New registration figures in recent times show the increase in popularity of wheel loaders, telehandlers and pivot steer loaders on Irish farms.
As a result, the number of machines on the used market has also increased. These used machines often tend to attract a different cohort of customers.
Farmers who do not require or maybe cannot justify a new machine tend to look to the secondhand market to satisfy their needs and budget.
The challenge is to locate a machine that has been well maintained and cared for.
The worldwide component shortages have limited the availability of new machines, which has also had a knock-on effect on the used market.
Over the past year or 18 months, the availability of used machines in dealers’ yards has become limited due to several factors such as Brexit and COVID-19.
Meanwhile, the price of used machinery has continued to increase in value in accordance with new machinery prices.
All that said, it is probably now as challenging as ever, if not more, to try to locate a good example of a used telehandler or pivot-steer loader.
In this article, we focus in particular on pivot-steer loaders, what to look out, what to be aware of and what to avoid.

The boom should be inspected for cracks or wear.
General condition
A first glance at the general condition of a machine will tell you a lot about how it has been treated.
Large body panels such as bonnets can be expensive to replace, so any damage should be taken into account.
Lights, mirrors and glassware should be intact. The machine should be started and let run for five to 10 minutes before test-driving. It is vital that the load monitor indicator (LMI) is working. This is a safety device that is present in all telehandlers.
It is worth keeping an eye out while examining the machine for plates and labels on components, checking that the date stamp matches the age of the machine.
For example, a 2010 machine with a component, such as a hydraulic pump, that has a plate stamped 2013 generally indicates that has been replaced at some point.
Down through the years, farmers have told us horror stories of used machines they purchased which seemed genuine, only to come across a next service due sticker/card in the cab or under the bonnet several months later with far more hours than they were led to believe upon purchasing.
Even with a rigorous inspection from an experienced person, it can be difficult to prove the genuine hours on a machine. And what’s more is that it might not be the seller who actually clocked the machine, but a previous owner.
However, this is where it pays to purchase machines from genuine dealers where you have a comeback.
Also, potential buyers should check that the serial numbers on the vehicle identification (VIN) plate match the serial numbers displayed elsewhere. Alert the dealer if there are any discrepancies.

The cab should be tidy with all switchgear working and a good seat.
Cab
Similar to exterior condition, the condition inside the cab gives a good indication of how well the machine was maintained by the previous owner(s).
The handbrake, for example, should be fully functional. Generally, an issue with the handbrake is as simple as replacing the cable.
All joystick functions, along with switch gear, should be tested, making sure everything does what is intended, including boom suspension and lights, etc.
The dashboard should be checked, ensuring there are no warning lights illuminated. The temperature gauge should be monitored and, unless being worked very hard, it should not pass the halfway mark. If fitted with a reversible fan, check that it is working.
Check for wear
Regular service intervals and consistent greasing will determine the lifespan of any machine.
The main points of wear and tear to watch out for on articulated loaders are the central pivot point, steering rams, bushes and pins. Such machines can be costly to re-bush, so take this into consideration.
If worn pins and bushes are left too long in need of replacement, then damage to the housing or frame can occur, resulting in a larger problem, which will likely require specialist attention.
Depending on the make and model, a new central pivot pin, bushings and bearings will set you back in the region of €950 plus VAT.
To check wear within the main pivot point, apply downwards pressure on the implement against the ground until it begins lifting the front wheels.
Have someone closely watch the pivot point for looseness. If the boom frame edges closer to the windscreen (more than 20mm), this is an indication of significant wear. Approach with caution and inform the seller.
Wear and tear on pins usually reveals one of two things: that the machine was poorly greased over its working life or that it has been subject to quite a bit of hard work.
A fresh machine with low hours shouldn’t need pins and bushes replaced if it has been well maintained.
That said, don’t be afraid of a machine that has had this work carried out if otherwise in good condition and the hours justify it.
Tyre condition will have a bearing on the valuation of the machine and will give a potential buyer a good indication of the hours the machine has clocked up.
The headstock on any type of loader usually ends up subject to the most wear and tear as result of bucket shaking and constant movement.
A lack of grease will always speed up the wear process that should take a number of years if well-greased.
Ensure the hydraulic locking pins are moving freely with no oil leaks. A new headstock will cost about €3,000 plus VAT.
The boom should be extended and inspected for any cracks, bends or any sideways or lateral moment.
Ideally, there should also be grease on the walls. A screeching nose when extending the boom will indicate a lack of grease. Most booms are fitted with wear pads, so check their condition.
Engine
Most importantly, the engine should be clean and dry and run well and not be too smoky. Potential buyers should ask about service intervals and check the oil by pulling the dipstick (when cold).
Most dealers tend to carry out an oil and fuel filter service before the machine is sold. If not, oil should have a good viscosity and not be overly black in colour. Gloopy, dark black oil indicates the engine has gone past its service interval.
Our advice if buying a machine is to have it fully serviced if unsure when that was last done.
The breather pipe on the underbody of the machine should be free of dripping oil or smoke. If smoke is coming out, it may indicate a number of possible issues, including head gasket problems.
The radiator should be inspected for damage. Coolant should be at the recommended level in the expansion bottle and not leaking. Open the bottle and inspect the coolant.
Coolant should show no signs of contaminants such as oil, or be rusty in colour. A machine with signs of oil present in its coolant should be avoided, as it generally tends to be a sign of head gasket failure.
A well-looked-after machine should have its coolant changed in line with the manufacturer’s recommended intervals.
The air filter should be checked to see if it is full of dust, another indication of how well the machine was looked after.
A blocked air breather will put a serious strain on both the turbo and the engine. Again, most reputable dealers will replace this as part of a pre-sale service.
Transmission and axles
The handiest way to check a power-shift transmission is to drive the machine forward and in reverse in each gear, which it should do smoothly and at its ease with no slippage.
Generally, if well-minded, a transmission should see a loader through its lifetime.
Depending on how many hours the machine has clocked up and the work it has carried out, the brakes may need to be replaced.
The brakes should react to force being applied to the pedal. Non-responsive brakes pose a serious safety hazard and will leave the buyer with a costly repair bill. Axle hubs should be checked for any leakages.
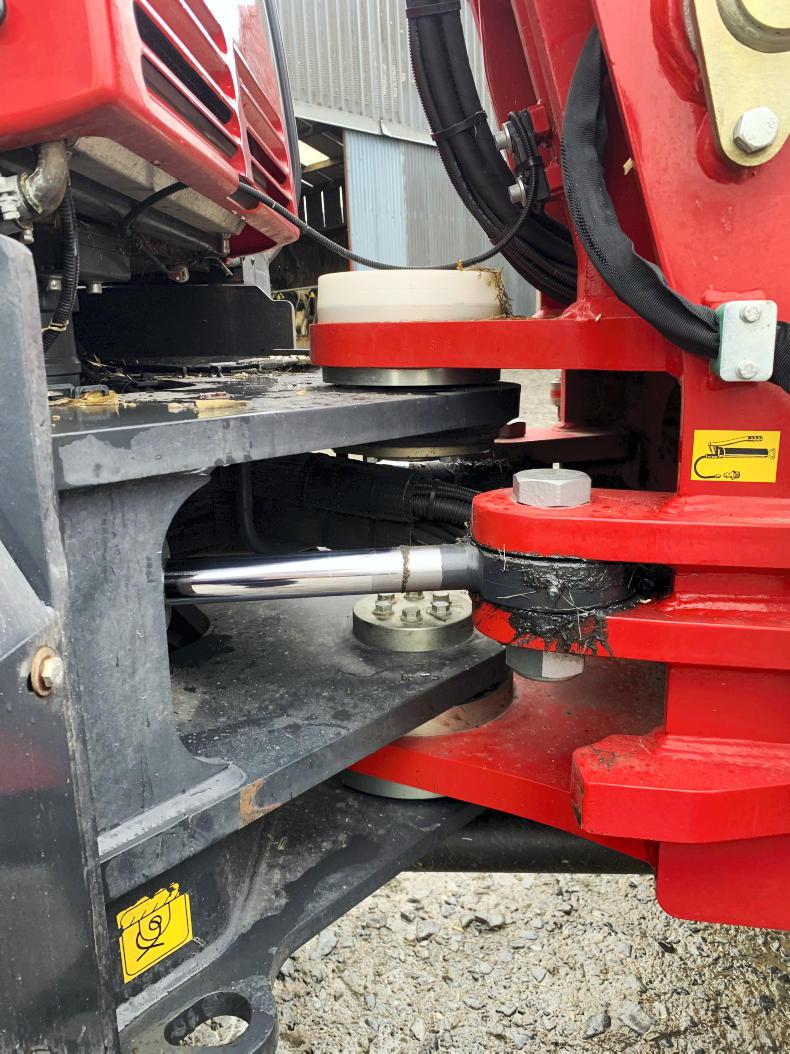
One of the most important points on a pivot-steer loader to examine is the pendulum joint.
Hydraulics
The easiest way to check the hydraulics is to test all functions and ensure they are responsive at the same time.
The boom should be extended while lifting and tilting it at the same time. These functions should work comfortably together. While test driving, test out the boom suspension that it works and engages and disengages as it should.
The hydraulic system should be checked for leaks and/or perished hoses. Ram seals should be checked for leaks too.
If an internal seal is damaged, it can be a costly job to replace and will leave the machine out of action for a period of time.
An overdue hydraulic oil and filter service interval will slow the hydraulic system and will give you an indication of how well the machine was cared for.
Most machines will have a sight glass where you can check the hydraulic oil level. The condition of the oil should also be checked. Milky looking oil is usually a sign that water has managed to get into the system.
New registration figures in recent times show the increase in popularity of wheel loaders, telehandlers and pivot steer loaders on Irish farms.
As a result, the number of machines on the used market has also increased. These used machines often tend to attract a different cohort of customers.
Farmers who do not require or maybe cannot justify a new machine tend to look to the secondhand market to satisfy their needs and budget.
The challenge is to locate a machine that has been well maintained and cared for.
The worldwide component shortages have limited the availability of new machines, which has also had a knock-on effect on the used market.
Over the past year or 18 months, the availability of used machines in dealers’ yards has become limited due to several factors such as Brexit and COVID-19.
Meanwhile, the price of used machinery has continued to increase in value in accordance with new machinery prices.
All that said, it is probably now as challenging as ever, if not more, to try to locate a good example of a used telehandler or pivot-steer loader.
In this article, we focus in particular on pivot-steer loaders, what to look out, what to be aware of and what to avoid.

The boom should be inspected for cracks or wear.
General condition
A first glance at the general condition of a machine will tell you a lot about how it has been treated.
Large body panels such as bonnets can be expensive to replace, so any damage should be taken into account.
Lights, mirrors and glassware should be intact. The machine should be started and let run for five to 10 minutes before test-driving. It is vital that the load monitor indicator (LMI) is working. This is a safety device that is present in all telehandlers.
It is worth keeping an eye out while examining the machine for plates and labels on components, checking that the date stamp matches the age of the machine.
For example, a 2010 machine with a component, such as a hydraulic pump, that has a plate stamped 2013 generally indicates that has been replaced at some point.
Down through the years, farmers have told us horror stories of used machines they purchased which seemed genuine, only to come across a next service due sticker/card in the cab or under the bonnet several months later with far more hours than they were led to believe upon purchasing.
Even with a rigorous inspection from an experienced person, it can be difficult to prove the genuine hours on a machine. And what’s more is that it might not be the seller who actually clocked the machine, but a previous owner.
However, this is where it pays to purchase machines from genuine dealers where you have a comeback.
Also, potential buyers should check that the serial numbers on the vehicle identification (VIN) plate match the serial numbers displayed elsewhere. Alert the dealer if there are any discrepancies.

The cab should be tidy with all switchgear working and a good seat.
Cab
Similar to exterior condition, the condition inside the cab gives a good indication of how well the machine was maintained by the previous owner(s).
The handbrake, for example, should be fully functional. Generally, an issue with the handbrake is as simple as replacing the cable.
All joystick functions, along with switch gear, should be tested, making sure everything does what is intended, including boom suspension and lights, etc.
The dashboard should be checked, ensuring there are no warning lights illuminated. The temperature gauge should be monitored and, unless being worked very hard, it should not pass the halfway mark. If fitted with a reversible fan, check that it is working.
Check for wear
Regular service intervals and consistent greasing will determine the lifespan of any machine.
The main points of wear and tear to watch out for on articulated loaders are the central pivot point, steering rams, bushes and pins. Such machines can be costly to re-bush, so take this into consideration.
If worn pins and bushes are left too long in need of replacement, then damage to the housing or frame can occur, resulting in a larger problem, which will likely require specialist attention.
Depending on the make and model, a new central pivot pin, bushings and bearings will set you back in the region of €950 plus VAT.
To check wear within the main pivot point, apply downwards pressure on the implement against the ground until it begins lifting the front wheels.
Have someone closely watch the pivot point for looseness. If the boom frame edges closer to the windscreen (more than 20mm), this is an indication of significant wear. Approach with caution and inform the seller.
Wear and tear on pins usually reveals one of two things: that the machine was poorly greased over its working life or that it has been subject to quite a bit of hard work.
A fresh machine with low hours shouldn’t need pins and bushes replaced if it has been well maintained.
That said, don’t be afraid of a machine that has had this work carried out if otherwise in good condition and the hours justify it.
Tyre condition will have a bearing on the valuation of the machine and will give a potential buyer a good indication of the hours the machine has clocked up.
The headstock on any type of loader usually ends up subject to the most wear and tear as result of bucket shaking and constant movement.
A lack of grease will always speed up the wear process that should take a number of years if well-greased.
Ensure the hydraulic locking pins are moving freely with no oil leaks. A new headstock will cost about €3,000 plus VAT.
The boom should be extended and inspected for any cracks, bends or any sideways or lateral moment.
Ideally, there should also be grease on the walls. A screeching nose when extending the boom will indicate a lack of grease. Most booms are fitted with wear pads, so check their condition.
Engine
Most importantly, the engine should be clean and dry and run well and not be too smoky. Potential buyers should ask about service intervals and check the oil by pulling the dipstick (when cold).
Most dealers tend to carry out an oil and fuel filter service before the machine is sold. If not, oil should have a good viscosity and not be overly black in colour. Gloopy, dark black oil indicates the engine has gone past its service interval.
Our advice if buying a machine is to have it fully serviced if unsure when that was last done.
The breather pipe on the underbody of the machine should be free of dripping oil or smoke. If smoke is coming out, it may indicate a number of possible issues, including head gasket problems.
The radiator should be inspected for damage. Coolant should be at the recommended level in the expansion bottle and not leaking. Open the bottle and inspect the coolant.
Coolant should show no signs of contaminants such as oil, or be rusty in colour. A machine with signs of oil present in its coolant should be avoided, as it generally tends to be a sign of head gasket failure.
A well-looked-after machine should have its coolant changed in line with the manufacturer’s recommended intervals.
The air filter should be checked to see if it is full of dust, another indication of how well the machine was looked after.
A blocked air breather will put a serious strain on both the turbo and the engine. Again, most reputable dealers will replace this as part of a pre-sale service.
Transmission and axles
The handiest way to check a power-shift transmission is to drive the machine forward and in reverse in each gear, which it should do smoothly and at its ease with no slippage.
Generally, if well-minded, a transmission should see a loader through its lifetime.
Depending on how many hours the machine has clocked up and the work it has carried out, the brakes may need to be replaced.
The brakes should react to force being applied to the pedal. Non-responsive brakes pose a serious safety hazard and will leave the buyer with a costly repair bill. Axle hubs should be checked for any leakages.
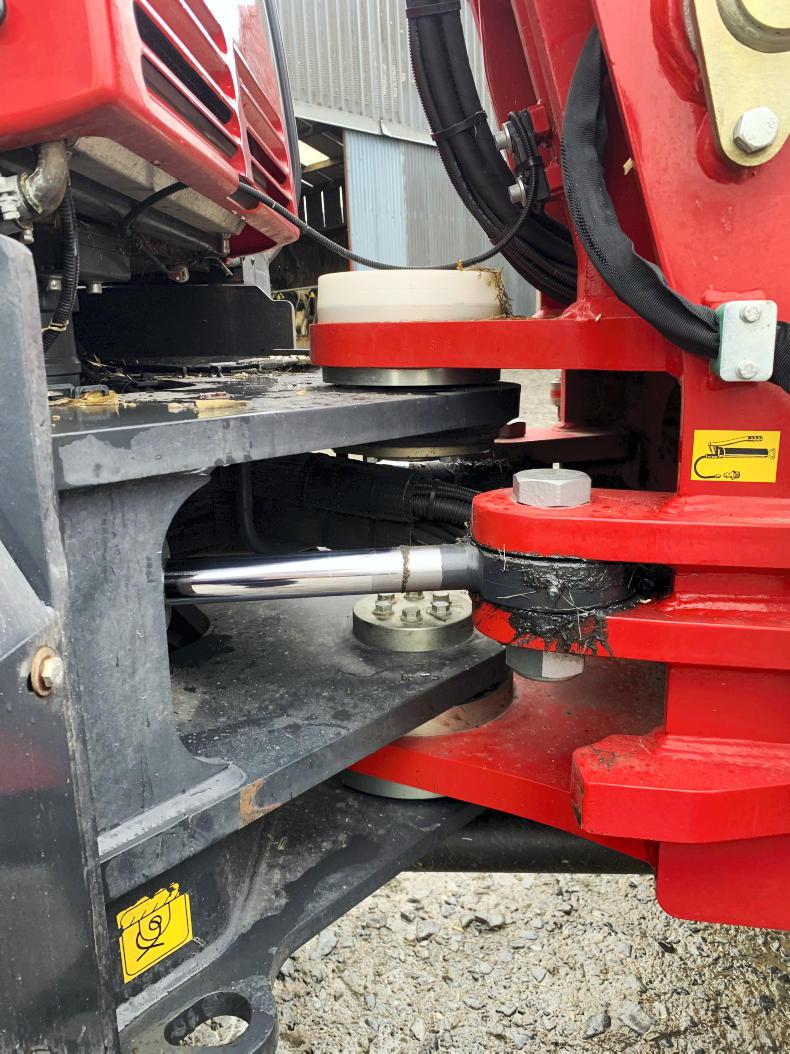
One of the most important points on a pivot-steer loader to examine is the pendulum joint.
Hydraulics
The easiest way to check the hydraulics is to test all functions and ensure they are responsive at the same time.
The boom should be extended while lifting and tilting it at the same time. These functions should work comfortably together. While test driving, test out the boom suspension that it works and engages and disengages as it should.
The hydraulic system should be checked for leaks and/or perished hoses. Ram seals should be checked for leaks too.
If an internal seal is damaged, it can be a costly job to replace and will leave the machine out of action for a period of time.
An overdue hydraulic oil and filter service interval will slow the hydraulic system and will give you an indication of how well the machine was cared for.
Most machines will have a sight glass where you can check the hydraulic oil level. The condition of the oil should also be checked. Milky looking oil is usually a sign that water has managed to get into the system.
SHARING OPTIONS: