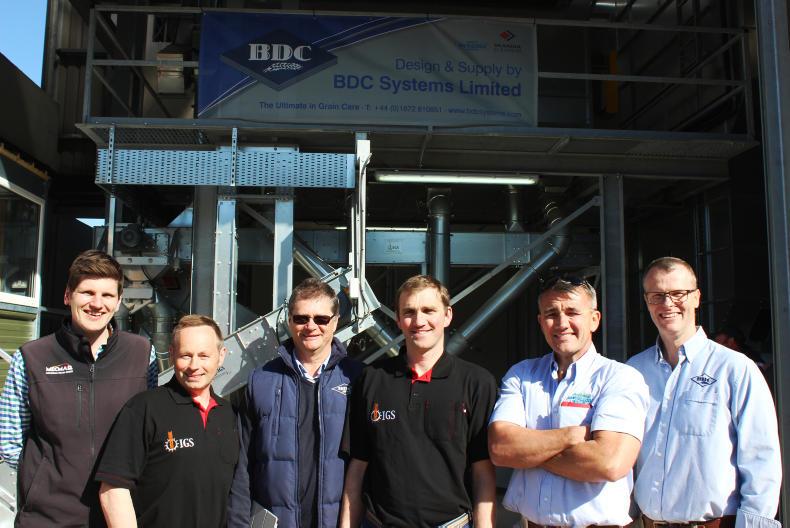
LOYALTY CODE:
The paper code cannot be redeemed when browsing in private/incognito mode. Please go to a normal browser window and enter the code there
This content is copyright protected!
However, if you would like to share the information in this article, you may use the headline, summary and link below:
Title: Grain store’s state-of-the-art construction
The availability of grants for grain storage under the new TAMS for tillage scheme will generate an amount of interest in both new store construction and the installation of handling equipment.
https://www.farmersjournal.ie/grain-store-s-state-of-the-art-construction-280478
ENTER YOUR LOYALTY CODE:
The reader loyalty code gives you full access to the site from when you enter it until the following Wednesday at 9pm. Find your unique code on the back page of Irish Country Living every week.
CODE ACCEPTED
You have full access to farmersjournal.ie on this browser until 9pm next Wednesday. Thank you for buying the paper and using the code.
CODE NOT VALID
Please try again or contact us.
For assistance, call 01 4199525
or email subs@farmersjournal.ie
Sign in
Incorrect details
Please try again or reset password
If would like to speak to a member of
our team, please call us on 01-4199525
Reset
password
Please enter your email address and we
will send you a link to reset your password
If would like to speak to a member of
our team, please call us on 01-4199525
Link sent to
your email
address
We have sent an email to your address.
Please click on the link in this email to reset
your password. If you can't find it in your inbox,
please check your spam folder. If you can't
find the email, please call us on 01-4199525.
Email address
not recognised
There is no subscription associated with this email
address. To read our subscriber-only content.
please subscribe or use the reader loyalty code.
If would like to speak to a member of
our team, please call us on 01-4199525
Update Success !
It’s seldom that we get the opportunity to visit an open day at a totally new grain-drying facility. While such a visit may not be of interest to everyone in the business, those who attended the event in early May will agree that this was an exceptional setup.
The event was hosted by the Hobson family, who bought the old Warrenstown College farm, plus other land in the area. The farm is now basically in tillage and the majority of the old farmyard buildings were unsuitable for grain storage. So the decision was made to knock a number of the existing buildings and to replace them with modern and purpose-built facilities.
This development was carried out in conjunction with well-known Co Louth builder Gerard King of Ashville Construction. For me, this development is a prime example of the benefit of working with someone who has a lot of experience of building in farmyards and the need to have a bigger plan than just one building.
Started with a basic sketch
Gerard told me that when he first met up with the Hobsons, he started with a sketch on a piece of paper and attempted to make best use of the space and natural falls that existed in different parts of the farmyard.
This resulted in some split-level construction which proved useful for fitting the new Svegma continuous-flow grain dryer under the same roofline as the store.
As well as in the grain stores, strongly reinforced walls are used in other parts of the farmyard to facilitate the split-level construction. The farmyard redevelopment is being done on a continuous basis. Two stores were built initially back in 2009/2010, another was built in 2013 and a new state-of-the-art store and drying and cleaning unit has now been completed.
The opportunity for people to see this facility is timely, given the new grant options available through TAMS for tillage. On the day, people could see quality store construction along with the new underfloor ducting technology from King Grain Ventilation.
Galco was also on hand to discuss the galvanising of the very many metal components and there were people from Calor to talk about gas as the fuel for grain drying. All of these provided interesting and useful information for people considering a new store in the near future.
Many features
Irish Grain Systems promoted the open day and they had fitted all of the equipment relating to grain drying and movement in the stores. There were a number of elements of the unit that I noted as interesting.
The storage capacity was built as a number of different stores rather than just one big store. This can be a great help where segregation is needed, either for different crops or varieties of a crop.
All stores are fitted with underfloor ventilation and the vents are common across all three stores. This allows the air to be propelled from one side or the other but it also provides the capability of splitting a store along its length with a moveable wall and allows half the width of the store to be ventilated by blocking the centre of each duct. All ducts can be shut off at the wind tunnels as required.
This meant that the construction had to incorporate an air tunnel at both side of each store. I reckon this made the investment a bit more costly but the added flexibility could well pay for itself in time. It is more likely that it will be the smaller niche tonnage that will carry the price premium.
Grain handling
Grain intake did not involve a deep hopper but rather a conveyor at the bottom of a shallow but wide drop through a very robust grid. This conveyor operates at the level of the floor in the adjoining dryer house, so accessibility would not be a huge issue in the event of breakage or blockage.
Once grain comes into the dryer house, it is elevated, moved through an aspirator to remove dust, etc, and then it could be passed through a cylindrical pre-cleaner if and when necessary. Pre-cleaning was considered to be particularly important as oats is one of the crops to be dried in the plant.
Dust, light material and oversize material can be removed by the aspirator and cleaner units and this material is then moved by blower pipes to an adjoining dust store fitted with a roller door.
The main vertical elevation is done using a combination of bucket elevators and Skandia curved conveyors. This is to prevent having to run elevators up through roofs or down into pits in the ground. The Svegma dryer is rated at 27t/hr from 20% to 15% moisture so arguably this sets the maximum throughput of the unit. However, there will be times when grain will come in at lower moisture so the handling equipment needs to be rated above the drying capacity.
Indeed, James Connor of IGS said that all the elevation and grain movement equipment is rated at 60t/hr. The design of the system allows John Hobson to run dried grain from his store back through the unit again for further grading and cleaning at a later date. The pre-cleaner can also be used as a grading machine by changing the sieve size on the cylinders and this can be done without having to put the grain back through the dryer.
Grain from the dryer is taken by angled conveyor up on to the central belt conveyor in the main store. From here it can be dropped off at any point along the length of the store and this is controlled using a remote control key fob. Controlling this is essential to help ensure a uniform fill of the store. There are also plans to fit another conveyor at the end of this one to move the grain from this into the two adjoining stores. This would then feed on to other centrally mounted conveyors to fill these stores.
The controls for the full grain movement, cleaning and drying are contained on a dual console and clearly marked control panels. As in all modern systems, these enable the operator to turn on or off motors to move grain to whatever destination is required.
This was a very impressive set-up but perhaps outside the scope of most growers. Asked what it might cost to replicate the grain handling system in another farmer’s yard, James Connor of IGS said that every job will have different specific requirements but said that a similar project would cost in the order of €230,000.
New vent design
Details of the store itself were carried in an article by Peter Varley on 22 April. I was particularly interested in the new venting system manufactured by King Grain Ventilation. This was precision in terms of how the vents were installed in the floor.
A frame is built for the vents using angle iron and this has lugs welded on to fix it into the concrete on both sides. The vents themselves use a completely new concept of lateral covers designed and made by King Grain.
Individual units are pressed out in segments and formed in 1m lengths. When these are fitted into the frame built into the floor, they sit perfectly flush with floor level for ease of loading, cleaning, etc. This system also means that installation and removal of the vents is a relatively small job compared with having individual choc bars.
The individual vent is pressed steel but each downward vent press leaves a little trough at its base. This means that small seeds like oilseed rape will sit in the trough and prevent others from falling through the vent into the duct itself.
Mecmar mobiles
While a Svegma continuous flow dryer was installed in the new store, IGS also brought Mecmar mobile batch dryers to the event. These are an impressive-looking dryer and are part of the array of kit that is grant aided by the new TAMS for tillage scheme. This scheme will cover the erection of new grain stores or the installation of dryers, conveyers and other retro-fit components into a grain facility. However, it does not cover improvements to existing stores, such as a new roof or ventilated floor unless they are part of a whole new construction project. Those present indicated considerable interest in both building and equipment and so this event proved particularly useful for interested parties.
SHARING OPTIONS: