Slowly, Ireland’s architects, engineers and designers are using more wood, especially in construction, but we lag well behind most European countries.
This is understandable as Ireland has a masonry rather than a wood culture and has traditionally lacked the supply and the diversity of raw material necessary to promote widespread timber usage and design in construction, furniture and other applications.
The winners of Wood Awards Ireland (WAI) 2020 demonstrate the range of wood usage now being achieved in Ireland from small-scale craft and design to substantial construction projects.
This week we give examples of the potential of large-scale industrial usage of timber while next week we explore smaller wood projects using broadleaves or hardwoods and minor coniferous or softwood species.
Large-scale projects
Ireland is not alone in its dependence on fossil-based materials but countries such as Canada, Austria, Germany, Sweden, Norway and Finland are now building innovatively and big with wood as an inherent medium in construction projects. Buildings over 80m tall have been completed in Norway and Austria with up to 75% softwood content. These have been achieved by engineering wood to increase its strength so that it can form the structural element of medium- to high-rise buildings. The two most common engineered wood products are glue-laminated (glulam) and cross-laminated timber (CLT).
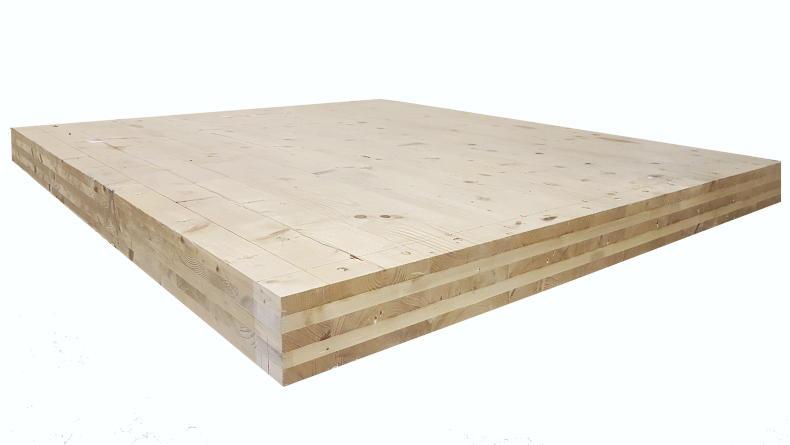
CLT is a multi-layer panel product made of at least three orthogonally bonded layers of timber (five here). Sitka spruce is suitable for CLT which provides exceptional rigidity and dimensional stability. \NUI Galway
International wood constructions projects aim to build much higher than 80m. For example, Sumitoma Forestry, the Japanese logging, timber processing and construction company, plans to build a 350m skyscraper in 2041 to mark the corporation’s 350th anniversary. The building will contain 90% timber.
CLT spruce research
The Timber Engineering Research Group at NUI Galway won the WAI innovative category by demonstrating the structural benefits of engineered wood and how Irish-grown Sitka spruce is suitable for CLT. The project team led by Dr Conan O’Ceallaigh and Prof Annette M Harte explained how “CLT is a multi-layer panel product made of at least three orthogonally bonded layers of timber, which has exceptional rigidity and dimensional stability”.
It is now beginning to displace carbon-intensive steel and concrete in demanding structural applications such as multi-storey buildings
CLT is precision-manufactured offsite, thereby maximising efficiency by improving construction and delivery times and also reducing labour costs. CLT has a major role to play in climate change mitigation.
“It is now beginning to displace carbon-intensive steel and concrete in demanding structural applications such as multi-storey buildings,” said Dr O’Ceallaigh.
“In central Europe and Scandinavia, CLT is primarily manufactured from grade C24 European spruce. With forecasts predicting large increases in Irish timber coming to the market over the coming decades, significant opportunities exist for the Irish wood products sector including the potential use of Irish-grown timber to manufacture CLT.”
The NUI Galway study has established the viability of using grade C16 Sitka spruce to produce structural CLT panels. The study examined suitable adhesives and the load capacity of CLT floor systems.
Thickness
“When compared to commercial CLT panels made from C24 timber, the C16 [Irish] panels required an increase in thickness of less than 12% to achieve the same performance,” maintained Dr O’Ceallaigh.
“Additionally, current steel fastener technology has been shown to be suitable for connections between Irish CLT panels.”
With production from Irish forests forecast to almost double by 2030, Sitka spruce CLT could transform the Irish construction market as most of the increased timber yield will comprise Sitka.
Center Parcs wins overall award for excellence in timber construction and design
Center Parcs Ireland was chosen as the overall winner of WAI 2020. Completed by John Sisk & Son (Holdings) Ltd with Holder Mathias Architects and Peter Brett Associates, this large-scale leisure project explored wood in all its forms from solid timber to engineered wood comprising glulam and CLT.
The €233m resort includes 466 self-catering lodges and 30 apartments
Located near Ballymahon, Co Longford, Center Parcs provides a world-class family holiday destination within Ireland, a real alternative to overseas family breaks.
The €233m resort includes 466 self-catering lodges and 30 apartments. The lodges were designed and built in strict accordance with Irish Building Regulations and are A2 energy rated.
The imported wood was in rough sawn format, which was then manufactured in an Irish sawmill to a wide range of different sizes.
Once machined, the wood was treated with the wood preservative Celcure M65 to increase its durability and lifespan.
Treatment of the wood well in advance of delivery to site was critical in order to ensure correct moisture content for installation during different times of the year.
This can be particularly challenging on Irish sites, especially during winter months when the levels of moisture are particularly high, so careful planning was required to ensure timely supply to site of seasoned materials.
All wood used in the project was certified by the Forest Stewardship Council (FSC) and Programme for the Endorsement of Forest Certification (PEFC)
Wiehag was the specialist Austrian subcontractor employed to deliver the glulam and CLT packages for the Subtropical Swimming Paradise (STSP), which is the focal point of the Center Parcs development.
Wiehag developed a 3D model for the glulam and CLT superstructure of the STSP. This was fabricated with the main substructure 3D model – produced by the design team – to ensure that the critical interface between the glulam curved arches and the reinforced concrete buttress columns was managed effectively.
All wood used in the project was certified by the Forest Stewardship Council (FSC) and Programme for the Endorsement of Forest Certification (PEFC).
Most of the species originated in Europe or North America including Norway spruce, European and Siberian larch and western red cedar The plywood species was Elliotis pine from the US, while timber for decking included FSC-certified redwood from the US and PEFC-certified bangkirai, a southeast Asian hardwood.
Slowly, Ireland’s architects, engineers and designers are using more wood, especially in construction, but we lag well behind most European countries.
This is understandable as Ireland has a masonry rather than a wood culture and has traditionally lacked the supply and the diversity of raw material necessary to promote widespread timber usage and design in construction, furniture and other applications.
The winners of Wood Awards Ireland (WAI) 2020 demonstrate the range of wood usage now being achieved in Ireland from small-scale craft and design to substantial construction projects.
This week we give examples of the potential of large-scale industrial usage of timber while next week we explore smaller wood projects using broadleaves or hardwoods and minor coniferous or softwood species.
Large-scale projects
Ireland is not alone in its dependence on fossil-based materials but countries such as Canada, Austria, Germany, Sweden, Norway and Finland are now building innovatively and big with wood as an inherent medium in construction projects. Buildings over 80m tall have been completed in Norway and Austria with up to 75% softwood content. These have been achieved by engineering wood to increase its strength so that it can form the structural element of medium- to high-rise buildings. The two most common engineered wood products are glue-laminated (glulam) and cross-laminated timber (CLT).
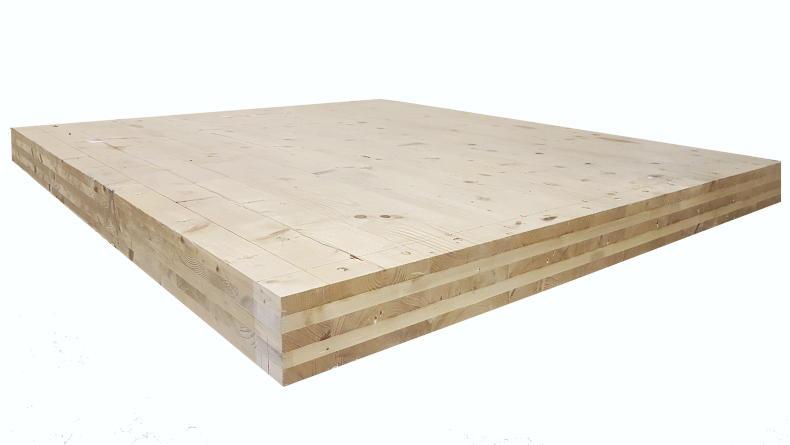
CLT is a multi-layer panel product made of at least three orthogonally bonded layers of timber (five here). Sitka spruce is suitable for CLT which provides exceptional rigidity and dimensional stability. \NUI Galway
International wood constructions projects aim to build much higher than 80m. For example, Sumitoma Forestry, the Japanese logging, timber processing and construction company, plans to build a 350m skyscraper in 2041 to mark the corporation’s 350th anniversary. The building will contain 90% timber.
CLT spruce research
The Timber Engineering Research Group at NUI Galway won the WAI innovative category by demonstrating the structural benefits of engineered wood and how Irish-grown Sitka spruce is suitable for CLT. The project team led by Dr Conan O’Ceallaigh and Prof Annette M Harte explained how “CLT is a multi-layer panel product made of at least three orthogonally bonded layers of timber, which has exceptional rigidity and dimensional stability”.
It is now beginning to displace carbon-intensive steel and concrete in demanding structural applications such as multi-storey buildings
CLT is precision-manufactured offsite, thereby maximising efficiency by improving construction and delivery times and also reducing labour costs. CLT has a major role to play in climate change mitigation.
“It is now beginning to displace carbon-intensive steel and concrete in demanding structural applications such as multi-storey buildings,” said Dr O’Ceallaigh.
“In central Europe and Scandinavia, CLT is primarily manufactured from grade C24 European spruce. With forecasts predicting large increases in Irish timber coming to the market over the coming decades, significant opportunities exist for the Irish wood products sector including the potential use of Irish-grown timber to manufacture CLT.”
The NUI Galway study has established the viability of using grade C16 Sitka spruce to produce structural CLT panels. The study examined suitable adhesives and the load capacity of CLT floor systems.
Thickness
“When compared to commercial CLT panels made from C24 timber, the C16 [Irish] panels required an increase in thickness of less than 12% to achieve the same performance,” maintained Dr O’Ceallaigh.
“Additionally, current steel fastener technology has been shown to be suitable for connections between Irish CLT panels.”
With production from Irish forests forecast to almost double by 2030, Sitka spruce CLT could transform the Irish construction market as most of the increased timber yield will comprise Sitka.
Center Parcs wins overall award for excellence in timber construction and design
Center Parcs Ireland was chosen as the overall winner of WAI 2020. Completed by John Sisk & Son (Holdings) Ltd with Holder Mathias Architects and Peter Brett Associates, this large-scale leisure project explored wood in all its forms from solid timber to engineered wood comprising glulam and CLT.
The €233m resort includes 466 self-catering lodges and 30 apartments
Located near Ballymahon, Co Longford, Center Parcs provides a world-class family holiday destination within Ireland, a real alternative to overseas family breaks.
The €233m resort includes 466 self-catering lodges and 30 apartments. The lodges were designed and built in strict accordance with Irish Building Regulations and are A2 energy rated.
The imported wood was in rough sawn format, which was then manufactured in an Irish sawmill to a wide range of different sizes.
Once machined, the wood was treated with the wood preservative Celcure M65 to increase its durability and lifespan.
Treatment of the wood well in advance of delivery to site was critical in order to ensure correct moisture content for installation during different times of the year.
This can be particularly challenging on Irish sites, especially during winter months when the levels of moisture are particularly high, so careful planning was required to ensure timely supply to site of seasoned materials.
All wood used in the project was certified by the Forest Stewardship Council (FSC) and Programme for the Endorsement of Forest Certification (PEFC)
Wiehag was the specialist Austrian subcontractor employed to deliver the glulam and CLT packages for the Subtropical Swimming Paradise (STSP), which is the focal point of the Center Parcs development.
Wiehag developed a 3D model for the glulam and CLT superstructure of the STSP. This was fabricated with the main substructure 3D model – produced by the design team – to ensure that the critical interface between the glulam curved arches and the reinforced concrete buttress columns was managed effectively.
All wood used in the project was certified by the Forest Stewardship Council (FSC) and Programme for the Endorsement of Forest Certification (PEFC).
Most of the species originated in Europe or North America including Norway spruce, European and Siberian larch and western red cedar The plywood species was Elliotis pine from the US, while timber for decking included FSC-certified redwood from the US and PEFC-certified bangkirai, a southeast Asian hardwood.
SHARING OPTIONS: