Joseph Walls Ltd is a family-run Agri Merchants serving the counties of Down, Tyrone, Armagh and Louth through its three depots in Hilltown, Clough and Dundalk. Now in its second generation, the business is headed up by Christopher Walls with the help of his father Joseph.
“Fertiliser, lime and grass seed are the core elements of the business. Not only do we supply but we also offer customers the service of spreading each of these inputs, especially lime which on average usually amounts to 20,000t each year. We also contract spread fertiliser for farmers,” Christopher stated.

Even though conditions were windy when we visted, dust was still greatly reduced due to the auger system
While the one mounted KRM Bogballe spreader takes care of all fertiliser applications, four lime spreaders are more often than not on the go. Up until last year, the Walls had run all Bredal machines, mainly K40s. Prior to this, in the earlier years it would have been Atkinson spreaders.
Why SpreadPoint?
Last year, Christopher made the decision to break the mould and upgrade two of the Bredal K40 machines for two new SpreadPoint SP-600 spreaders fitted with SX-A 12m auger systems. Aside from the benefit of being built within the county, the firm’s auger concept was a major selling point.
He said: “With lime, there’s always going to be dust. But if it can be suppressed then straightaway it’s a major benefit in more ways than one. The first initial benefits were the reduction of dust while spreading in residential areas and the ability to spread on windier days. Having followed its development, we then went to see the auger system working and were well impressed.”

Even though conditions were windy when we visted, dust was still greatly reduced due to the auger system
Having felt that the design and build quality were unmatched by any other machine on the market, a deal was later struck to buy two identical SP-600 model 6m3 spreaders fitted with SX-A 12m folding auger applicators and a CV-650 mobile belt elevator.
We visited the spreaders in action, spreading in conditions one would describe as too windy for a conventional disc machine, straightaway proving the benefit of the auger concept.
Design and features
The SP-600 sits above the 4m3 SP-400 model and under the tandem-axle 9m3 SP-900 model as the middle offering within the SpreadPoint range. As standard the SP-600 is equipped with a 10-stud commercial axle, hydraulic drive, hydraulic rear door and a sprung drawbar. SpreadPoint opted for a monocoque chassis which is designed to provide a high strength to weight ratio. The spreader has an unladen weight of 3t.

Since delivery last July, each of the spreaders have spread over 10,000t.
SpreadPoint has cleverly designed its SP spreader range with modularity in mind. Operators have the option to change rear spreading attachments. For instance a customer can opt for the traditional SP-A heavy duty twin-disc system, and at a later stage fit the SX-A 12m folding auger applicator or the SD-A single-disc spreading unit for salting/gritting roads. This was a feature Christopher praised in the SpreadPoint design.

The mobile elevator can load a spreader in under three minutes.
Customers can choose between an RDS control terminal or Isobus control, meaning the spreader is controlled via the tractor’s terminal. Running the spreaders on two full Isobus New Holland ‘Blue Power’ tractors, Christopher opted for the latter option.
To achieve the correct application rate, the spreaders can then be operated in one of three ways. Firstly, using a fixed belt speed and fixed forward speed to maintain the set application rate or secondly, via SensePoint rate control. Once the density of the material is known, belt speed is automatically adjusted to match the tractor’s forward speed.
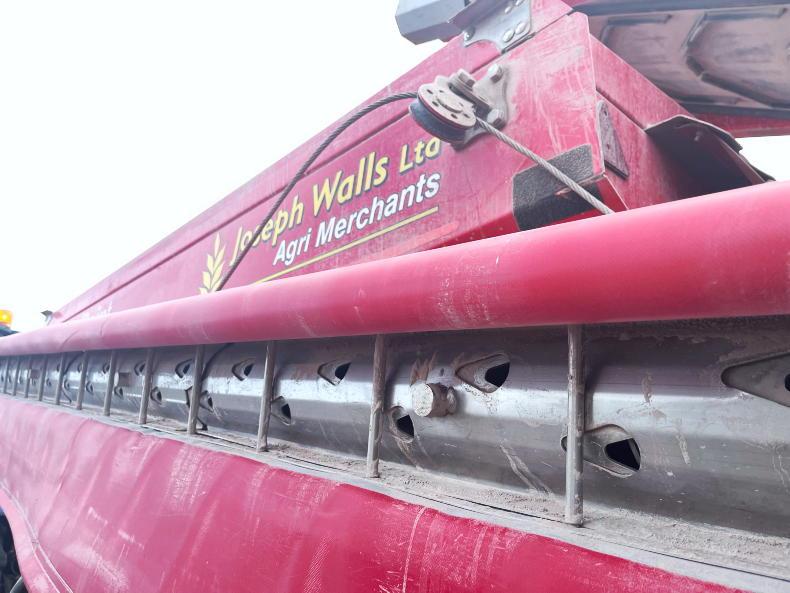
Lime is dropped through the series of holes on the underside of the auger.
Finally, the WeighPoint control option uses load cells to constantly monitor the remaining weight and the quantity spread over a certain time period and continually adjust belt speed according to the set application rate if needs be. Both SensePoint and WeighPoint systems are capable of variable-rate spreading where prescription maps are available.
Both Christopher and spreader operator Ian McDowell complimented the SensePoint system. “The SensePoint system proves accurate once properly calibrated and the load weight is inputted. It’s usually always within 100-150kg of being truly accurate, which can’t be argued with,” Ian stated.
There has been no interest among farmers, especially grassland for variable rate lime applications according to Christopher, a service he believes at the moment doesn’t justify the additional cost in most situations once lime remains cheap relative to chemical fertiliser.

Both boom sections are fitted with a 150mm diameter stainless steel auger, each driven by a hydraulic motor.
Other functions of the control screen include the control of hydraulic boom movements, control of hydraulic motor speeds as well as other features such as the recording of job-specific data – weight, spread etc. Both Christopher and Ian complimented the Isobus control screens and the ease of adjustment, which is done from the driver’s seat.
Auger system
The auger system consists of two separate 6m stainless steel booms, one to the left and one to the right.
Within each is a 150mm diameter stainless steel auger fabricated with 6mm welded flights. Both left and right augers have their own hydraulic motors to provide rotation.
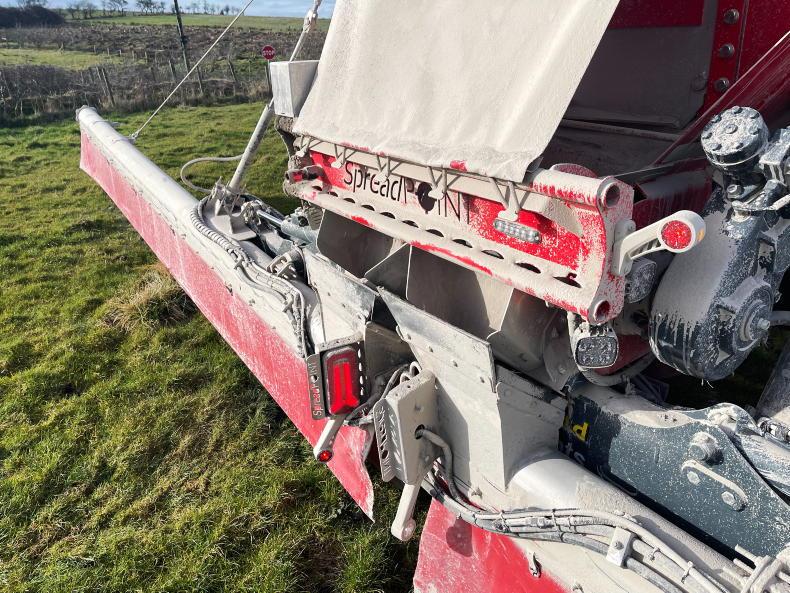
The boom sections fold down and around into working position independantly.
Once the lime falls off the central floor belt it lands in a small receiving hopper at the end of each boom section.

Christopher Walls, Joseph Walls Agri Merchants.
It is then carried by the auger and dropped through the series of outlet holes on the lower side of the auger housing across the 12m total working width. The process is not too dissimilar to a dribble bar system on a slurry tanker. According to SpreadPoint, the choice of full stainless steel is because of lime’s corrosive nature.

Both Christopher's machines are operated via Isobus which is a clean well laid out system he explained.
The adjustable hole arrangement on the auger housing helps tune the spread pattern. SpreadPoint claims this helps reduce the “lining” effect sometimes associated with auger applicators.
Meanwhile, subsequent calibrations of the spread pattern can be done from the cab via the Isobus terminal by adjusting auger speed. From the terminal, operators can see the live application rate alongside the target rate. Application rates up to 5,000kg/ha at speeds of up to 14km/h can be achieved.

Christopher uses two New Holland T7.225 AutoCommand tractors to run the 6m3 spreaders.
One of the few downsides of the auger system is that lime needs to be stone free which, according to Christopher, is hard to guarantee. In the event a stone enters the auger, it then has to be manually reversed from its outer end using a large wrench until the blockage is freed. While each 6m boom can be raised and lowered independently, they cannot spread independently. To help reduce drift, trailing PVC curtains typically run approximately 800mm above the ground.
Rear door position is also displayed on screen via a position sensor mounted on the hydraulic ram. Designed largely for variable-rate applications, the door settings can be adjusted on the move.
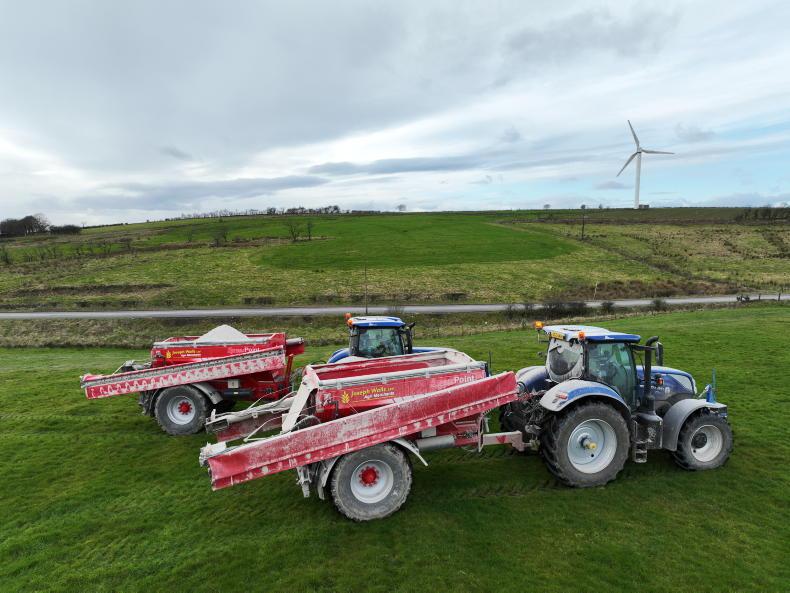
A third identical spreader and mobile elevator is expected to join the fleet in the coming weeks.
However, the system doesn’t suit all situations which Christopher and his team have found out, especially where there are considerable dips and hollows. The booms do not have a break-back feature so operators need to be conscious of undulating terrain. That said, each side can be raised up via tilt rams to avoid surface contact in most situations.
Other features
Aside from an inline hydraulic filter, a pressure gauge is present to show whether or not the auger is blocked.
If blocked, oil is diverted via pressure relief valve. The neat geometry of the booms allow them to fold within 2.7m for transport.

Operators need to be concious of the tail swing from the booms when in transport position.
However, the operator needs to be conscious of boom length especially when leaving gaps, Christopher said. In addition to ball and spoon hitches, Christopher opted for two rear cameras on each machine.
Elevator
While the majority of Irish contractors operate a loading shovel to load spreaders, the Walls don’t.
The benefit of proving the entire service means that they have control over transport and spreading. In order to be more efficient, mobile elevators have always been used. Both spreaders are piped with connections to both tow and power the elevator. Lime is seamlessly unloaded from the truck and into the spreader.

The spreader is equipped with load sensing hydraulics and its own inline hydraulic filter.
Aside from eliminating a loading shovel and an additional operator, Christopher describes the elevators as a cleaner process which provides the ability to load spreaders at the field along the side of a road instead of having to drive miles to a farmyard.
The CV-650 elevator works hand in hand with the spreaders and has the ability to fill each spreader in under three minutes.

The 800mm curtain prevents any drift as the lime is dropped onto the surface.
After spreading 10,000t with each spreader since delivery last July, Christopher and Joseph are more than happy with their performance. “The spreaders have worked a treat. Having come from a pto-driven basic spreader, the difference is night and day. The augers have proved a great job so far combined with the fact everything is controlled and adjusted from the cab. Having come from 7t machines, the additional capacity now sees an artic emptied in three spreader loads, speeding up the job.
“There are a number of benefits to the auger system, the main benefit being dust suppression, especially in residential areas. Given that lime is being vertically dropped, the spread pattern is much more even and accurate.

The 800mm curtain prevents any drift as the lime is dropped onto the surface.
“As expected, a more highly skilled operator is needed to manage the auger system and it is a system that doesn’t suit every field, especially smaller fields with dips and hollows.
“It’s early days yet but I’d expect running costs are going to be higher. Aside from regular greasing, the spreaders have worked maintenance-free so far.

The mobile elevator leaves for quick mess free loading according to Christopher.
“The auger system is going to become more popular without doubt. Already this year there have been farmers requesting the auger system. However, we’ll always keep a standard twin-disc machine for certain jobs. To cope with increasing demand we have another identical spreader and elevator ordered which is expected to arrive now in the coming weeks.
“Overall, the spreaders have been a substantial investment for the business but it’s important we provide the best service possible. Farmers have really seen the importance of lime spreading in recent years, especially with the price of chemical fertiliser.”

The mobile elevator leaves for quick mess free loading according to Christopher.
Model: SP-600 with SX-A 12m folding auger systems.
Spreader capacity: 6m3.
Drive method: hydraulic.
Working width: 12m.
Controls: Isobus.
Rate control: SensePoint Intelligent Control.
Tyres: 650/65 R30.5.
Joseph Walls Ltd is a family-run Agri Merchants serving the counties of Down, Tyrone, Armagh and Louth through its three depots in Hilltown, Clough and Dundalk. Now in its second generation, the business is headed up by Christopher Walls with the help of his father Joseph.
“Fertiliser, lime and grass seed are the core elements of the business. Not only do we supply but we also offer customers the service of spreading each of these inputs, especially lime which on average usually amounts to 20,000t each year. We also contract spread fertiliser for farmers,” Christopher stated.

Even though conditions were windy when we visted, dust was still greatly reduced due to the auger system
While the one mounted KRM Bogballe spreader takes care of all fertiliser applications, four lime spreaders are more often than not on the go. Up until last year, the Walls had run all Bredal machines, mainly K40s. Prior to this, in the earlier years it would have been Atkinson spreaders.
Why SpreadPoint?
Last year, Christopher made the decision to break the mould and upgrade two of the Bredal K40 machines for two new SpreadPoint SP-600 spreaders fitted with SX-A 12m auger systems. Aside from the benefit of being built within the county, the firm’s auger concept was a major selling point.
He said: “With lime, there’s always going to be dust. But if it can be suppressed then straightaway it’s a major benefit in more ways than one. The first initial benefits were the reduction of dust while spreading in residential areas and the ability to spread on windier days. Having followed its development, we then went to see the auger system working and were well impressed.”

Even though conditions were windy when we visted, dust was still greatly reduced due to the auger system
Having felt that the design and build quality were unmatched by any other machine on the market, a deal was later struck to buy two identical SP-600 model 6m3 spreaders fitted with SX-A 12m folding auger applicators and a CV-650 mobile belt elevator.
We visited the spreaders in action, spreading in conditions one would describe as too windy for a conventional disc machine, straightaway proving the benefit of the auger concept.
Design and features
The SP-600 sits above the 4m3 SP-400 model and under the tandem-axle 9m3 SP-900 model as the middle offering within the SpreadPoint range. As standard the SP-600 is equipped with a 10-stud commercial axle, hydraulic drive, hydraulic rear door and a sprung drawbar. SpreadPoint opted for a monocoque chassis which is designed to provide a high strength to weight ratio. The spreader has an unladen weight of 3t.

Since delivery last July, each of the spreaders have spread over 10,000t.
SpreadPoint has cleverly designed its SP spreader range with modularity in mind. Operators have the option to change rear spreading attachments. For instance a customer can opt for the traditional SP-A heavy duty twin-disc system, and at a later stage fit the SX-A 12m folding auger applicator or the SD-A single-disc spreading unit for salting/gritting roads. This was a feature Christopher praised in the SpreadPoint design.

The mobile elevator can load a spreader in under three minutes.
Customers can choose between an RDS control terminal or Isobus control, meaning the spreader is controlled via the tractor’s terminal. Running the spreaders on two full Isobus New Holland ‘Blue Power’ tractors, Christopher opted for the latter option.
To achieve the correct application rate, the spreaders can then be operated in one of three ways. Firstly, using a fixed belt speed and fixed forward speed to maintain the set application rate or secondly, via SensePoint rate control. Once the density of the material is known, belt speed is automatically adjusted to match the tractor’s forward speed.
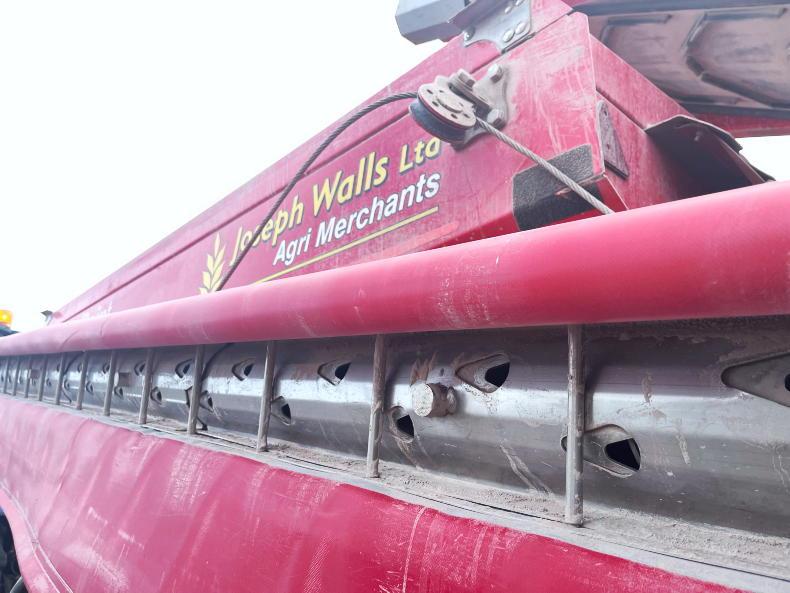
Lime is dropped through the series of holes on the underside of the auger.
Finally, the WeighPoint control option uses load cells to constantly monitor the remaining weight and the quantity spread over a certain time period and continually adjust belt speed according to the set application rate if needs be. Both SensePoint and WeighPoint systems are capable of variable-rate spreading where prescription maps are available.
Both Christopher and spreader operator Ian McDowell complimented the SensePoint system. “The SensePoint system proves accurate once properly calibrated and the load weight is inputted. It’s usually always within 100-150kg of being truly accurate, which can’t be argued with,” Ian stated.
There has been no interest among farmers, especially grassland for variable rate lime applications according to Christopher, a service he believes at the moment doesn’t justify the additional cost in most situations once lime remains cheap relative to chemical fertiliser.

Both boom sections are fitted with a 150mm diameter stainless steel auger, each driven by a hydraulic motor.
Other functions of the control screen include the control of hydraulic boom movements, control of hydraulic motor speeds as well as other features such as the recording of job-specific data – weight, spread etc. Both Christopher and Ian complimented the Isobus control screens and the ease of adjustment, which is done from the driver’s seat.
Auger system
The auger system consists of two separate 6m stainless steel booms, one to the left and one to the right.
Within each is a 150mm diameter stainless steel auger fabricated with 6mm welded flights. Both left and right augers have their own hydraulic motors to provide rotation.
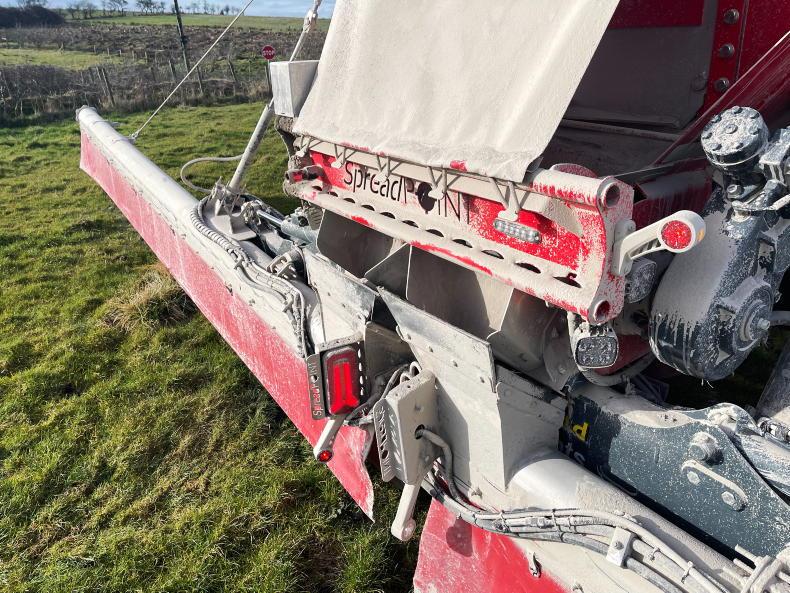
The boom sections fold down and around into working position independantly.
Once the lime falls off the central floor belt it lands in a small receiving hopper at the end of each boom section.

Christopher Walls, Joseph Walls Agri Merchants.
It is then carried by the auger and dropped through the series of outlet holes on the lower side of the auger housing across the 12m total working width. The process is not too dissimilar to a dribble bar system on a slurry tanker. According to SpreadPoint, the choice of full stainless steel is because of lime’s corrosive nature.

Both Christopher's machines are operated via Isobus which is a clean well laid out system he explained.
The adjustable hole arrangement on the auger housing helps tune the spread pattern. SpreadPoint claims this helps reduce the “lining” effect sometimes associated with auger applicators.
Meanwhile, subsequent calibrations of the spread pattern can be done from the cab via the Isobus terminal by adjusting auger speed. From the terminal, operators can see the live application rate alongside the target rate. Application rates up to 5,000kg/ha at speeds of up to 14km/h can be achieved.

Christopher uses two New Holland T7.225 AutoCommand tractors to run the 6m3 spreaders.
One of the few downsides of the auger system is that lime needs to be stone free which, according to Christopher, is hard to guarantee. In the event a stone enters the auger, it then has to be manually reversed from its outer end using a large wrench until the blockage is freed. While each 6m boom can be raised and lowered independently, they cannot spread independently. To help reduce drift, trailing PVC curtains typically run approximately 800mm above the ground.
Rear door position is also displayed on screen via a position sensor mounted on the hydraulic ram. Designed largely for variable-rate applications, the door settings can be adjusted on the move.
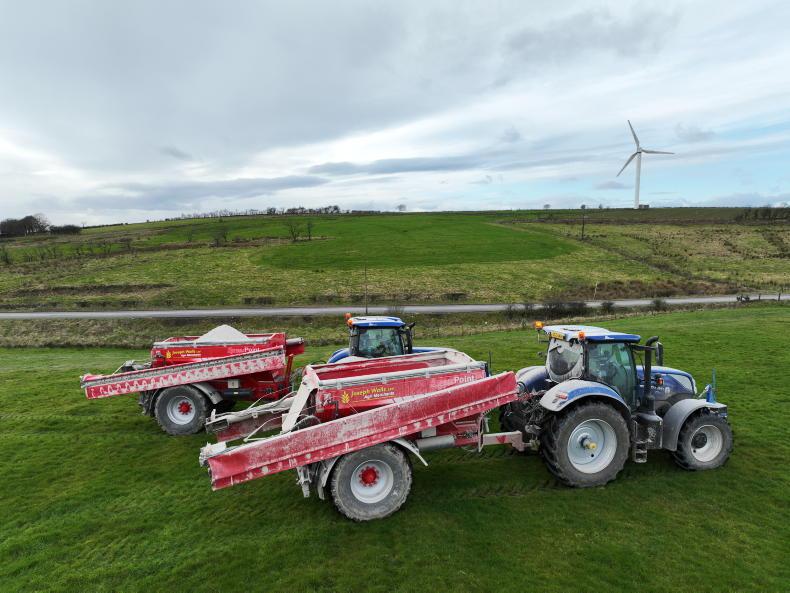
A third identical spreader and mobile elevator is expected to join the fleet in the coming weeks.
However, the system doesn’t suit all situations which Christopher and his team have found out, especially where there are considerable dips and hollows. The booms do not have a break-back feature so operators need to be conscious of undulating terrain. That said, each side can be raised up via tilt rams to avoid surface contact in most situations.
Other features
Aside from an inline hydraulic filter, a pressure gauge is present to show whether or not the auger is blocked.
If blocked, oil is diverted via pressure relief valve. The neat geometry of the booms allow them to fold within 2.7m for transport.

Operators need to be concious of the tail swing from the booms when in transport position.
However, the operator needs to be conscious of boom length especially when leaving gaps, Christopher said. In addition to ball and spoon hitches, Christopher opted for two rear cameras on each machine.
Elevator
While the majority of Irish contractors operate a loading shovel to load spreaders, the Walls don’t.
The benefit of proving the entire service means that they have control over transport and spreading. In order to be more efficient, mobile elevators have always been used. Both spreaders are piped with connections to both tow and power the elevator. Lime is seamlessly unloaded from the truck and into the spreader.

The spreader is equipped with load sensing hydraulics and its own inline hydraulic filter.
Aside from eliminating a loading shovel and an additional operator, Christopher describes the elevators as a cleaner process which provides the ability to load spreaders at the field along the side of a road instead of having to drive miles to a farmyard.
The CV-650 elevator works hand in hand with the spreaders and has the ability to fill each spreader in under three minutes.

The 800mm curtain prevents any drift as the lime is dropped onto the surface.
After spreading 10,000t with each spreader since delivery last July, Christopher and Joseph are more than happy with their performance. “The spreaders have worked a treat. Having come from a pto-driven basic spreader, the difference is night and day. The augers have proved a great job so far combined with the fact everything is controlled and adjusted from the cab. Having come from 7t machines, the additional capacity now sees an artic emptied in three spreader loads, speeding up the job.
“There are a number of benefits to the auger system, the main benefit being dust suppression, especially in residential areas. Given that lime is being vertically dropped, the spread pattern is much more even and accurate.

The 800mm curtain prevents any drift as the lime is dropped onto the surface.
“As expected, a more highly skilled operator is needed to manage the auger system and it is a system that doesn’t suit every field, especially smaller fields with dips and hollows.
“It’s early days yet but I’d expect running costs are going to be higher. Aside from regular greasing, the spreaders have worked maintenance-free so far.

The mobile elevator leaves for quick mess free loading according to Christopher.
“The auger system is going to become more popular without doubt. Already this year there have been farmers requesting the auger system. However, we’ll always keep a standard twin-disc machine for certain jobs. To cope with increasing demand we have another identical spreader and elevator ordered which is expected to arrive now in the coming weeks.
“Overall, the spreaders have been a substantial investment for the business but it’s important we provide the best service possible. Farmers have really seen the importance of lime spreading in recent years, especially with the price of chemical fertiliser.”

The mobile elevator leaves for quick mess free loading according to Christopher.
Model: SP-600 with SX-A 12m folding auger systems.
Spreader capacity: 6m3.
Drive method: hydraulic.
Working width: 12m.
Controls: Isobus.
Rate control: SensePoint Intelligent Control.
Tyres: 650/65 R30.5.
SHARING OPTIONS: