Many farmers have excavators for their own use. Such machines allow farmers to carry out their own work, whether this be land drainage/reclamation, general yard work or for building purposes. In some cases, owning a machine may work out cheaper than hiring in a plant hire contractor.
However, buying a cheap used excavator with the aim of saving a few euros may end up being the most expensive option in the long run. If in the market for a used machine, it is vital to take the time to inspect any potential machine thoroughly. The following guide will give you some pointers on what to watch out for before you commit to buying.
1 Tracks
Starting off with the tracks, potential buyers should be looking out for pointing of the sprockets. If pointed, this will indicate significant wear. The bottom track rollers should be checked over. To inspect, jack up one side of the machine and check each one individually. If these rollers have become loose, they need to be replaced.
It is possible to get away with replacing one at each end of the tracks but in most cases all will have to be replaced. These are sealed self-lubricated units. They will set you back €90 plus VAT each. Special attention should also be paid to components such as track links and idlers in relation to wear.

Check for slack in the track itself which may indicate it needs to be tensioned or could also be a sign of poor maintenance and excessive wear.
Check for slack in the track itself which may indicate it needs to be tensioned or could also be a sign of poor maintenance and excessive wear. If wear is evident in these areas, there’s a good chance the machine will need a full undercarriage, costing in the region of €4,000 plus VAT. This is a huge cost so needs to be checked thoroughly.
2 Slew ring
The slew ring is essentially the machine’s turntable. The excavator’s upper carriage sits on top of the slew ring, enabling it to rotate in both directions. It’s like a big bearing. If not regularly greased, like any component, it will wear over time. The excavator should rotate smoothly without any noise or grinding, which would again indicate that something is not right.
To check for play, start the machine and move the arm up and down. If worn, you will feel the machine rocking. Padraig noted that you will get away with a little bit of wear, but if excessive, it will have to be changed. This is a major job and would cost in the region of €3,000 plus VAT to fit.
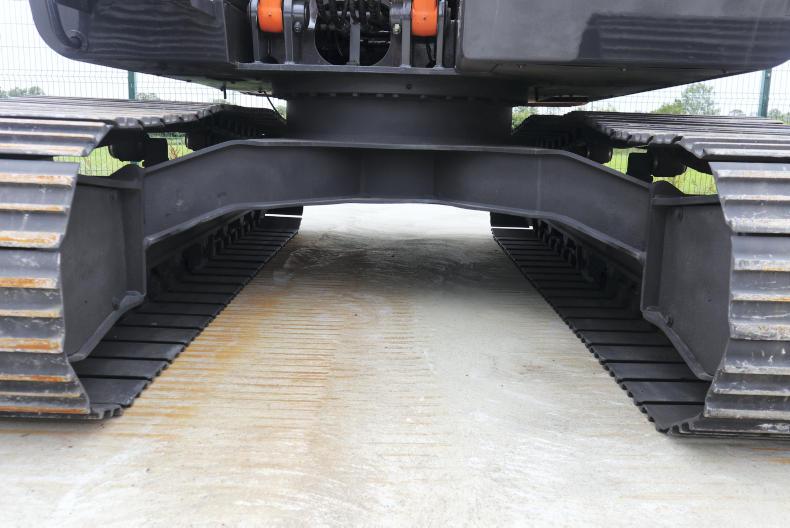
The excavator should rotate smoothly without any noise or grinding, which would again indicate that something is not right.
3 Connection points
Check the main pin which connects the boom arm to the upper carriage and the connection point between the dipper arm and boom. These connection points need to be inspected for excessive wear or movement due to worn pins or bushings. You will get a good feel for the wear in the pins by operating the machine.
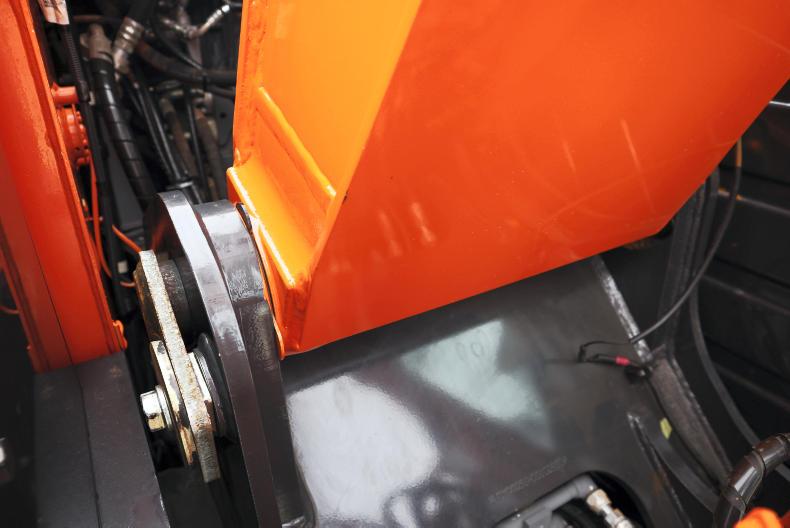
Check all connection points for excessive wear or movement due to worn pins or bushings.
If an excavator wasn’t properly greased and looked after, there will be wear and tear. These points will be loose and will give you a good indication of what the overall condition of the machine may be like. To re-bush the machine would easily cost in the region of €2,000 to €3,000 plus VAT. If the main boom pin is worn, it may need to be line-boarded which will add further cost. Machines with wear will stay working. However, excessive wear will mean less accuracy when digging.
The functionality of the quick hitch should be checked. If significant wear is present, it will need to be replaced. These can’t be reconditioned. Depending on the size and brand fitted, a new hitch will cost in the region of €2,000 plus VAT.
4 Hydraulics
It can be a little difficult to fully check over the health of the hydraulic pump. First off, if the machine is tracking straight and if there’s good power in the tracks, both are a sign of good health. If there’s a bearing gone, the pump will be noisy and noticeably not running smoothly.
There is a gauge positioned to one side of the pump. The oil should be clean. If the oil is dark, the goodness is gone out of it. It is likely burnt, a sign that it wasn’t changed in a long time.
Check the hydraulic pump compartment for signs of leaks. This will give you a better understanding of whether the machine was misused or maintained correctly. A new hydraulic pump is crazy money (in the region of €8,000 plus VAT for a 13t machine). Most people today will recondition the pump. This will cost somewhere in the region of €3,000 to €5,000 plus VAT.

Most people today will recondition the pump. This will cost somewhere in the region of €3,000 to €5,000 plus VAT.
All hydraulic hoses, lines and cylinders should be checked for leaks or potential problems such as cracks or wear. Also, check for leaks in the slew ring or swing bearing, which could give an indication of excessive play or movement.
Any leaks will need to be repaired to ensure the safe and reliable operation of the excavator. Ram seals will cost in the region of €200 plus VAT (supplied and fitted) per ram.
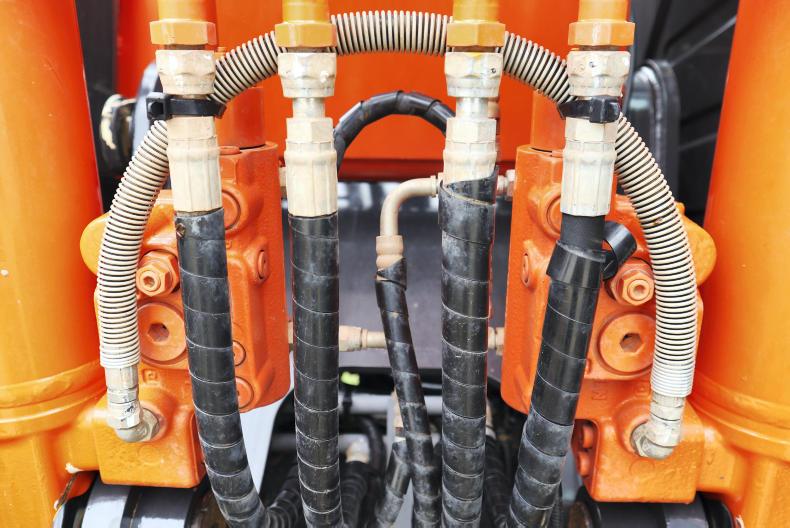
All hydraulic hoses, lines and cylinders should be checked for leaks or potential problems such as cracks or wear.
5 Engine
The machine should be started and left running idle for at least 10 minutes. A sound engine should run smoothly without any unusual noise or excessive smoke. Once warmed up, check for back pressure down the breather pipe. The breather pipe will be located under the rear of the machine. A small amount of blow from the engine is normal, but excessive blow will indicate engine wear, meaning it might be best to stay away from that machine.
Open the engine compartment and check for signs of leaks or excessive black smoke in the form of soot. This will also give a good indication of the engine’s mechanical condition. A stall test where the engine is cut out or stalled at low revs by working the hydraulics will give a good indication if there is a problem with the engine or hydraulic pump. Oil and water levels should also be inspected.
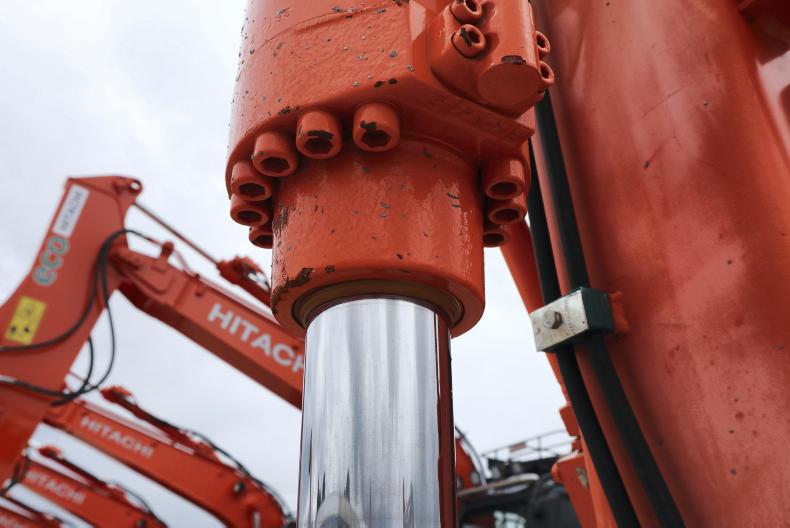
Ram seals will cost in the region of €200 plus VAT (supplied and fitted) per ram.
6 General condition
Like any machine, a general walk around and look at its condition both inside and out will tell you a lot about how well it was cared for by its previous owners.
The exterior should be closely examined for cracks, bends or dents, especially around key connection point welds. The existence of flaws like these could mean that the excavator was subjected to abuse and may require expensive repairs. Welded plates or reinforcing is a telltale sign that there was a problem previously and should be investigated further.
In the cab, all controls and functions should be checked over to see if functional. As Padraig mentioned, a wiper not working isn’t the end of the world but a major function not working should raise a red flag. Keep an eye out for tampered wiring. Some people may fit lights and additional add-ons, which if unprofessionally done can lead to problems down the road. Check over the dashboard for the presence of any warning lights.
If you suspect the odometer isn’t working correctly or has been tampered with, a good rule of thumb is to inspect the cab interior for wear around the pedals and controls, which may give you a better indication of the machine’s true hours.
Many farmers have excavators for their own use. Such machines allow farmers to carry out their own work, whether this be land drainage/reclamation, general yard work or for building purposes. In some cases, owning a machine may work out cheaper than hiring in a plant hire contractor.
However, buying a cheap used excavator with the aim of saving a few euros may end up being the most expensive option in the long run. If in the market for a used machine, it is vital to take the time to inspect any potential machine thoroughly. The following guide will give you some pointers on what to watch out for before you commit to buying.
1 Tracks
Starting off with the tracks, potential buyers should be looking out for pointing of the sprockets. If pointed, this will indicate significant wear. The bottom track rollers should be checked over. To inspect, jack up one side of the machine and check each one individually. If these rollers have become loose, they need to be replaced.
It is possible to get away with replacing one at each end of the tracks but in most cases all will have to be replaced. These are sealed self-lubricated units. They will set you back €90 plus VAT each. Special attention should also be paid to components such as track links and idlers in relation to wear.

Check for slack in the track itself which may indicate it needs to be tensioned or could also be a sign of poor maintenance and excessive wear.
Check for slack in the track itself which may indicate it needs to be tensioned or could also be a sign of poor maintenance and excessive wear. If wear is evident in these areas, there’s a good chance the machine will need a full undercarriage, costing in the region of €4,000 plus VAT. This is a huge cost so needs to be checked thoroughly.
2 Slew ring
The slew ring is essentially the machine’s turntable. The excavator’s upper carriage sits on top of the slew ring, enabling it to rotate in both directions. It’s like a big bearing. If not regularly greased, like any component, it will wear over time. The excavator should rotate smoothly without any noise or grinding, which would again indicate that something is not right.
To check for play, start the machine and move the arm up and down. If worn, you will feel the machine rocking. Padraig noted that you will get away with a little bit of wear, but if excessive, it will have to be changed. This is a major job and would cost in the region of €3,000 plus VAT to fit.
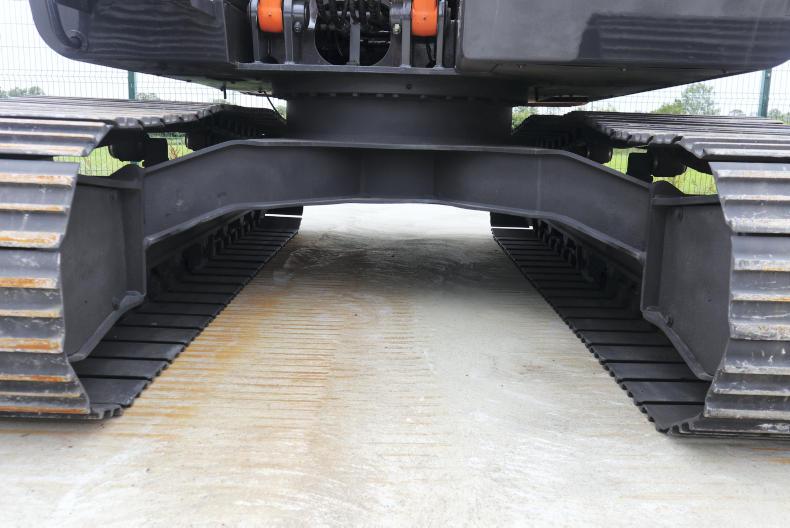
The excavator should rotate smoothly without any noise or grinding, which would again indicate that something is not right.
3 Connection points
Check the main pin which connects the boom arm to the upper carriage and the connection point between the dipper arm and boom. These connection points need to be inspected for excessive wear or movement due to worn pins or bushings. You will get a good feel for the wear in the pins by operating the machine.
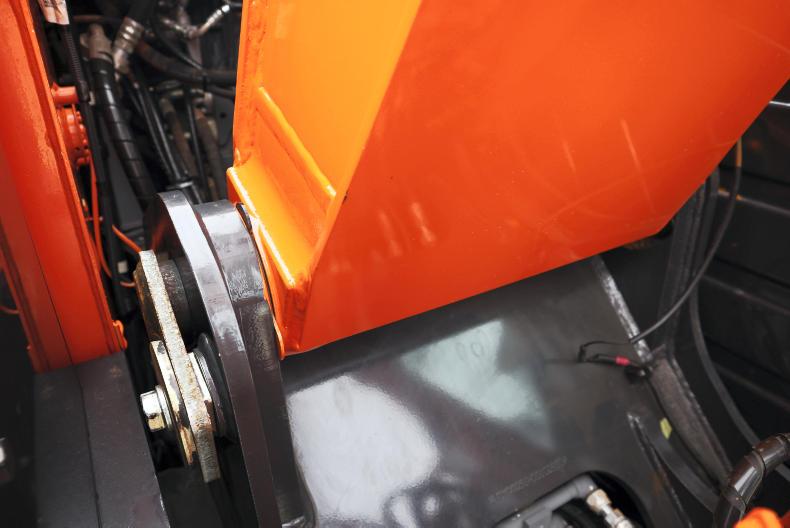
Check all connection points for excessive wear or movement due to worn pins or bushings.
If an excavator wasn’t properly greased and looked after, there will be wear and tear. These points will be loose and will give you a good indication of what the overall condition of the machine may be like. To re-bush the machine would easily cost in the region of €2,000 to €3,000 plus VAT. If the main boom pin is worn, it may need to be line-boarded which will add further cost. Machines with wear will stay working. However, excessive wear will mean less accuracy when digging.
The functionality of the quick hitch should be checked. If significant wear is present, it will need to be replaced. These can’t be reconditioned. Depending on the size and brand fitted, a new hitch will cost in the region of €2,000 plus VAT.
4 Hydraulics
It can be a little difficult to fully check over the health of the hydraulic pump. First off, if the machine is tracking straight and if there’s good power in the tracks, both are a sign of good health. If there’s a bearing gone, the pump will be noisy and noticeably not running smoothly.
There is a gauge positioned to one side of the pump. The oil should be clean. If the oil is dark, the goodness is gone out of it. It is likely burnt, a sign that it wasn’t changed in a long time.
Check the hydraulic pump compartment for signs of leaks. This will give you a better understanding of whether the machine was misused or maintained correctly. A new hydraulic pump is crazy money (in the region of €8,000 plus VAT for a 13t machine). Most people today will recondition the pump. This will cost somewhere in the region of €3,000 to €5,000 plus VAT.

Most people today will recondition the pump. This will cost somewhere in the region of €3,000 to €5,000 plus VAT.
All hydraulic hoses, lines and cylinders should be checked for leaks or potential problems such as cracks or wear. Also, check for leaks in the slew ring or swing bearing, which could give an indication of excessive play or movement.
Any leaks will need to be repaired to ensure the safe and reliable operation of the excavator. Ram seals will cost in the region of €200 plus VAT (supplied and fitted) per ram.
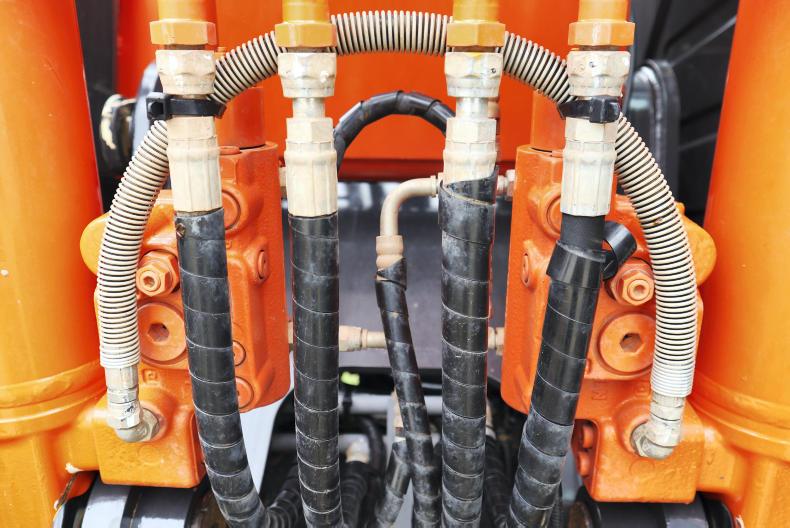
All hydraulic hoses, lines and cylinders should be checked for leaks or potential problems such as cracks or wear.
5 Engine
The machine should be started and left running idle for at least 10 minutes. A sound engine should run smoothly without any unusual noise or excessive smoke. Once warmed up, check for back pressure down the breather pipe. The breather pipe will be located under the rear of the machine. A small amount of blow from the engine is normal, but excessive blow will indicate engine wear, meaning it might be best to stay away from that machine.
Open the engine compartment and check for signs of leaks or excessive black smoke in the form of soot. This will also give a good indication of the engine’s mechanical condition. A stall test where the engine is cut out or stalled at low revs by working the hydraulics will give a good indication if there is a problem with the engine or hydraulic pump. Oil and water levels should also be inspected.
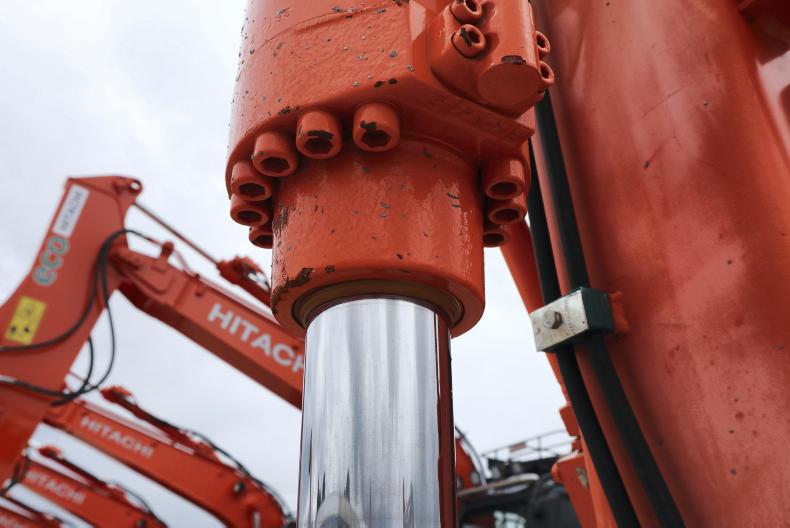
Ram seals will cost in the region of €200 plus VAT (supplied and fitted) per ram.
6 General condition
Like any machine, a general walk around and look at its condition both inside and out will tell you a lot about how well it was cared for by its previous owners.
The exterior should be closely examined for cracks, bends or dents, especially around key connection point welds. The existence of flaws like these could mean that the excavator was subjected to abuse and may require expensive repairs. Welded plates or reinforcing is a telltale sign that there was a problem previously and should be investigated further.
In the cab, all controls and functions should be checked over to see if functional. As Padraig mentioned, a wiper not working isn’t the end of the world but a major function not working should raise a red flag. Keep an eye out for tampered wiring. Some people may fit lights and additional add-ons, which if unprofessionally done can lead to problems down the road. Check over the dashboard for the presence of any warning lights.
If you suspect the odometer isn’t working correctly or has been tampered with, a good rule of thumb is to inspect the cab interior for wear around the pedals and controls, which may give you a better indication of the machine’s true hours.
SHARING OPTIONS: