An open day organised by Easyfix was held on Michael and Catherine Gowing’s dairy farm in Scorduff, Brosna, Birr, Co Offaly. Originally from Co Laois, Michael bought the then 290ac farm in 2006.
Interestingly, Michael and his wife Catherine are both former Macra na Feirme presidents.
Since the initial purchase, they have grown the farm further by buying and leasing more adjoining land and increasing the herd size by 50%.
Today, there are 350 cows being milked and the farm is particularly busy in the springtime because 90% calve in the first six weeks.
With growing numbers, the Gowings and their staff have taken steps to make work more efficient and streamlined.
In this article, we feature some of the infrastructural and equipment changes they have made to achieve greater levels of efficiency and safety on the demanding farm.
Rubber mats in the parlour
The installation Michael is most proud of was the fitting of rubber mats on the floor of the parlour where cows walk.
“Over time, any grip that was in the concrete floor had worn away and it could become very slippy in wet weather,” explained Michael.
He said the chance of a cow slipping and hurting herself was getting too high for their liking, so something had to be done.
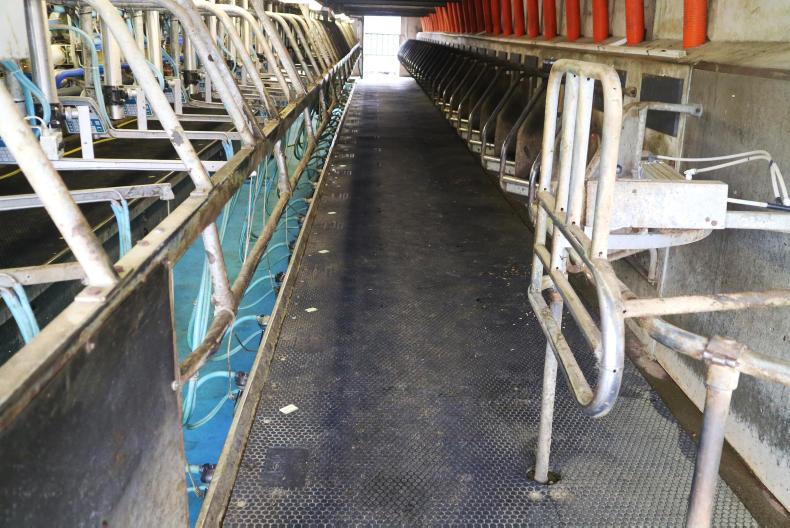
He got rubber mats fitted with a grip finish and is very pleased with the results. “I am not a man to recommend something until I have tried it, but after just one milking I called my father and told him to fit the mats,” said Michael.
He said cows flow into and out of the parlour much quicker now and are confident in their stance and less fidgety with the mats. Michael also put down special mats in the pit, which he says was a welcome addition in the 28-unit parlour.
The rubber cow mats cost approximately €3,000, excluding VAT.
Slurry pump and rain gun
The Gowings have a large 340,000-gallon round slurry store on the farm, which holds the majority of slurry produced.
Michael said this slurry store was extremely difficult to agitate in the past because a hard crust used to develop on the top.

“There was a propeller agitator fitted at the bottom of the tank but it was taking far too long to agitate the slurry and it couldn’t really get rid of the crust,” he explained.
Michael said the propeller could be left turned on for a number of hours with little or no effect. He decided to buy a reconditioned high-pressure umbilical slurry pump, which cost approximately €4,000 in 2015.

The slurry pump can be connected to a rain gun which is fitted to the top of the outdoor slurry lagoon. “It only takes half an hour to agitate the slurry and break up any crust; it’s great,” said Michael.
The slurry pump can also be used to move slurry from the nearby underground tank to the store and is faster doing this job than the agitator. “Sometimes we use it as a booster when our contractor comes spreading slurry with the umbilical system too,” he explained.
Herringbone/batch crush
Four years ago, the family decided to install a herringbone crush. They already had a good-quality cattle race on the farm but Michael said it was not suitable for every job.
“It was taking too long to scan cows, test cows or give vaccinations,” he explained. The herringbone crush was designed to fit 28 cows (one row of the parlour).
In this type of crush, cows stand side by side and are in the correct position for insemination, vaccinations and TB testing.
“The first time I used it, I thought it was the biggest waste of money ever, but we soon realised that it would just take time for both us and the cows to get used to it,” explained Michael.

Since then, it has made bigger cow-handling jobs much more efficient. He said that the herringbone crush is more suitable for in-calf cows and they can now scan 350 cows in three hours.
They also use this crush for artificially inseminating cows at the start of the breeding season, when there are a lot of cows to be inseminated on a daily basis.
However, when there are less than 10 cows to be done, they revert back to the cattle race. “We find it easier to artificially inseminate a small number of cows in the old race,” explained Michael.
Rainwater harvesting
The water supply on the farm was not reliable so they decided to build a 20,000-gallon rainwater harvesting tank as a reserve.
This tank was poured when they were building the new cubicle shed. There are three wells on the farm and they are all fed into this tank.
There is also a county council connection, which feeds into this tank and is only used as a last resort. A series of ball cocks are fitted in the tank to control the supply of water from the different sources.
“In the winter, 75% of the water on the farm is harvested from the roof of the nine-bay cubicle shed,” said Michael.

He added that this reduces the amount of times the pumps in the well have to come on annually.
However, Michael admits that when demand for water is at its peak, supply is usually at its lowest because rainfall is low but the tank gives peace of mind that a reserve is available.
Water is used first from the rain water supply followed by the well supply and this is followed by the county council supply.
He said the county council water was only required once when a pump from the main well broke down. In the event of a power outage and all pumps stop working Michael can switch the mains system to supply the water troughs directly.
Bull pens
This year, the Gowings upgraded their bull-handling facilities. They were using an old slatted shed that was on the farm for housing bulls but it needed upgrading.
Six or seven bulls are wintered on the farm every year and they can become boisterous during that period.
“Safety for man and beast was the reason we went to such expense with this shed,” said Michael.

They changed all the gates and barriers and replaced these with heavy gauge steel gates.
The heights of the barriers and gates were increased and all the concrete single slats were replaced with gang slats and rubber mats were installed in some pens.
“It might seem a little excessive but I would rather it that way,” he explained.
Calf shed
The calf shed is an interesting design. It was once used as a slatted shed for yearlings but as cow numbers increased the shed had to be converted to accommodate calves.
Sliding doors were added to the front, so that calves would not be subjected to draughts.

Michael said that the shed is still airy because there is a gap between the eaves and the back wall to allow air enter the building and warm air will flow out the front of the shed over the doors.
The sliding doors also shelter the people feeding the calves at the front of the building from the elements. Inside, each pen is 12ft x 15ft and is slatted.
A round bale of straw is rolled out on top of the slats as bedding for the calves.

With the slats, bedding keeps drier for longer and it can be easily cleaned out using a tractor loader at the front.
The calves are usually housed in this shed in groups of 30 from 10 days old.
When they get stronger, they are put out into small, sheltered paddocks beside the yard.
Milk tank
Feeding calves is a big job on the farm in spring. To make it more efficient, the Gowings bought an old 700l tank with an axle.
A small dairy farmer owned this tank originally and used it to transport milk down a lane for collection.
They fitted a used diesel pump, hose and nozzle to this tank despite being told the pump would seize up after a few months use.
“People said without the lubrication of the diesel it would stop working but after two years it is still going strong,” explained Michael.

He said it only cost €110 at the time to buy the secondhand pump compared with €480 if he was to buy a proper milk pump.
“The tank makes feeding so much quicker and it is insulated which keeps the milk warm and this helps to train young calves to suck,” said Michael.
Watch: Donegal farmer reclaims moorland for grazing
Watch: underpass takes the stress out of milking/a>
An open day organised by Easyfix was held on Michael and Catherine Gowing’s dairy farm in Scorduff, Brosna, Birr, Co Offaly. Originally from Co Laois, Michael bought the then 290ac farm in 2006.
Interestingly, Michael and his wife Catherine are both former Macra na Feirme presidents.
Since the initial purchase, they have grown the farm further by buying and leasing more adjoining land and increasing the herd size by 50%.
Today, there are 350 cows being milked and the farm is particularly busy in the springtime because 90% calve in the first six weeks.
With growing numbers, the Gowings and their staff have taken steps to make work more efficient and streamlined.
In this article, we feature some of the infrastructural and equipment changes they have made to achieve greater levels of efficiency and safety on the demanding farm.
Rubber mats in the parlour
The installation Michael is most proud of was the fitting of rubber mats on the floor of the parlour where cows walk.
“Over time, any grip that was in the concrete floor had worn away and it could become very slippy in wet weather,” explained Michael.
He said the chance of a cow slipping and hurting herself was getting too high for their liking, so something had to be done.
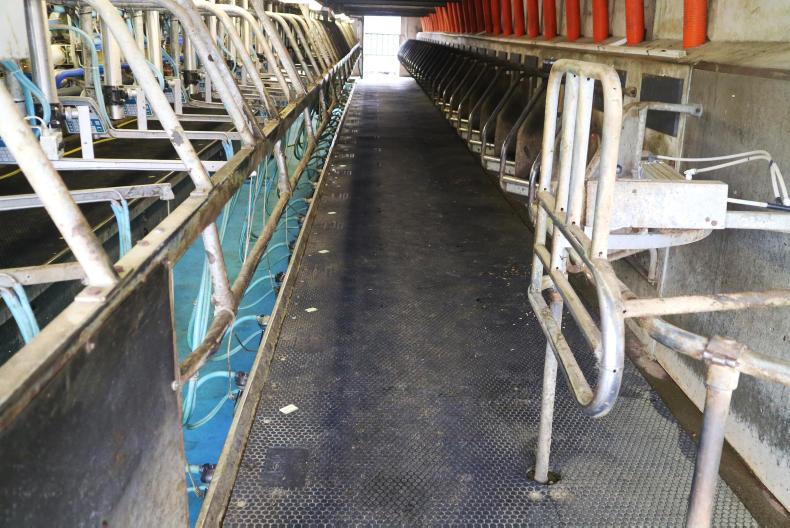
He got rubber mats fitted with a grip finish and is very pleased with the results. “I am not a man to recommend something until I have tried it, but after just one milking I called my father and told him to fit the mats,” said Michael.
He said cows flow into and out of the parlour much quicker now and are confident in their stance and less fidgety with the mats. Michael also put down special mats in the pit, which he says was a welcome addition in the 28-unit parlour.
The rubber cow mats cost approximately €3,000, excluding VAT.
Slurry pump and rain gun
The Gowings have a large 340,000-gallon round slurry store on the farm, which holds the majority of slurry produced.
Michael said this slurry store was extremely difficult to agitate in the past because a hard crust used to develop on the top.

“There was a propeller agitator fitted at the bottom of the tank but it was taking far too long to agitate the slurry and it couldn’t really get rid of the crust,” he explained.
Michael said the propeller could be left turned on for a number of hours with little or no effect. He decided to buy a reconditioned high-pressure umbilical slurry pump, which cost approximately €4,000 in 2015.

The slurry pump can be connected to a rain gun which is fitted to the top of the outdoor slurry lagoon. “It only takes half an hour to agitate the slurry and break up any crust; it’s great,” said Michael.
The slurry pump can also be used to move slurry from the nearby underground tank to the store and is faster doing this job than the agitator. “Sometimes we use it as a booster when our contractor comes spreading slurry with the umbilical system too,” he explained.
Herringbone/batch crush
Four years ago, the family decided to install a herringbone crush. They already had a good-quality cattle race on the farm but Michael said it was not suitable for every job.
“It was taking too long to scan cows, test cows or give vaccinations,” he explained. The herringbone crush was designed to fit 28 cows (one row of the parlour).
In this type of crush, cows stand side by side and are in the correct position for insemination, vaccinations and TB testing.
“The first time I used it, I thought it was the biggest waste of money ever, but we soon realised that it would just take time for both us and the cows to get used to it,” explained Michael.

Since then, it has made bigger cow-handling jobs much more efficient. He said that the herringbone crush is more suitable for in-calf cows and they can now scan 350 cows in three hours.
They also use this crush for artificially inseminating cows at the start of the breeding season, when there are a lot of cows to be inseminated on a daily basis.
However, when there are less than 10 cows to be done, they revert back to the cattle race. “We find it easier to artificially inseminate a small number of cows in the old race,” explained Michael.
Rainwater harvesting
The water supply on the farm was not reliable so they decided to build a 20,000-gallon rainwater harvesting tank as a reserve.
This tank was poured when they were building the new cubicle shed. There are three wells on the farm and they are all fed into this tank.
There is also a county council connection, which feeds into this tank and is only used as a last resort. A series of ball cocks are fitted in the tank to control the supply of water from the different sources.
“In the winter, 75% of the water on the farm is harvested from the roof of the nine-bay cubicle shed,” said Michael.

He added that this reduces the amount of times the pumps in the well have to come on annually.
However, Michael admits that when demand for water is at its peak, supply is usually at its lowest because rainfall is low but the tank gives peace of mind that a reserve is available.
Water is used first from the rain water supply followed by the well supply and this is followed by the county council supply.
He said the county council water was only required once when a pump from the main well broke down. In the event of a power outage and all pumps stop working Michael can switch the mains system to supply the water troughs directly.
Bull pens
This year, the Gowings upgraded their bull-handling facilities. They were using an old slatted shed that was on the farm for housing bulls but it needed upgrading.
Six or seven bulls are wintered on the farm every year and they can become boisterous during that period.
“Safety for man and beast was the reason we went to such expense with this shed,” said Michael.

They changed all the gates and barriers and replaced these with heavy gauge steel gates.
The heights of the barriers and gates were increased and all the concrete single slats were replaced with gang slats and rubber mats were installed in some pens.
“It might seem a little excessive but I would rather it that way,” he explained.
Calf shed
The calf shed is an interesting design. It was once used as a slatted shed for yearlings but as cow numbers increased the shed had to be converted to accommodate calves.
Sliding doors were added to the front, so that calves would not be subjected to draughts.

Michael said that the shed is still airy because there is a gap between the eaves and the back wall to allow air enter the building and warm air will flow out the front of the shed over the doors.
The sliding doors also shelter the people feeding the calves at the front of the building from the elements. Inside, each pen is 12ft x 15ft and is slatted.
A round bale of straw is rolled out on top of the slats as bedding for the calves.

With the slats, bedding keeps drier for longer and it can be easily cleaned out using a tractor loader at the front.
The calves are usually housed in this shed in groups of 30 from 10 days old.
When they get stronger, they are put out into small, sheltered paddocks beside the yard.
Milk tank
Feeding calves is a big job on the farm in spring. To make it more efficient, the Gowings bought an old 700l tank with an axle.
A small dairy farmer owned this tank originally and used it to transport milk down a lane for collection.
They fitted a used diesel pump, hose and nozzle to this tank despite being told the pump would seize up after a few months use.
“People said without the lubrication of the diesel it would stop working but after two years it is still going strong,” explained Michael.

He said it only cost €110 at the time to buy the secondhand pump compared with €480 if he was to buy a proper milk pump.
“The tank makes feeding so much quicker and it is insulated which keeps the milk warm and this helps to train young calves to suck,” said Michael.
Watch: Donegal farmer reclaims moorland for grazing
Watch: underpass takes the stress out of milking/a>
SHARING OPTIONS: