The Drayne family has been milking cows outside Lisburn since the 1930s, and has been selling milk and cream directly to consumers since 1942.
Explaining the history of the farm during an autumn dairy meeting organised by the Ulster Grassland Society (UGS) on Tuesday, Michael Drayne said that when he joined the business in 1970, it was mainly concentrating on doorstep deliveries in the Lisburn area.
However, the advent of supermarkets brought a gradual demise in this route to market, forcing the family to look at alternative outlets, such as restaurants, coffee shops and local retailers. Most of its customer base is in the Lisburn and Belfast areas.
Selling liquid milk remains a highly competitive market and “you won’t get fat on the profit”, suggested Michael.
Approximately eight years ago, the business saw an opportunity to diversify into the production of ice-cream. It now has 13 different flavours on offer, with sales throughout NI and into the Republic of Ireland.
While there are also plenty of competitors in the ice-cream market, it has the potential to be “a bit more profitable”, Michael told UGS members.
In total, the Draynes produce and process 1.3m litres of their own milk and buy in a further 6m litres for processing from Lakeland Dairies – Michael Drayne has had a long-standing relationship with the Lakeland Dairies owned Ballyrashane Creamery.
The ice-cream plant on the farm pasteurises 300l per hour, with a recent upgrade made to a 700l-per-hour continuous freezer, allowing more ice-cream to be produced daily. The focus is on producing a high quality premium product for restaurants, hotels and small shops.
The milk plant runs at 5,000l per hour, producing full-fat, semi-skimmed and skimmed milk, as well as whipping and double cream. A planned investment in the New Year will see throughput doubling from 5,000l to 10,000l.
“The bigger plant will take half the time. It is about improving efficiency. We are not necessarily looking to double the volume,” explained Michael.
He said that downturns in dairy commodities have in the past stimulated a “race to the bottom” among processing businesses trying to win new market share. However, his customers need a long notice period of any changes in price, which means that when the market turns, it can still take him four months to get the price up again.
“For us, to run the price down would be foolish,” said Michael.
Across the processing plant, there are nine full-time employees, with a further 18 employed in product distribution and seven in sales, administration and management.
A focus into the future is to improve the environmental sustainability of the business, with plans to get to net zero greenhouse gas emissions by 2040. In recent years, investment has been made in solar panels, and during the last summer, around 40% of energy needs came from this technology.
Cows milked though Lely robots
There are 120 Holstein cows on the Drayne farm, milked through three Lely A4 robots.
According to Chris Wright, who manages the dairy herd on the farm, the plan is to get the herd to 170 cows to maximise the potential of the three robots.
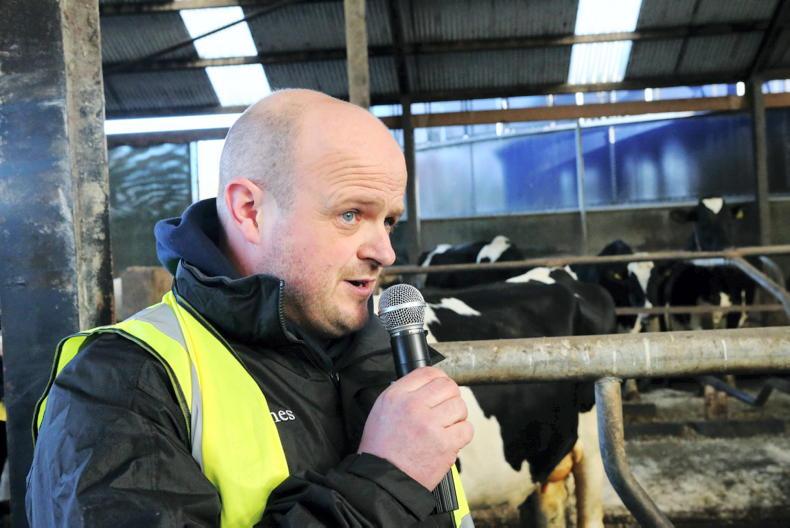
Chris Wright, farm manager at the Draynes Farm.
He said there is currently between 12% and 17% free-time at the robots, while this figure should be around 10%. The farm also had some issues with slow-milking speed in 13 to 14 cows. A check through breeding records shows that these cows are all related to three original animals – no more replacements from these bloodlines will be kept.
First, calving heifers are allocated to Robot A, with mature cows going through Robot B. Once cows are settled in-calf and around 200 days-in-milk, they go to Robot C.
This third group is allowed free access to grass during the day in spring and summer months.
First, calving heifers are allocated to Robot A, with mature cows going through Robot B
How much time the group actually spends outside can be dependent on the weather and grass quality, while farm traffic during silage-making and slurry spreading can also disrupt the flow of cows in and out of the robot.
However, Chris was clear that when customers come to visit the farm, they want (and expect) to see cows out grazing.
Difficult summer for silage-making
Broken weather meant first-cut silage in 2022 was not harvested until 24 May, but the cows “did not like it”, so the aim was to harvest earlier in 2023, said Chris Wright.
In total, 231 acres of first cut was mowed on 2 May 2023, but a short window to get it ensiled resulted in the silage not being as dry as was hoped (see Table 1).
The first cut was treated with an inoculant and has the potential to support maintenance plus 8l of milk, which is below the target of 10l. Slippage in the pit has also occurred, which has meant a significant amount has been wasted.
Normally, three cuts are taken, although a fourth cut was ensiled this year. Chris is considering moving towards a multi-cut system to try to improve overall D-value, leading to higher yields and improved milk components.
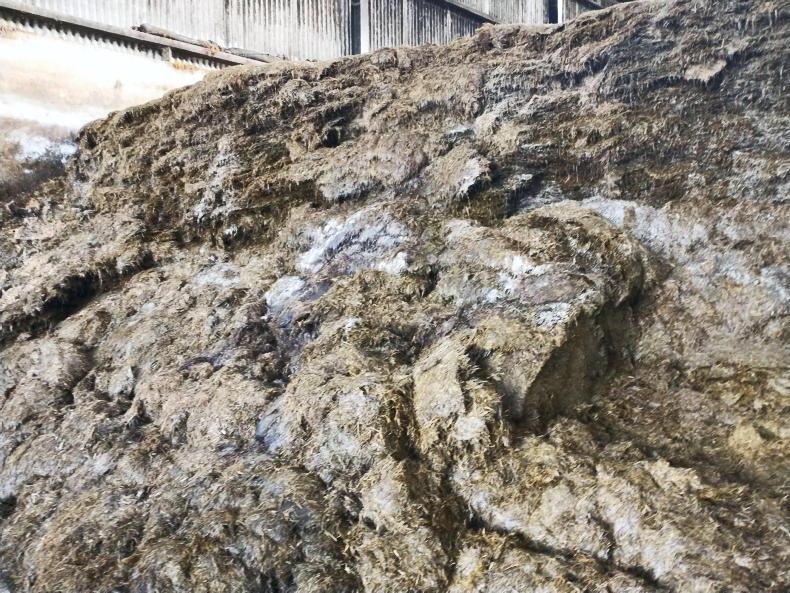
Slippage occurred in the middle of the first cut silage pit and has resulted in significant losses.
Wholecrop rye is included in the diet of both lactating and dry cows, with the herd currently being offered a spring-planted crop. However, it got off to a difficult start due to dry weather in June and “lacks any power”, said Chris. Analysis shows it has a D-value of 62.5, an ME of 9.7MJ and a starch content of only 5.8%.
An autumn-planted crop is in the bottom of the pit and should be higher quality – it will be included in the diet within the next couple of weeks.
Milking and dry cow diets this winter
Fresh calved cows and heifers on the Drayne farm are fed a base diet to support maintenance plus 25l, explained Mary-Jane Robinson from Thompsons.
As well as 32kg of first-cut silage, the TMR includes 8kg of wholecrop rye, 0.5kg of straw, 6.5kg of a blend, 2.5kg of soya hulls and 0.2kg of megalac. Cows are then fed-to-yield in the robot with an 18% compound nut.
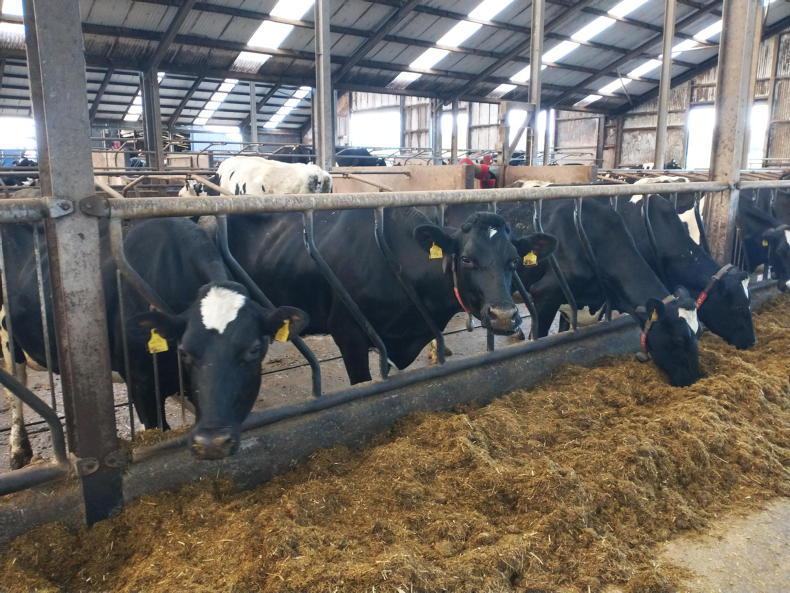
The cows on the Draynes Farm are all Holstein-bred.
The diet for stale cows going through Robot C is designed to support maintenance, plus 18l, with 38kg of first cut offered along with 5kg of wholecrop rye, 0.5kg of straw, 2.5kg of soya hulls and 2kg of blend.
The cows in this group were recently moved over to a Lely concentrate optimiser programme. It effectively manages the amount of concentrate fed in the robot, utilising software thattakes into account current milk price and feed costs, as well as individual milk yield.
The aim is to reduce concentrate fed and maximise the milk produced from forage, said Mary-Jane.
Overall, average milk yield on the farm currently sits at 33l, with cows an average of 157 days in milk and visiting the robots an average of 3.1 times per day. Rolling herd feed rate is at 0.39kg/l.
Dry cows
Dry cows are run as one group with the diet based on grass silage and wholecrop rye, with 2kg of wheat straw offered along with 2kg of pre-calver concentrate.
Year-round calving for consistent yield
To optimise the robots and also ensure a consistent supply of milk for processing, the herd on the farm is year-round calving.
The aim is to bring in first calvers at 24 months, with sexed semen used on these heifers and the first two cycles of top-performing cows.
Those that don’t hold to sexed semen or are not deemed suitable for breeding replacements are inseminated with triple beef semen.
All beef calves are sold off the farm. Calving interval currently averages 393 days.
While all milking cows are Holstein-bred, 40 straws of Viking Red semen was used last year and there are 15 crossbred heifer calves on the ground.
112ha farmed.120 Holstein cows.Three Lely robots.Butterfat: 4.2%.Protein: 3.38%.SCC: 140. Read more
Delivering top beef margins in Co Down
Soil sampling under way in Zone 2
The Drayne family has been milking cows outside Lisburn since the 1930s, and has been selling milk and cream directly to consumers since 1942.
Explaining the history of the farm during an autumn dairy meeting organised by the Ulster Grassland Society (UGS) on Tuesday, Michael Drayne said that when he joined the business in 1970, it was mainly concentrating on doorstep deliveries in the Lisburn area.
However, the advent of supermarkets brought a gradual demise in this route to market, forcing the family to look at alternative outlets, such as restaurants, coffee shops and local retailers. Most of its customer base is in the Lisburn and Belfast areas.
Selling liquid milk remains a highly competitive market and “you won’t get fat on the profit”, suggested Michael.
Approximately eight years ago, the business saw an opportunity to diversify into the production of ice-cream. It now has 13 different flavours on offer, with sales throughout NI and into the Republic of Ireland.
While there are also plenty of competitors in the ice-cream market, it has the potential to be “a bit more profitable”, Michael told UGS members.
In total, the Draynes produce and process 1.3m litres of their own milk and buy in a further 6m litres for processing from Lakeland Dairies – Michael Drayne has had a long-standing relationship with the Lakeland Dairies owned Ballyrashane Creamery.
The ice-cream plant on the farm pasteurises 300l per hour, with a recent upgrade made to a 700l-per-hour continuous freezer, allowing more ice-cream to be produced daily. The focus is on producing a high quality premium product for restaurants, hotels and small shops.
The milk plant runs at 5,000l per hour, producing full-fat, semi-skimmed and skimmed milk, as well as whipping and double cream. A planned investment in the New Year will see throughput doubling from 5,000l to 10,000l.
“The bigger plant will take half the time. It is about improving efficiency. We are not necessarily looking to double the volume,” explained Michael.
He said that downturns in dairy commodities have in the past stimulated a “race to the bottom” among processing businesses trying to win new market share. However, his customers need a long notice period of any changes in price, which means that when the market turns, it can still take him four months to get the price up again.
“For us, to run the price down would be foolish,” said Michael.
Across the processing plant, there are nine full-time employees, with a further 18 employed in product distribution and seven in sales, administration and management.
A focus into the future is to improve the environmental sustainability of the business, with plans to get to net zero greenhouse gas emissions by 2040. In recent years, investment has been made in solar panels, and during the last summer, around 40% of energy needs came from this technology.
Cows milked though Lely robots
There are 120 Holstein cows on the Drayne farm, milked through three Lely A4 robots.
According to Chris Wright, who manages the dairy herd on the farm, the plan is to get the herd to 170 cows to maximise the potential of the three robots.
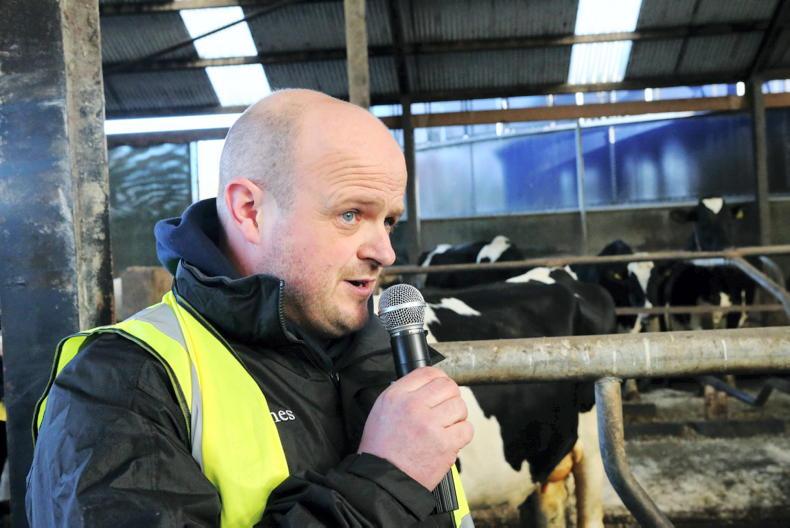
Chris Wright, farm manager at the Draynes Farm.
He said there is currently between 12% and 17% free-time at the robots, while this figure should be around 10%. The farm also had some issues with slow-milking speed in 13 to 14 cows. A check through breeding records shows that these cows are all related to three original animals – no more replacements from these bloodlines will be kept.
First, calving heifers are allocated to Robot A, with mature cows going through Robot B. Once cows are settled in-calf and around 200 days-in-milk, they go to Robot C.
This third group is allowed free access to grass during the day in spring and summer months.
First, calving heifers are allocated to Robot A, with mature cows going through Robot B
How much time the group actually spends outside can be dependent on the weather and grass quality, while farm traffic during silage-making and slurry spreading can also disrupt the flow of cows in and out of the robot.
However, Chris was clear that when customers come to visit the farm, they want (and expect) to see cows out grazing.
Difficult summer for silage-making
Broken weather meant first-cut silage in 2022 was not harvested until 24 May, but the cows “did not like it”, so the aim was to harvest earlier in 2023, said Chris Wright.
In total, 231 acres of first cut was mowed on 2 May 2023, but a short window to get it ensiled resulted in the silage not being as dry as was hoped (see Table 1).
The first cut was treated with an inoculant and has the potential to support maintenance plus 8l of milk, which is below the target of 10l. Slippage in the pit has also occurred, which has meant a significant amount has been wasted.
Normally, three cuts are taken, although a fourth cut was ensiled this year. Chris is considering moving towards a multi-cut system to try to improve overall D-value, leading to higher yields and improved milk components.
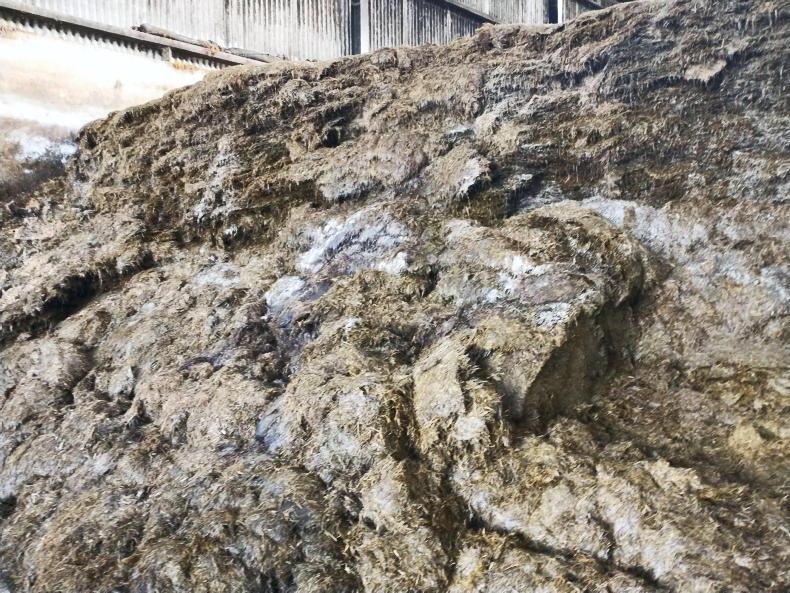
Slippage occurred in the middle of the first cut silage pit and has resulted in significant losses.
Wholecrop rye is included in the diet of both lactating and dry cows, with the herd currently being offered a spring-planted crop. However, it got off to a difficult start due to dry weather in June and “lacks any power”, said Chris. Analysis shows it has a D-value of 62.5, an ME of 9.7MJ and a starch content of only 5.8%.
An autumn-planted crop is in the bottom of the pit and should be higher quality – it will be included in the diet within the next couple of weeks.
Milking and dry cow diets this winter
Fresh calved cows and heifers on the Drayne farm are fed a base diet to support maintenance plus 25l, explained Mary-Jane Robinson from Thompsons.
As well as 32kg of first-cut silage, the TMR includes 8kg of wholecrop rye, 0.5kg of straw, 6.5kg of a blend, 2.5kg of soya hulls and 0.2kg of megalac. Cows are then fed-to-yield in the robot with an 18% compound nut.
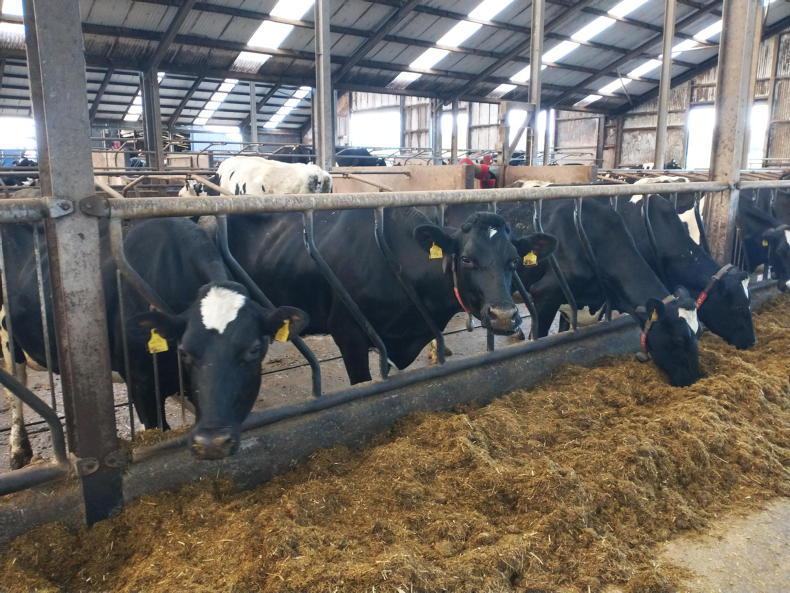
The cows on the Draynes Farm are all Holstein-bred.
The diet for stale cows going through Robot C is designed to support maintenance, plus 18l, with 38kg of first cut offered along with 5kg of wholecrop rye, 0.5kg of straw, 2.5kg of soya hulls and 2kg of blend.
The cows in this group were recently moved over to a Lely concentrate optimiser programme. It effectively manages the amount of concentrate fed in the robot, utilising software thattakes into account current milk price and feed costs, as well as individual milk yield.
The aim is to reduce concentrate fed and maximise the milk produced from forage, said Mary-Jane.
Overall, average milk yield on the farm currently sits at 33l, with cows an average of 157 days in milk and visiting the robots an average of 3.1 times per day. Rolling herd feed rate is at 0.39kg/l.
Dry cows
Dry cows are run as one group with the diet based on grass silage and wholecrop rye, with 2kg of wheat straw offered along with 2kg of pre-calver concentrate.
Year-round calving for consistent yield
To optimise the robots and also ensure a consistent supply of milk for processing, the herd on the farm is year-round calving.
The aim is to bring in first calvers at 24 months, with sexed semen used on these heifers and the first two cycles of top-performing cows.
Those that don’t hold to sexed semen or are not deemed suitable for breeding replacements are inseminated with triple beef semen.
All beef calves are sold off the farm. Calving interval currently averages 393 days.
While all milking cows are Holstein-bred, 40 straws of Viking Red semen was used last year and there are 15 crossbred heifer calves on the ground.
112ha farmed.120 Holstein cows.Three Lely robots.Butterfat: 4.2%.Protein: 3.38%.SCC: 140. Read more
Delivering top beef margins in Co Down
Soil sampling under way in Zone 2
SHARING OPTIONS: