Andrew Purcell and Alf McGlew are neighbouring dairy farmers and, in 2007, they entered a collaborative farming partnership.
This year, they completed the jump from their 25-unit herringbone parlour into a new DeLaval 50-bail rotary parlour which they have been milking in since 23 November.
Over the last 14 years of working together, they have taken on more ground and increased cow numbers.
Now stocked at 3.3LU/ha, they are milking 370 cows on the home platform. During this time, they took on a second milking platform and are now milking 80 cows there. In 2021, a total of 450 cows were milked between both platforms.
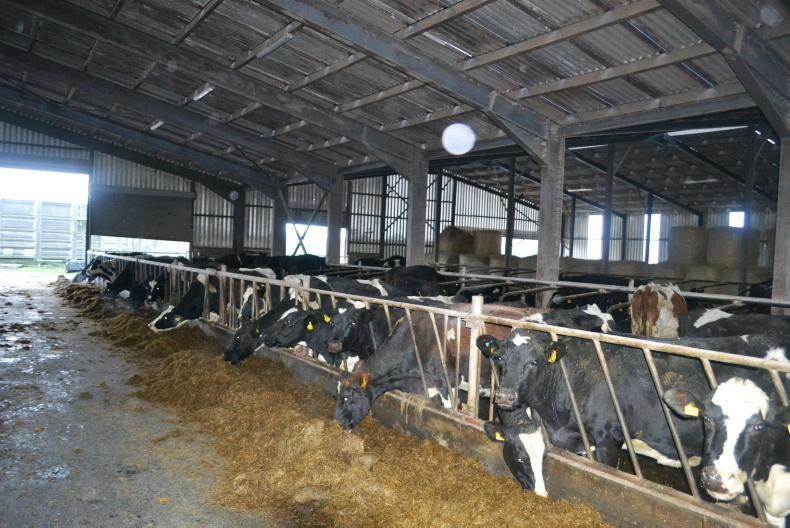
All 450 cows are wintered and calved on the home farm and at the beginning of March each year, 80 cows are moved to the second block.
Silage comes from support blocks that are not on the main platform and the replacement heifers are reared on this ground too.
Cow numbers grew from 140 to 240 between 2007 and 2015. Cow type has also changed since the beginning of the partnership.
In 2008, they crossed the herd with Jersey and some Norwegian red. They are now milking a predominantly Jersey cross herd of cows.

The work started in February 2021.
Last May, Andrew and Alf entered a long-term lease for a dairy farm less than 0.5km from the home farm.
There are cubicles and grazing infrastructure present but Andrew and Alf have added to the existing infrastructure.
They are also in the middle of renovating the existing parlour and will move the 25-unit herringbone parlour from the home farm in the coming weeks.
The aim is to run this as a separate unit and milk 250 cows stocked at 3.3 LU/ha.

Originally built in 1975, the shed was moved, reerected and resheeted in 2002 to be used as a machienary and straw store.
This will bring cow numbers to 700 in 2022 with Andrew, Alf and three other full-time labour units, Ray Winters, Stephen Murphy and David O’Halloran. Peter McCann, the owner of the outfarm, does most of the milking there.
Breeding and EBI have been a key focus on the farm. All spring calving, the six-week calving rate in 2021 was 86%.
In 2020, there was 560kg MS/cow sold on a predominantly grass-based diet with 800kg meal fed per cow. They supply milk to both Glanbia and Lakeland Dairies.
“2020 was our fifth year in a row breaking 550kg MS/cow. Cow type and production is the key reason we can continue to grow the business,” says Andrew.
Milking facilities on the main platform have come under pressure in recent years with the increased cow numbers.
Originally, there was a basic 14-unit DeLaval parlour which was extended to 20 units in 2007 and a 10,000-litre bulk tank. In 2015, they sold the 20-unit parlour and put in a 25-unit DeLaval parlour which they were able to avail of the grant on.
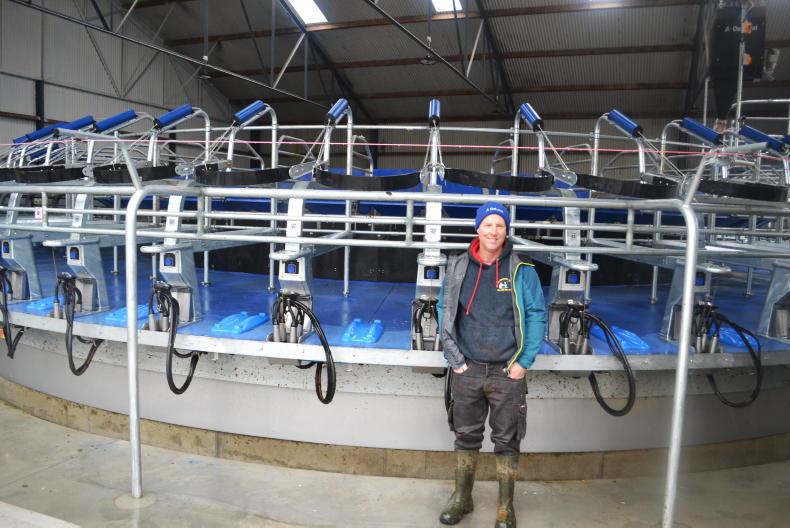
The first cow was milked in the rotary on 25 November 2021.
They also upgraded to a 20,000-litre DeLaval bulk tank.
As cow numbers have increased, so too did the numbers of rows going through the parlour. With 370 cows, there were almost 15 rows, which meant long milking periods.
Cow flow was poor and the collecting yard was also under pressure as cows had to be held in the cubicle shed before milking.
Making the switch to a rotary parlour
With plans to invest in a new milking parlour, they started to consider a rotary. As they were very happy with their local DeLaval service team in Marron Farm Services they were keen to stick with DeLaval. Looking around the yard, they considered the possibility of converting an existing shed or going to a greenfield site.

One shed that has been on the farm for decades was in an ideal location for access to the land and cubicles. The shed was originally built in 1975 as an indoor equestrian centre.
In 2002, Andrew took down the 10-bay shed and re-erected it as two five-bay sheds in the new yard.
Since then, one part has been a calf rearing shed and the other a straw and machinery store but it’s now home to the new milking parlour.
Ground work and building work were carried out by Thomas Kavanagh and Sean Devine. It started in late February with the tank in the collecting yard.

All the controls for the machine, drafter and backing gate are behind the milker.
Over 2,200t of shale and limestone rock was dug up and crushed during the process. All of this material was then used to improve roadways on the new milking platform.
Building resumed in May and it was full steam ahead until November. The DeLaval team started in late August and the first cow was milked on 23 November.
“Building a rotary parlour is a much more complex build than a herringbone parlour and you need a good builder who is willing to work with the engineer.

The handling facilities consist of an Alfco drafting gate, holding pens, a straight crush and a exit race that doubles up as a herringbone crush.
“We were very lucky here because Alf and the team could look after the cows while I became a project manager and ‘go-for’ for the builder,” says Andrew.
Andrew also says that Liam Flood, a DeLaval engineer, was an excellent support to both him and the builder during the process.
When it came to the spec of the parlour, they visited a number of different farms around the country and decided what they liked.
In the end, they put in a 50-bail DeLaval E100 rotary with comfort bail ACR, auto retention, feeding and auto wash.

One feature of the parlour Andrew was very happy with was the cluster drop.
This is when the cluster comes off the cow; it drops down and passes under the bridge where cows enter and exit the rotary.
During their tour of different rotaries, they were told that where this feature is not included cows can sometimes get caught in the cluster and pull it as they exit which delays milking.
Unlike other systems where there is an auto-teat spray under each cow they went with the WETIT automatic teat spray unit.

The WETIT automatic teat spray is a New Zealand product that is located just before the cow exit.
This is a New Zealand product and is just one device close to the exit that sprays each cow.
Andrew is very happy with it so far and says it saves having to go into the centre of the rotary to refill the teat spray as it is plumbed externally.
There was a lot of thought and effort put into the collecting yard and handling facilities.
Design
Kieran Kerrigan from Alfco Farm Services designed and supplied the backing gate and drafting gate. These work in tandem and, as each group of 12 cows exits through the drafting gate, the backing gate moves forward.

The cluster drop feature allows the cluster to pass under the bridge and avoids cows getting caught in the cluster when exiting.
Condon Engineering supplied the gates, the crush and the exit race, which also doubles up into a herringbone crush.
“We used the herringbone crush for the first time in early December and it was excellent. It will save a lot of time in the future,” says Andrew.
When designing the collecting yard and handling facilities they were very conscious of the falls in the yard.

Since 2015 Flogas instant water heating has been used to heat the water on the farm.
In some yards, they visited the handling facilities were at the same slope as the collecting yard and they noticed cows were bunching in the drafting pens.
To improve cow comfort, they graded the handling facilities at 1% and the collecting yard at 3%.
Transition from herringbone
to rotary
As the cows have all been milked in a herringbone, Andrew says they are very impressed by how fast they have taken to the rotary.
Having the cows trained now will take a lot of pressure off next spring.
Everyone on the farm is looking forward to when both the cows and milker are settled into the new system.

The 25-unit parlour was installed in 2015 and will be moved to the new milking platform for spring 2022.
“The first day, it took three hours to get the 300 cows on to the rotary and they have got much better with each milking since.”
All concrete work including tanks, the rotary, walls and floors came to €170,000. The machine: €290,000.Drafting and backing gate: €30,000.Electricity and gas: €20,000.Plumbing: €10,000 (own labour).The whole project to date has cost in the region of €520,000.
Andrew Purcell and Alf McGlew are neighbouring dairy farmers and, in 2007, they entered a collaborative farming partnership.
This year, they completed the jump from their 25-unit herringbone parlour into a new DeLaval 50-bail rotary parlour which they have been milking in since 23 November.
Over the last 14 years of working together, they have taken on more ground and increased cow numbers.
Now stocked at 3.3LU/ha, they are milking 370 cows on the home platform. During this time, they took on a second milking platform and are now milking 80 cows there. In 2021, a total of 450 cows were milked between both platforms.
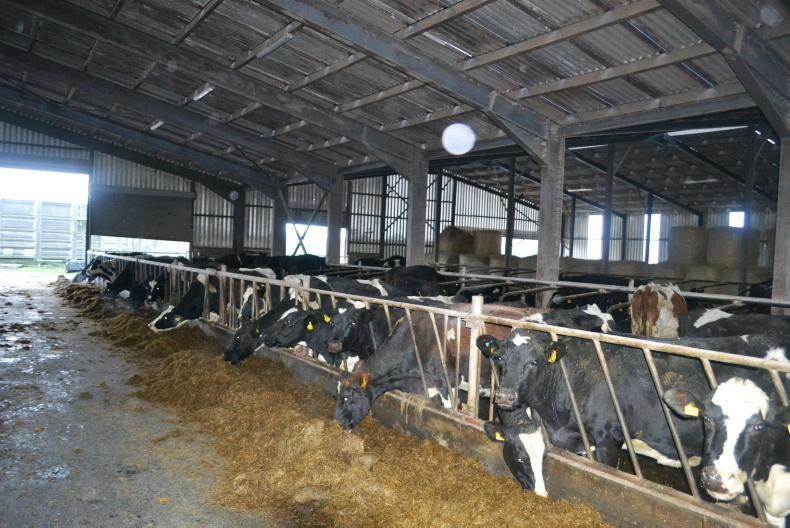
All 450 cows are wintered and calved on the home farm and at the beginning of March each year, 80 cows are moved to the second block.
Silage comes from support blocks that are not on the main platform and the replacement heifers are reared on this ground too.
Cow numbers grew from 140 to 240 between 2007 and 2015. Cow type has also changed since the beginning of the partnership.
In 2008, they crossed the herd with Jersey and some Norwegian red. They are now milking a predominantly Jersey cross herd of cows.

The work started in February 2021.
Last May, Andrew and Alf entered a long-term lease for a dairy farm less than 0.5km from the home farm.
There are cubicles and grazing infrastructure present but Andrew and Alf have added to the existing infrastructure.
They are also in the middle of renovating the existing parlour and will move the 25-unit herringbone parlour from the home farm in the coming weeks.
The aim is to run this as a separate unit and milk 250 cows stocked at 3.3 LU/ha.

Originally built in 1975, the shed was moved, reerected and resheeted in 2002 to be used as a machienary and straw store.
This will bring cow numbers to 700 in 2022 with Andrew, Alf and three other full-time labour units, Ray Winters, Stephen Murphy and David O’Halloran. Peter McCann, the owner of the outfarm, does most of the milking there.
Breeding and EBI have been a key focus on the farm. All spring calving, the six-week calving rate in 2021 was 86%.
In 2020, there was 560kg MS/cow sold on a predominantly grass-based diet with 800kg meal fed per cow. They supply milk to both Glanbia and Lakeland Dairies.
“2020 was our fifth year in a row breaking 550kg MS/cow. Cow type and production is the key reason we can continue to grow the business,” says Andrew.
Milking facilities on the main platform have come under pressure in recent years with the increased cow numbers.
Originally, there was a basic 14-unit DeLaval parlour which was extended to 20 units in 2007 and a 10,000-litre bulk tank. In 2015, they sold the 20-unit parlour and put in a 25-unit DeLaval parlour which they were able to avail of the grant on.
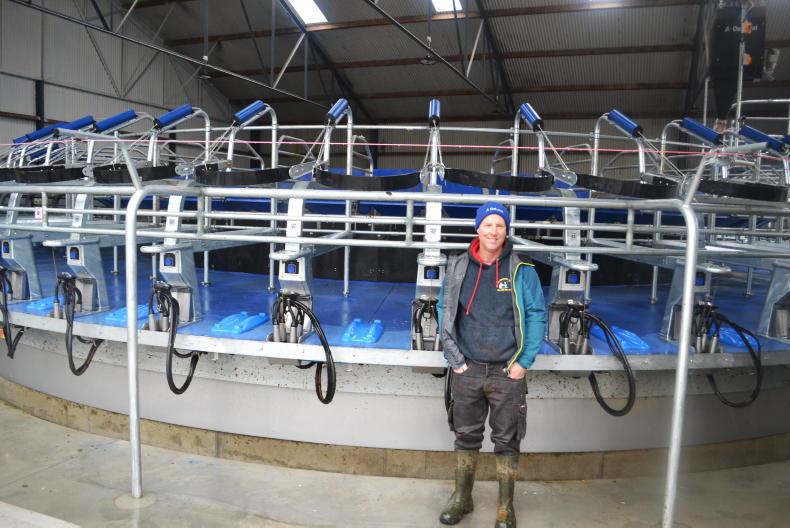
The first cow was milked in the rotary on 25 November 2021.
They also upgraded to a 20,000-litre DeLaval bulk tank.
As cow numbers have increased, so too did the numbers of rows going through the parlour. With 370 cows, there were almost 15 rows, which meant long milking periods.
Cow flow was poor and the collecting yard was also under pressure as cows had to be held in the cubicle shed before milking.
Making the switch to a rotary parlour
With plans to invest in a new milking parlour, they started to consider a rotary. As they were very happy with their local DeLaval service team in Marron Farm Services they were keen to stick with DeLaval. Looking around the yard, they considered the possibility of converting an existing shed or going to a greenfield site.

One shed that has been on the farm for decades was in an ideal location for access to the land and cubicles. The shed was originally built in 1975 as an indoor equestrian centre.
In 2002, Andrew took down the 10-bay shed and re-erected it as two five-bay sheds in the new yard.
Since then, one part has been a calf rearing shed and the other a straw and machinery store but it’s now home to the new milking parlour.
Ground work and building work were carried out by Thomas Kavanagh and Sean Devine. It started in late February with the tank in the collecting yard.

All the controls for the machine, drafter and backing gate are behind the milker.
Over 2,200t of shale and limestone rock was dug up and crushed during the process. All of this material was then used to improve roadways on the new milking platform.
Building resumed in May and it was full steam ahead until November. The DeLaval team started in late August and the first cow was milked on 23 November.
“Building a rotary parlour is a much more complex build than a herringbone parlour and you need a good builder who is willing to work with the engineer.

The handling facilities consist of an Alfco drafting gate, holding pens, a straight crush and a exit race that doubles up as a herringbone crush.
“We were very lucky here because Alf and the team could look after the cows while I became a project manager and ‘go-for’ for the builder,” says Andrew.
Andrew also says that Liam Flood, a DeLaval engineer, was an excellent support to both him and the builder during the process.
When it came to the spec of the parlour, they visited a number of different farms around the country and decided what they liked.
In the end, they put in a 50-bail DeLaval E100 rotary with comfort bail ACR, auto retention, feeding and auto wash.

One feature of the parlour Andrew was very happy with was the cluster drop.
This is when the cluster comes off the cow; it drops down and passes under the bridge where cows enter and exit the rotary.
During their tour of different rotaries, they were told that where this feature is not included cows can sometimes get caught in the cluster and pull it as they exit which delays milking.
Unlike other systems where there is an auto-teat spray under each cow they went with the WETIT automatic teat spray unit.

The WETIT automatic teat spray is a New Zealand product that is located just before the cow exit.
This is a New Zealand product and is just one device close to the exit that sprays each cow.
Andrew is very happy with it so far and says it saves having to go into the centre of the rotary to refill the teat spray as it is plumbed externally.
There was a lot of thought and effort put into the collecting yard and handling facilities.
Design
Kieran Kerrigan from Alfco Farm Services designed and supplied the backing gate and drafting gate. These work in tandem and, as each group of 12 cows exits through the drafting gate, the backing gate moves forward.

The cluster drop feature allows the cluster to pass under the bridge and avoids cows getting caught in the cluster when exiting.
Condon Engineering supplied the gates, the crush and the exit race, which also doubles up into a herringbone crush.
“We used the herringbone crush for the first time in early December and it was excellent. It will save a lot of time in the future,” says Andrew.
When designing the collecting yard and handling facilities they were very conscious of the falls in the yard.

Since 2015 Flogas instant water heating has been used to heat the water on the farm.
In some yards, they visited the handling facilities were at the same slope as the collecting yard and they noticed cows were bunching in the drafting pens.
To improve cow comfort, they graded the handling facilities at 1% and the collecting yard at 3%.
Transition from herringbone
to rotary
As the cows have all been milked in a herringbone, Andrew says they are very impressed by how fast they have taken to the rotary.
Having the cows trained now will take a lot of pressure off next spring.
Everyone on the farm is looking forward to when both the cows and milker are settled into the new system.

The 25-unit parlour was installed in 2015 and will be moved to the new milking platform for spring 2022.
“The first day, it took three hours to get the 300 cows on to the rotary and they have got much better with each milking since.”
All concrete work including tanks, the rotary, walls and floors came to €170,000. The machine: €290,000.Drafting and backing gate: €30,000.Electricity and gas: €20,000.Plumbing: €10,000 (own labour).The whole project to date has cost in the region of €520,000.
SHARING OPTIONS: