The Mullen family based in Kilmainham, Kells, Co Meath, have 10 months milking under their belt with their new state-of-the-art Swiftflow rapid-exit milking parlour. The parlour and handling facilities were completed in February of this year and the development has made a huge difference to the busy 350-cow dairy farm.
Matthew Mullen has been farming full-time with his father Declan, mother Gladys and uncle Gerry Mullen for two years now in a registered farm partnership, with Declan junior helping out in the evenings after school and weekends.

The Mullens: Matthew, Declan senior and Declan junior in their new milking parlour in Kells, Co Meath.
The family have a liquid milk contract with Glanbia which allows them to milk 130 cows during the winter months. This leaves the remainder of the cows calving in the springtime.
Cow numbers have doubled on this farm since the abolition of dairy quotas. Before building the new parlour, they were struggling with the old 10-unit herringbone machine.
Matthew said: “We were spending up to five hours in the morning to milk 270 cows last year.”
Declan said that it had got to the point that a larger parlour was essential to manage the farm efficiently.
The shed
The big question a lot of readers might be wondering is why the family chose rapid-exit over rotary.
Matthew said that they had considered rotary but after talking to David Smith from Cookstown Dairy Services based in Louth, the family decided to go with a rapid exit parlour as it best suited their setup. The rapid-exit parlour offered greater speed milking a larger number of cows compared to the traditional herringbone with more efficiency.
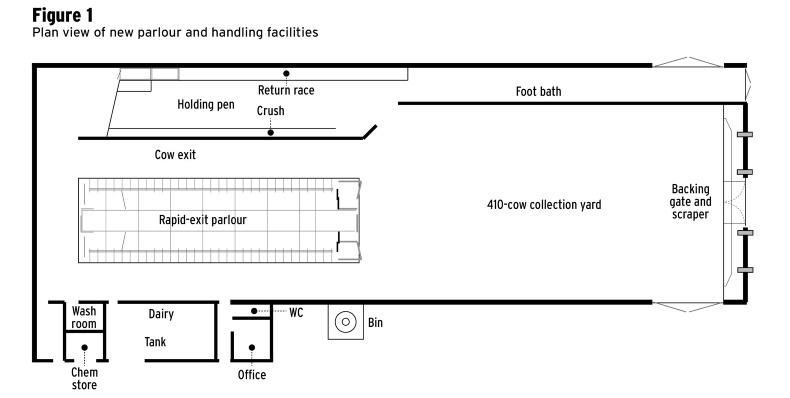
To accommodate this new parlour, a large collecting yard, shed and handling facilities were constructed to the rear of the existing farmyard and cubicles.
Efficiency
The rapid-exit parlour has made a huge difference to milking times compared to the old setup.
They installed a 26-unit Dairymaster Swiftflow rapid exit parlour and left space for four more units when needed in the future. Rapid-exit parlours are very similar to a traditional herringbone parlour.
The main difference is what its name suggests – cows exit the parlour quickly. When a row of cows are milked, the milker pushes a lever and all of the bailing and feed bins rise up above the cows. This means instead of queuing up to exit the parlour, a cow can exit in seconds. This speeds up milking time substantially.
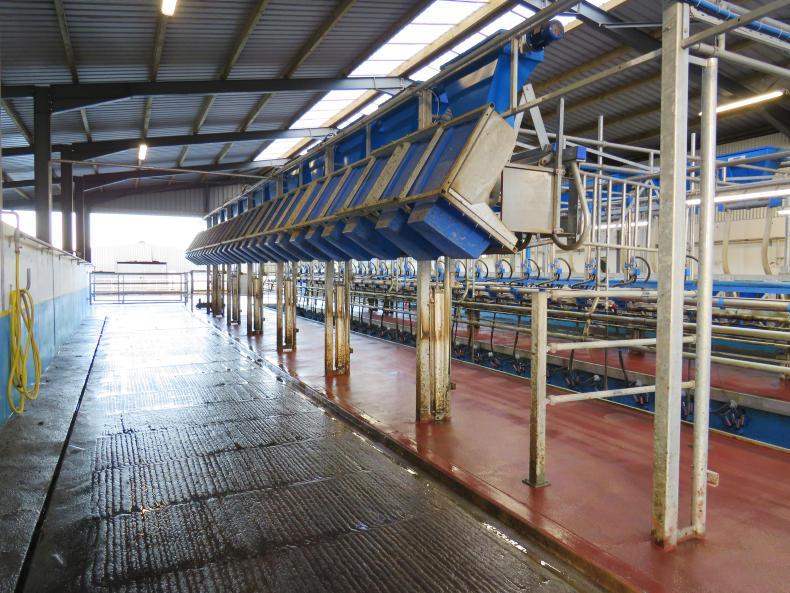
There is sequential bailing in the parlour which gives each cow an individual space to stand during milking. The bailing makes milking more efficient and helps cut out instances where an extra cow pushes her way into a row, upsetting the milking routine.
The parlour has electronic feeders with a feed-to-yield system. There are automatic cluster removers and a dump line all controlled by an auto ID that reads the EID tag in the cow’s ear as she enters the parlour.
“If a cow has been treated for mastitis the computer system in the parlour will warn us before we put on the cups,” Declan junior explained.
This is a useful addition used in conjunction with the normal antibiotic controls already in existence on the farm.
Drafting
After cows exit the parlour they walk through the Dairymaster drafting system. Normally cows will walk straight through this drafting system back to the cubicles or to grass depending on the time of year.
If a cow has been selected to be drafted in the parlour for breeding, veterinary or further inspection, when she walks through the drafting system the gate will open in front of the cow and direct her into a holding pen.

The Mullens are very happy with the drafting system and said it is working extremely well. The slatted flow channel was placed along the main route that cows use to exit the drafting area which really helps to cut down the washing time after milking.
This flow channel is connected to the slatted tank at the bottom of the collecting yard. Declan senior said he wanted the footbath a couple of metres away from the end of the race for easy access, so cows could evaluate the footbath before passing through, this has proven to be very successful.
Yard
The collecting yard is 535m2 and at 1.3m2 per cow it can hold 410 cows and is designed to accommodate more cows in the future when the need arises.
There is a 9ft deep slatted tank at the end of the yard which is capped off with 16ft 6in slats, with agitation points on either side of the tank.

Ciaran Smith of Mount Nugent, Co Cavan, carried out all of the concrete work and erected the shed.
There is an automatic backing gate in this yard also supplied by Dairymaster. It can be set to move forward a few metres at a time automatically or continuously on demand. It is a dual-purpose backing gate with ratchet scrapers underneath the gate which clean the yard and push any slurry back to the slatted tank.
There are plates on top of every girder in the collecting yard which will allow for the erecting of a roof over it in the future if needed. There are integrated handling facilities within the drafting area which provide easy accessibility for the general handling of cows or during herd tests.
Other investments
Some other substantial investments within the shed include a 30,100l Dairymaster bulk tank, a plate cooler, heat recovery system and variable speed pump to reduce electricity usage.
The instalment of an auto washer cuts out labour as it does not need to be supervised while in use, which in turn means that the lads have more time to carry out other jobs.
A large 25t V-mac silo was erected also which will allow for the purchase of a full load of ration at a time. They’ve also built an underground water tank to collect the washings of the milking machine.
Cost
The total expenditure of all building works carried out came to a sum of €408,500 excluding VAT. This project was carried out with the aid of the Targeted Agricultural Modernisation Scheme (TAMS) II for the parlour equipment.
New rapid-exit parlour installed on 350-cow dairy farm in Meath.Replaces 10-unit herringbone parlour.Milking times have dropped from five hours to 1.5 hours per milking.Extras include auto ID, automatic cluster removers, dump line and auto drafter
The Mullen family based in Kilmainham, Kells, Co Meath, have 10 months milking under their belt with their new state-of-the-art Swiftflow rapid-exit milking parlour. The parlour and handling facilities were completed in February of this year and the development has made a huge difference to the busy 350-cow dairy farm.
Matthew Mullen has been farming full-time with his father Declan, mother Gladys and uncle Gerry Mullen for two years now in a registered farm partnership, with Declan junior helping out in the evenings after school and weekends.

The Mullens: Matthew, Declan senior and Declan junior in their new milking parlour in Kells, Co Meath.
The family have a liquid milk contract with Glanbia which allows them to milk 130 cows during the winter months. This leaves the remainder of the cows calving in the springtime.
Cow numbers have doubled on this farm since the abolition of dairy quotas. Before building the new parlour, they were struggling with the old 10-unit herringbone machine.
Matthew said: “We were spending up to five hours in the morning to milk 270 cows last year.”
Declan said that it had got to the point that a larger parlour was essential to manage the farm efficiently.
The shed
The big question a lot of readers might be wondering is why the family chose rapid-exit over rotary.
Matthew said that they had considered rotary but after talking to David Smith from Cookstown Dairy Services based in Louth, the family decided to go with a rapid exit parlour as it best suited their setup. The rapid-exit parlour offered greater speed milking a larger number of cows compared to the traditional herringbone with more efficiency.
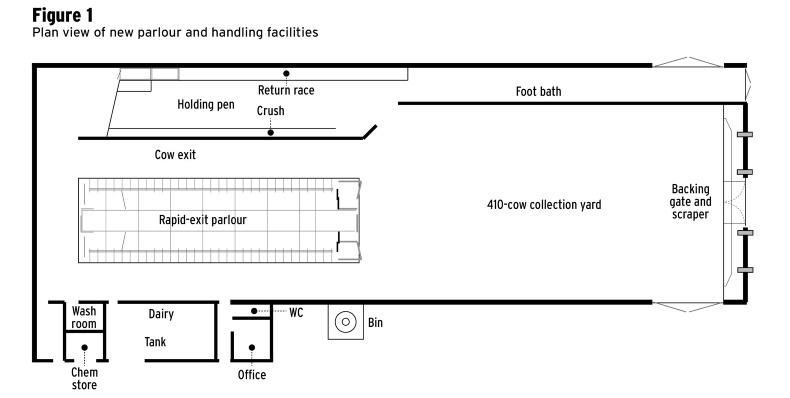
To accommodate this new parlour, a large collecting yard, shed and handling facilities were constructed to the rear of the existing farmyard and cubicles.
Efficiency
The rapid-exit parlour has made a huge difference to milking times compared to the old setup.
They installed a 26-unit Dairymaster Swiftflow rapid exit parlour and left space for four more units when needed in the future. Rapid-exit parlours are very similar to a traditional herringbone parlour.
The main difference is what its name suggests – cows exit the parlour quickly. When a row of cows are milked, the milker pushes a lever and all of the bailing and feed bins rise up above the cows. This means instead of queuing up to exit the parlour, a cow can exit in seconds. This speeds up milking time substantially.
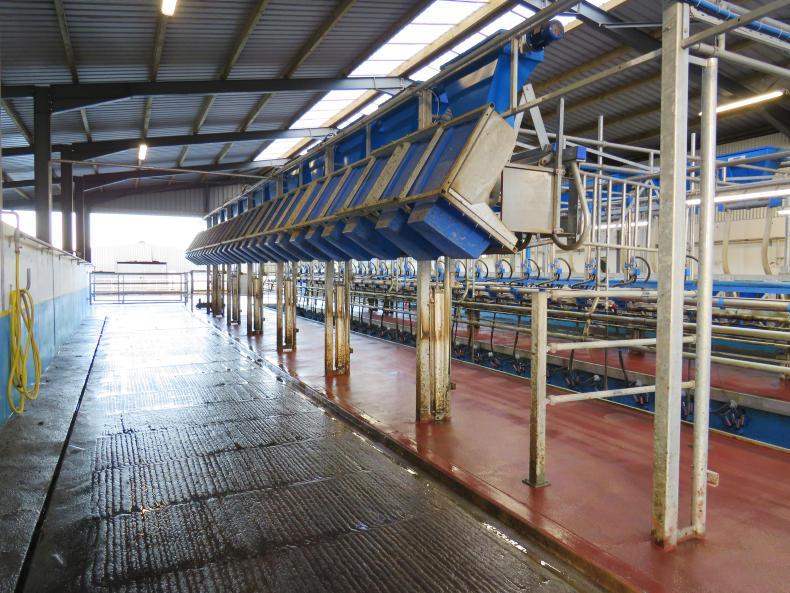
There is sequential bailing in the parlour which gives each cow an individual space to stand during milking. The bailing makes milking more efficient and helps cut out instances where an extra cow pushes her way into a row, upsetting the milking routine.
The parlour has electronic feeders with a feed-to-yield system. There are automatic cluster removers and a dump line all controlled by an auto ID that reads the EID tag in the cow’s ear as she enters the parlour.
“If a cow has been treated for mastitis the computer system in the parlour will warn us before we put on the cups,” Declan junior explained.
This is a useful addition used in conjunction with the normal antibiotic controls already in existence on the farm.
Drafting
After cows exit the parlour they walk through the Dairymaster drafting system. Normally cows will walk straight through this drafting system back to the cubicles or to grass depending on the time of year.
If a cow has been selected to be drafted in the parlour for breeding, veterinary or further inspection, when she walks through the drafting system the gate will open in front of the cow and direct her into a holding pen.

The Mullens are very happy with the drafting system and said it is working extremely well. The slatted flow channel was placed along the main route that cows use to exit the drafting area which really helps to cut down the washing time after milking.
This flow channel is connected to the slatted tank at the bottom of the collecting yard. Declan senior said he wanted the footbath a couple of metres away from the end of the race for easy access, so cows could evaluate the footbath before passing through, this has proven to be very successful.
Yard
The collecting yard is 535m2 and at 1.3m2 per cow it can hold 410 cows and is designed to accommodate more cows in the future when the need arises.
There is a 9ft deep slatted tank at the end of the yard which is capped off with 16ft 6in slats, with agitation points on either side of the tank.

Ciaran Smith of Mount Nugent, Co Cavan, carried out all of the concrete work and erected the shed.
There is an automatic backing gate in this yard also supplied by Dairymaster. It can be set to move forward a few metres at a time automatically or continuously on demand. It is a dual-purpose backing gate with ratchet scrapers underneath the gate which clean the yard and push any slurry back to the slatted tank.
There are plates on top of every girder in the collecting yard which will allow for the erecting of a roof over it in the future if needed. There are integrated handling facilities within the drafting area which provide easy accessibility for the general handling of cows or during herd tests.
Other investments
Some other substantial investments within the shed include a 30,100l Dairymaster bulk tank, a plate cooler, heat recovery system and variable speed pump to reduce electricity usage.
The instalment of an auto washer cuts out labour as it does not need to be supervised while in use, which in turn means that the lads have more time to carry out other jobs.
A large 25t V-mac silo was erected also which will allow for the purchase of a full load of ration at a time. They’ve also built an underground water tank to collect the washings of the milking machine.
Cost
The total expenditure of all building works carried out came to a sum of €408,500 excluding VAT. This project was carried out with the aid of the Targeted Agricultural Modernisation Scheme (TAMS) II for the parlour equipment.
New rapid-exit parlour installed on 350-cow dairy farm in Meath.Replaces 10-unit herringbone parlour.Milking times have dropped from five hours to 1.5 hours per milking.Extras include auto ID, automatic cluster removers, dump line and auto drafter
SHARING OPTIONS: