This time of year is traditionally a quiet time on many farms. Where ploughing for 2018 cannot be carried out, virtually all other field operations are now completed.
The long list of jobs which were put off during the year now fill the days, while others are confined to workshops where the annual machinery service and repairs take place.
But this quiet time also serves as a perfect opportunity to ensure that your chemical records are up to date, regardless of what type of farm you are on. In 2016, 36% of pesticide-related offences uncovered during cross-compliance inspections related to a product registration breach. This could be as simple as stating the incorrect water levels as instructed on the label. These breaches were most likely discovered as a result of poor application record-keeping. A further 9% of offences related to inadequate purchase records. Therefore, having your records in order can save you a potential penalty on your BPS payment, saving you both time and money down the line.
The pesticide section of a cross-compliance inspection is divided into seven parts:
Part one: storage of plant protection and biocidal products.Part two: handling of plant protection and biocidal products.Part three: maintenance of records on plant protection and biocidal products.Part four: checks to ensure that application equipment used is suitable and properly calibrated.Part five: checks to ensure that plant protection and biocidal products used and those in-store are registered, and are appropriate for the crops grown and the enterprises on the holding.Part six: checks to ensure that the plant protection and biocidal products used, and the timing and numbers of applications/treatments reflect approved label instructions.Part seven: checks to ensure that the principles of good plant protection practice and, where appropriate, integrated control techniques have been followed.Each section accounts for a certain amount of marks which are added together to give an overall result. This article will focus on the pesticide records you may be asked to produce on the day of an inspection and the common mistakes which farmers fall down on.
The law for farmers
Under the Sustainable Use Directive, only a registered professional user can apply pesticides authorised for professional use.
All farmers applying their own chemicals should now be registered as a professional user and if they purchase, apply or store pesticides on their farm then they are responsible for maintaining records pertaining to these. In addition to this, if a third party contractor is used to apply pesticides, their name and address as well as PU number will also be required.
Pesticide application record
The most important records to have on hand during an inspection are pesticide application records. Generally, most farmers will keep their own field logs throughout the year when spraying and then transfer them to the Department’s template at a later date. These field logs may also be required to be produced during an inspection. There are numerous software programmes available today which can assist in keeping these records. Ideally, logs should be kept for each individual fields, but this is not always necessary and may lead to repetition. Instead, logs can be kept on a crop-by-crop basis.
On the pesticide application record template supplied by the Department, the location/LPIS number of the field in question must be filled in. However, if multiple land parcels with the same crop are receiving the same spray programme, the Department will accept one record as long as all relevant LPIS numbers are included.

When filling in the product name and PCS number, the Department recommends that these are taken directly from the product container, as opposed to invoices, receipts or websites.
Ensure that that you have not applied a product onto a crop for which it is not cleared and that you have not exceed the maximum individual or the maximum combined dose.
Farmers can easily get caught out on this issue as the rates listed on this record will be used to calculate what inventory should be in your chemical store. Ensure that the dates on which you applied a chemical are in line with the recommended timings on the product label. While this will be hard to prove, inspectors will be looking for any abnormalities.
If you are availing of the STRIPE (Surface water Tool for Reducing the Impact of Pesticides on the Environment) initiative and have reduced buffer zones by 75% or 90%, be sure to indicate this. The integrated pest management (IPM) rationale must be included, as this will be the basis for justifying the use of the chemical. This brief explanation is in addition to the separate integrated pest management record sheet, which must also be maintained.
Finally, the PU number of the person applying the plant protection product is required beside every application. Mistakes made when filling out application records will result in penalties. An example of a single application record is shown in Table 1.
Table 1: A pesticide application record entry for a treatment with BiPlay SX showing the details required.

Chemical store inventory
During an inspection, the inspector will record all chemicals present in the chemical store. The Department states that farmers should also keep an inventory of all chemical in the store, but this may not always be asked for by the inspector. This is where many farmers can get caught out.
When chemical stocks are inspected, they will be cross-checked with the information on the application records.
For example, if you applied 0.7 litres/ha of High Load Mircam on 30ha of spring barley, you should have applied 21 litres. If you only purchased 20 litres then you must have had one litre in stock to begin with, or you have returned the product to the supplier. You may be asked to prove this.

Product purchase, return and disposals
Farmers may also be asked to produce records on any purchase, returns and disposals of chemicals. Details of the name and address of the supplier of product, its brand name, PCS number, pack size, amount of product received and the date of purchase, disposal or return may be required.
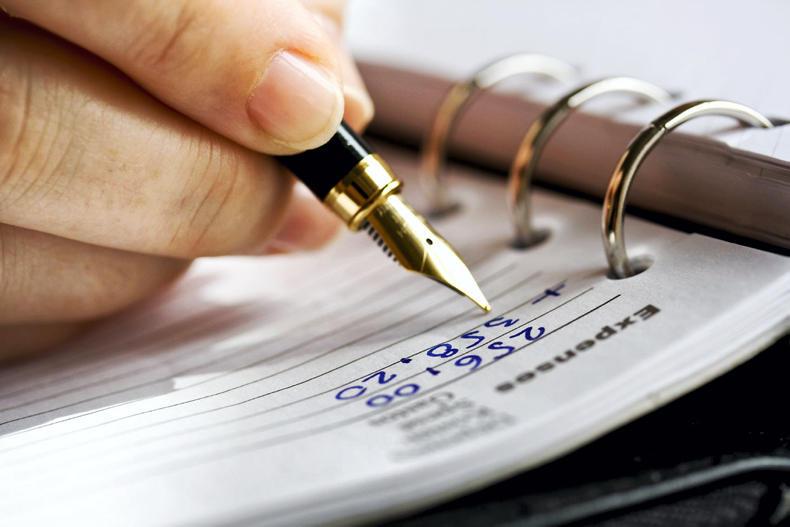
Table 2: Sheet on which to log chemical purchases or inventories.

Integrated pest management (IPM) record sheet
IPM records may be required on the day of the inspection or at a later date. These records demonstrate the application of the general IPM principles. In addition to the IPM column on the pesticide application record, a ‘tick box’ worksheet is also distributed to farmers (through the basic payment scheme pack) to demonstrate how they are adopting the general principles of IPM .
Read more
’A single drop of MCPA in an Olympic-size pool will contaminate the water’
More than 27,500 registered to spray
This time of year is traditionally a quiet time on many farms. Where ploughing for 2018 cannot be carried out, virtually all other field operations are now completed.
The long list of jobs which were put off during the year now fill the days, while others are confined to workshops where the annual machinery service and repairs take place.
But this quiet time also serves as a perfect opportunity to ensure that your chemical records are up to date, regardless of what type of farm you are on. In 2016, 36% of pesticide-related offences uncovered during cross-compliance inspections related to a product registration breach. This could be as simple as stating the incorrect water levels as instructed on the label. These breaches were most likely discovered as a result of poor application record-keeping. A further 9% of offences related to inadequate purchase records. Therefore, having your records in order can save you a potential penalty on your BPS payment, saving you both time and money down the line.
The pesticide section of a cross-compliance inspection is divided into seven parts:
Part one: storage of plant protection and biocidal products.Part two: handling of plant protection and biocidal products.Part three: maintenance of records on plant protection and biocidal products.Part four: checks to ensure that application equipment used is suitable and properly calibrated.Part five: checks to ensure that plant protection and biocidal products used and those in-store are registered, and are appropriate for the crops grown and the enterprises on the holding.Part six: checks to ensure that the plant protection and biocidal products used, and the timing and numbers of applications/treatments reflect approved label instructions.Part seven: checks to ensure that the principles of good plant protection practice and, where appropriate, integrated control techniques have been followed.Each section accounts for a certain amount of marks which are added together to give an overall result. This article will focus on the pesticide records you may be asked to produce on the day of an inspection and the common mistakes which farmers fall down on.
The law for farmers
Under the Sustainable Use Directive, only a registered professional user can apply pesticides authorised for professional use.
All farmers applying their own chemicals should now be registered as a professional user and if they purchase, apply or store pesticides on their farm then they are responsible for maintaining records pertaining to these. In addition to this, if a third party contractor is used to apply pesticides, their name and address as well as PU number will also be required.
Pesticide application record
The most important records to have on hand during an inspection are pesticide application records. Generally, most farmers will keep their own field logs throughout the year when spraying and then transfer them to the Department’s template at a later date. These field logs may also be required to be produced during an inspection. There are numerous software programmes available today which can assist in keeping these records. Ideally, logs should be kept for each individual fields, but this is not always necessary and may lead to repetition. Instead, logs can be kept on a crop-by-crop basis.
On the pesticide application record template supplied by the Department, the location/LPIS number of the field in question must be filled in. However, if multiple land parcels with the same crop are receiving the same spray programme, the Department will accept one record as long as all relevant LPIS numbers are included.

When filling in the product name and PCS number, the Department recommends that these are taken directly from the product container, as opposed to invoices, receipts or websites.
Ensure that that you have not applied a product onto a crop for which it is not cleared and that you have not exceed the maximum individual or the maximum combined dose.
Farmers can easily get caught out on this issue as the rates listed on this record will be used to calculate what inventory should be in your chemical store. Ensure that the dates on which you applied a chemical are in line with the recommended timings on the product label. While this will be hard to prove, inspectors will be looking for any abnormalities.
If you are availing of the STRIPE (Surface water Tool for Reducing the Impact of Pesticides on the Environment) initiative and have reduced buffer zones by 75% or 90%, be sure to indicate this. The integrated pest management (IPM) rationale must be included, as this will be the basis for justifying the use of the chemical. This brief explanation is in addition to the separate integrated pest management record sheet, which must also be maintained.
Finally, the PU number of the person applying the plant protection product is required beside every application. Mistakes made when filling out application records will result in penalties. An example of a single application record is shown in Table 1.
Table 1: A pesticide application record entry for a treatment with BiPlay SX showing the details required.

Chemical store inventory
During an inspection, the inspector will record all chemicals present in the chemical store. The Department states that farmers should also keep an inventory of all chemical in the store, but this may not always be asked for by the inspector. This is where many farmers can get caught out.
When chemical stocks are inspected, they will be cross-checked with the information on the application records.
For example, if you applied 0.7 litres/ha of High Load Mircam on 30ha of spring barley, you should have applied 21 litres. If you only purchased 20 litres then you must have had one litre in stock to begin with, or you have returned the product to the supplier. You may be asked to prove this.

Product purchase, return and disposals
Farmers may also be asked to produce records on any purchase, returns and disposals of chemicals. Details of the name and address of the supplier of product, its brand name, PCS number, pack size, amount of product received and the date of purchase, disposal or return may be required.
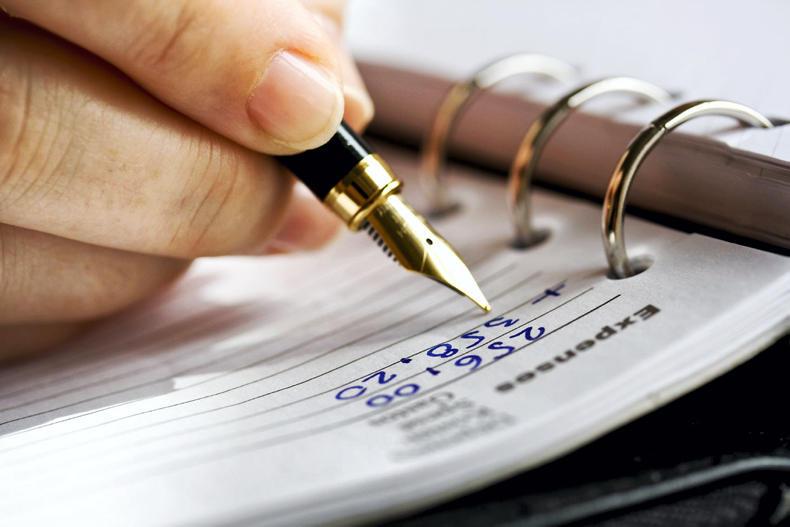
Table 2: Sheet on which to log chemical purchases or inventories.

Integrated pest management (IPM) record sheet
IPM records may be required on the day of the inspection or at a later date. These records demonstrate the application of the general IPM principles. In addition to the IPM column on the pesticide application record, a ‘tick box’ worksheet is also distributed to farmers (through the basic payment scheme pack) to demonstrate how they are adopting the general principles of IPM .
Read more
’A single drop of MCPA in an Olympic-size pool will contaminate the water’
More than 27,500 registered to spray
SHARING OPTIONS: