A few months ago, I had occasion to make an unscheduled visit to Agrifac in a town called Steenwijk in northern Netherlands.
Some may know the name of this machinery manufacturer – most may not have heard of it before. Agrifac makes two major lines of machinery – beet harvesters and self-propelled sprayers. And what they make is big and sophisticated.
There were a few things that struck me in particular about the operation.
Firstly, they seem to make nothing, ie it seems to be an assembly plant for parts made elsewhere.
Secondly, they make big and sophisticated machinery with sprayers up to 55m boom width and beet harvesters up to 12 rows sitting on three hydraulically powered axles.
Each of the four wheels is driven by its own hydraulic motor
Interestingly, our guide said that this big 12-row beet harvester was produced initially many years ago but it gained no popularity at the time. It was relaunched a few years ago and has been selling very well since.
The comment was that the initial machine was ahead of its time but the arrival of much bigger tractor and trailer units on farms has now provided matching capacity for this big harvester as the units of 10 to 15 years ago were too small for its capacity.
Assembly only
The assembly plant produces sprayers for just over six months of the year and harvesters for about the same. As with most other manufacturers, units are made to order and they are highly personalised.
While all the individual components are outsourced, a spokesman for the company told me that they do not purchase on price. Virtually all parts are manufactured within a modest radius of the assembly plant.
“Attempting to source the cheapest components on price alone from either Eastern Europe or further afield might look better on the bottom line but downtime on any machine is highly significant for customers and could be very damaging to the reputation of the company,” the guide stated.
Most of the engines used are Iveco because these same engines are present in many tractors and in other farm machinery. So there will be local expertise in most areas of the world where these machines might be purchased. They also use Volvo engines in some of their bigger 350+hp units.
They source very high quality hydraulic and other components. If a machine broke down in a field in Ukraine or Russia it would take up to eight days to drive there with the parts for repair. So the main objective is not to have machines that will break down.
Because of the absolute necessity to avoid unintentional stoppages, all machines are fitted with a unit that communicates between the factory and each individual machine. This means that each machine is always remotely monitored and, in general, the factory will know of an impending breakage before the operator does and he will be told that by phone.
Sophisticated precision
All sprayers are fitted with GPS precision controls for operation and steering. Boom sizes go from 24m to 55m width. Asked if such big units were going to the open prairie lands of Australia or America, the answer was “not necessarily”.
“Some do, but many go to local farmers who are operating on expensive local rented land but the users of these big units are growing valuable crops. Expensive land and valuable crops generate a benefit from these big widths so as to minimise the number of tram tracks in a field.”
Sprayers can have different levels of sophistication but all are fitted with an independent suspension system that can be used to raise the height of the under-body above the crop to give a clearance of up to 2m.
The spraying system itself is a modified Airtec system which uses a combination of liquid and air to generate the required droplet size.
To facilitate variable rate (or reduced rate from a given/set application rate) they can use pulsing nozzles. These can be used to decrease the application volume on the move by adjusting their on/off time.
These sophisticated pulsing nozzles can turn off or on the spray liquid up to 100 times per second. So if every second pulse is off the spray volume in that patch could, say, drop from 100 l/ha to 50 l/ha. This means that the liquid pressure and droplet size are barely affected, even though rate has been decreased.
Two spray lines
Imagine having a 55m boom width and changing from one application volume to another for different crops or targets. This would mean changing/turning around 110 different nozzles – a job in itself. It would also be a 110m round trip from the cab.
In that part of the world, it would not be uncommon for a farmer to spray pesticides in morning when the wind is low and then switch to liquid fertiliser in the afternoon when wind speeds rise. Drift would not be an issue as this would be a much coarser spray using a very different nozzle.
To avoid having to alter every nozzle, the sprayer boom can be fitted with a second spray line and a specialised nozzle set. The second line has nozzles that are offset by 25cm.
Each of the two lines can then be turned off or on from the cab meaning virtually no lost time.
Blocked nozzles
Blocked nozzles are a very common problem in spraying. They mean turning off the boom; walking to clear the problem nozzle; back to the controls and boom-on again to re-check. This could take a lot of time if you got dirty water or a batch of crystallised spray.
To avoid the need to walk to and from the cab each time to turn the boom on and off, these sprayers can be fitted with a device which can be controlled using an app on a smartphone. Using this, the operator can turn the boom on and off to check nozzle blockage.
Sprayer units at the moderate end are priced between €250,000 and €300,000. Tank size can now go up to 8,000 litres and with huge technological sophistication available, prices can go much higher also.
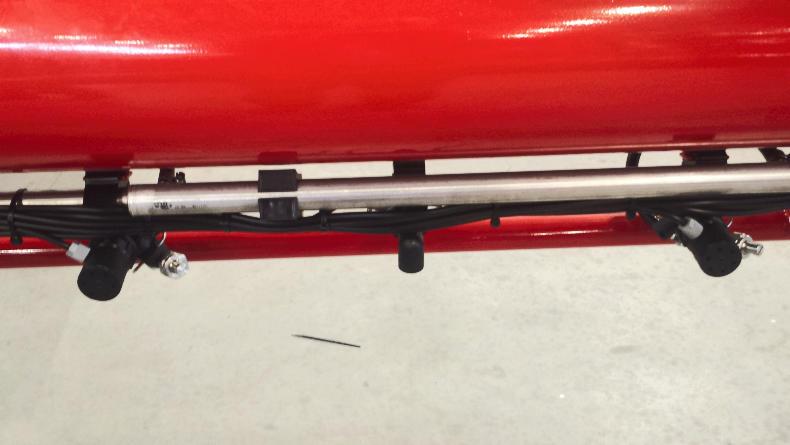
All the bigger booms tend to be fitted with ultrasonic height control linked into the hydraulics to help maintain correct spraying height. Each of the four wheels is driven by its own hydraulic motor. All wheels can steer and each can float independently of the others.
This suspension adds considerably to the stability of the boom to enable forward speeds that can go higher than 20mph in some countries.
All machines are built on a variable width chassis which can go out to 3m wide, a configuration which is desirable for farmers using controlled traffic.
Agrifac makes big and sophisticated self-propelled sprayers and sugar beet harvesters.Sprayer widths go out to 55m.Sophistication includes GPS controls and pulsing nozzles to control application rate.An app can be used to turn the boom on or off remotely using a smartphone. Read more
Vintage tractors: rumbling Renault is still rolling
Hi-Spec Engineering makes loss in 2016
A few months ago, I had occasion to make an unscheduled visit to Agrifac in a town called Steenwijk in northern Netherlands.
Some may know the name of this machinery manufacturer – most may not have heard of it before. Agrifac makes two major lines of machinery – beet harvesters and self-propelled sprayers. And what they make is big and sophisticated.
There were a few things that struck me in particular about the operation.
Firstly, they seem to make nothing, ie it seems to be an assembly plant for parts made elsewhere.
Secondly, they make big and sophisticated machinery with sprayers up to 55m boom width and beet harvesters up to 12 rows sitting on three hydraulically powered axles.
Each of the four wheels is driven by its own hydraulic motor
Interestingly, our guide said that this big 12-row beet harvester was produced initially many years ago but it gained no popularity at the time. It was relaunched a few years ago and has been selling very well since.
The comment was that the initial machine was ahead of its time but the arrival of much bigger tractor and trailer units on farms has now provided matching capacity for this big harvester as the units of 10 to 15 years ago were too small for its capacity.
Assembly only
The assembly plant produces sprayers for just over six months of the year and harvesters for about the same. As with most other manufacturers, units are made to order and they are highly personalised.
While all the individual components are outsourced, a spokesman for the company told me that they do not purchase on price. Virtually all parts are manufactured within a modest radius of the assembly plant.
“Attempting to source the cheapest components on price alone from either Eastern Europe or further afield might look better on the bottom line but downtime on any machine is highly significant for customers and could be very damaging to the reputation of the company,” the guide stated.
Most of the engines used are Iveco because these same engines are present in many tractors and in other farm machinery. So there will be local expertise in most areas of the world where these machines might be purchased. They also use Volvo engines in some of their bigger 350+hp units.
They source very high quality hydraulic and other components. If a machine broke down in a field in Ukraine or Russia it would take up to eight days to drive there with the parts for repair. So the main objective is not to have machines that will break down.
Because of the absolute necessity to avoid unintentional stoppages, all machines are fitted with a unit that communicates between the factory and each individual machine. This means that each machine is always remotely monitored and, in general, the factory will know of an impending breakage before the operator does and he will be told that by phone.
Sophisticated precision
All sprayers are fitted with GPS precision controls for operation and steering. Boom sizes go from 24m to 55m width. Asked if such big units were going to the open prairie lands of Australia or America, the answer was “not necessarily”.
“Some do, but many go to local farmers who are operating on expensive local rented land but the users of these big units are growing valuable crops. Expensive land and valuable crops generate a benefit from these big widths so as to minimise the number of tram tracks in a field.”
Sprayers can have different levels of sophistication but all are fitted with an independent suspension system that can be used to raise the height of the under-body above the crop to give a clearance of up to 2m.
The spraying system itself is a modified Airtec system which uses a combination of liquid and air to generate the required droplet size.
To facilitate variable rate (or reduced rate from a given/set application rate) they can use pulsing nozzles. These can be used to decrease the application volume on the move by adjusting their on/off time.
These sophisticated pulsing nozzles can turn off or on the spray liquid up to 100 times per second. So if every second pulse is off the spray volume in that patch could, say, drop from 100 l/ha to 50 l/ha. This means that the liquid pressure and droplet size are barely affected, even though rate has been decreased.
Two spray lines
Imagine having a 55m boom width and changing from one application volume to another for different crops or targets. This would mean changing/turning around 110 different nozzles – a job in itself. It would also be a 110m round trip from the cab.
In that part of the world, it would not be uncommon for a farmer to spray pesticides in morning when the wind is low and then switch to liquid fertiliser in the afternoon when wind speeds rise. Drift would not be an issue as this would be a much coarser spray using a very different nozzle.
To avoid having to alter every nozzle, the sprayer boom can be fitted with a second spray line and a specialised nozzle set. The second line has nozzles that are offset by 25cm.
Each of the two lines can then be turned off or on from the cab meaning virtually no lost time.
Blocked nozzles
Blocked nozzles are a very common problem in spraying. They mean turning off the boom; walking to clear the problem nozzle; back to the controls and boom-on again to re-check. This could take a lot of time if you got dirty water or a batch of crystallised spray.
To avoid the need to walk to and from the cab each time to turn the boom on and off, these sprayers can be fitted with a device which can be controlled using an app on a smartphone. Using this, the operator can turn the boom on and off to check nozzle blockage.
Sprayer units at the moderate end are priced between €250,000 and €300,000. Tank size can now go up to 8,000 litres and with huge technological sophistication available, prices can go much higher also.
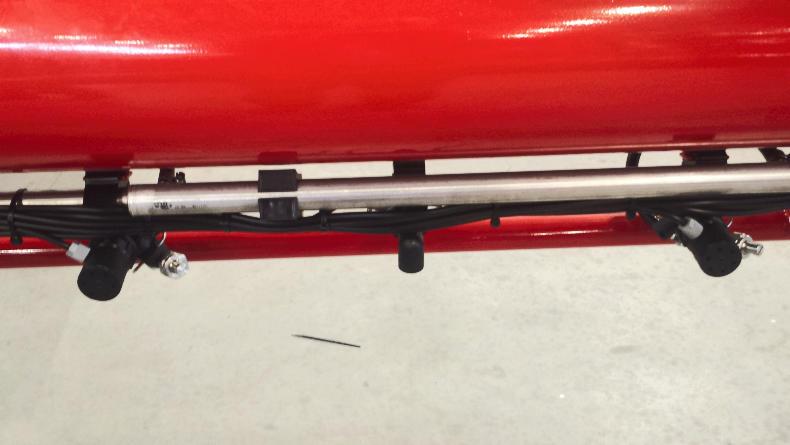
All the bigger booms tend to be fitted with ultrasonic height control linked into the hydraulics to help maintain correct spraying height. Each of the four wheels is driven by its own hydraulic motor. All wheels can steer and each can float independently of the others.
This suspension adds considerably to the stability of the boom to enable forward speeds that can go higher than 20mph in some countries.
All machines are built on a variable width chassis which can go out to 3m wide, a configuration which is desirable for farmers using controlled traffic.
Agrifac makes big and sophisticated self-propelled sprayers and sugar beet harvesters.Sprayer widths go out to 55m.Sophistication includes GPS controls and pulsing nozzles to control application rate.An app can be used to turn the boom on or off remotely using a smartphone. Read more
Vintage tractors: rumbling Renault is still rolling
Hi-Spec Engineering makes loss in 2016
SHARING OPTIONS: