The first AgXeed autonomous agricultural tractor has arrived on Irish soil.
The first unit was on display at the Kelly’s of Borris open days in Carlow last week.
This appearance officially marked the appointment of the well-known Claas dealership as the sole Irish importer and distributor of these Dutch built robots.
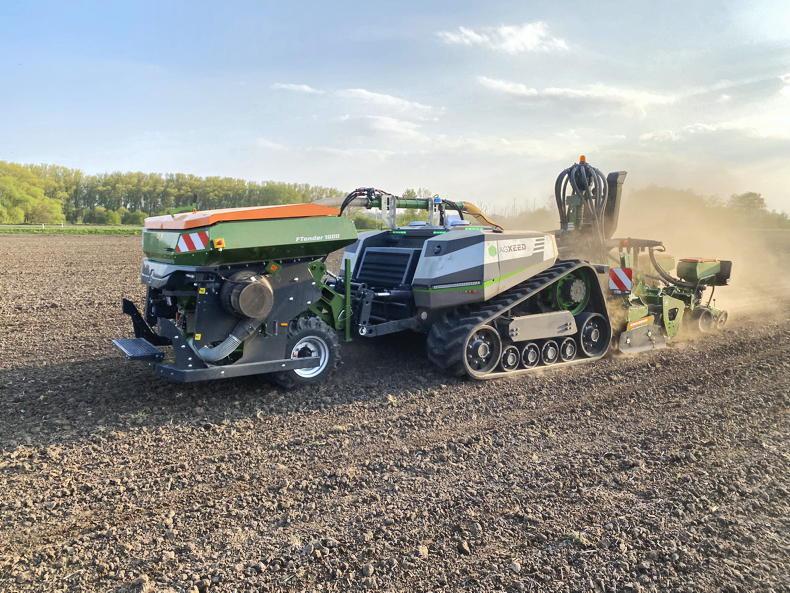
For obstacle detection, it uses lidar, ultrasonic, radar and contact sensors.
The robot
AgXeed has designed three models of autonomous field robots. With three models in the range, these come with diesel-electric drive and come on wheels or on tracks.
The machine on display was an AgBot 5.115T2. This is the flagship model, which is also the only tracked version.
It’s powered by a 4.1l four-cylinder 156hp Deutz engine, with a maximum torque of 610Nm. Power is transmitted from the engine to a generator and from there to electric drive motors. The electric drive train has a speed range from 0km/h to 13.5km/h.
With a 350l diesel tank and a 30l AdBlue tank, the manufacturer claims that the robot will typically run for 20 hours at 75% load on one tank of fuel. It claims efficiency is largely down to the electric drivetrain.
The hydraulic system is supplied by Bosch and offers a flow rate of 85l/min at 210bar. Meanwhile, up to four double-acting proportional spool valves and load-sensing hydraulics are available.
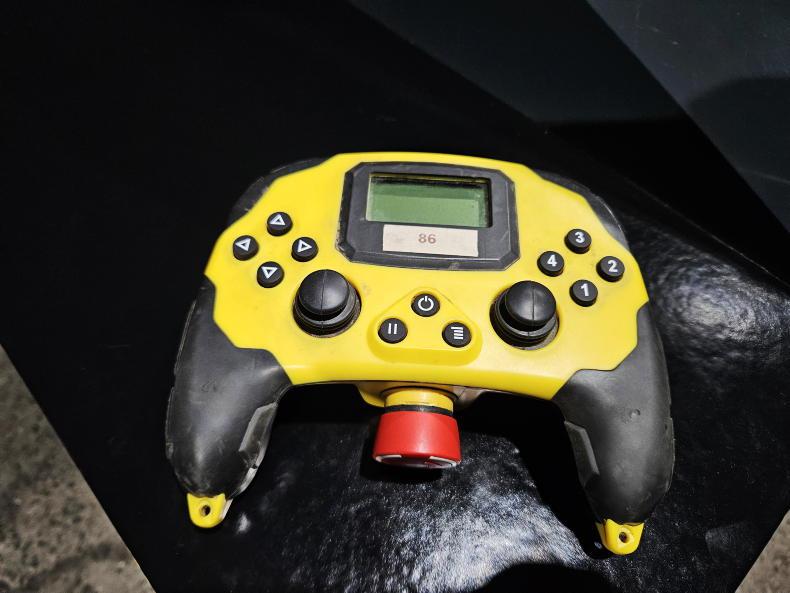
The operator can manually operate the robot through a remote control.
The unit weighs in at 7.8t (without ballast) and features an 8t rear linkage capacity, which is paired up with a 3t front linkage lift capacity.
Five different track belt widths are available, from 300mm to 910mm, while it also features an adjustable track width. The track width can be manually adjusted from its narrowest 1.8m out to 3.2m.
It offers a crop clearance of 42cm. An electric PTO, independent of the engine speed, and external high-voltage connections are available.
The 156hp tracked version was presented in 2020, followed by the 75hp three-wheeled AgBot 2.055W3 for orchards and vineyards in 2021, which was most recently joined by the four-wheeled 75hp AgBot 2.055W4.
The autonomy element
“To meet the regulations for unsupervised autonomy, the machines have to have four levels of sensors," explained AgXeed head of sales Peter Robinson.
"These include Lidar scanners on the top of the machine, radar sensors which are integrated into the safety bumper, ultrasonic sensors which are also integrated into the safety bumper and contact sensitive bumper which is also integrated into the safety bumper.
"This technology is used to detect obstacles and allow the tractor to carry out autonomous work without supervision. For successful autonomy, it requires three of the four to be working at any one time.
"Sometimes, direct harsh sunlight can affect the lidar, while heavy dust can kill the ultrasound.
"When the machine is operational, the safety bumper runs 15cm above the ground. If anything comes into contact with this, it will stop the machine dead and kill the power to the implement at the rear. The machines are strictly prohibited to be autonomously operated on roads. The units are fully insurable and meet all regulations,” he explained.
If the sensors detect an obstacle, the owner is sent a message on their phone. Cameras installed around the tractor allow the owner to see the entire surroundings of the tractor.
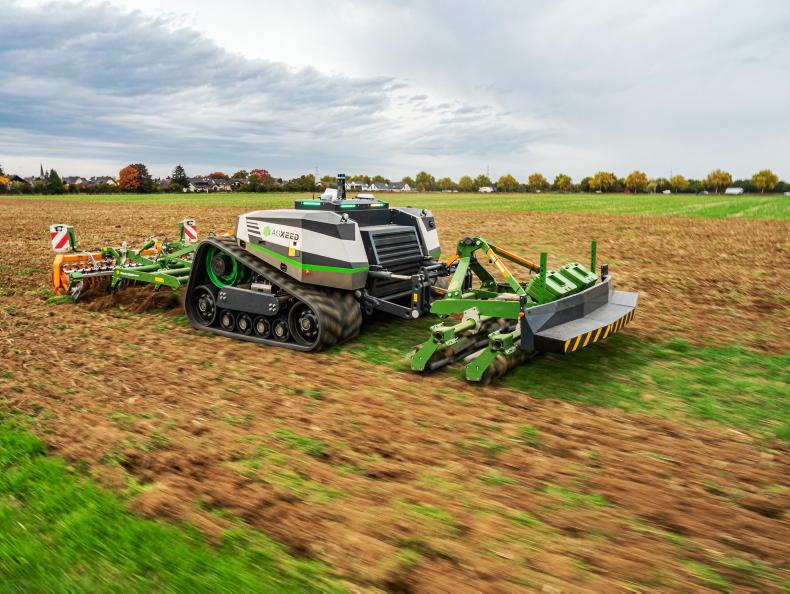
It in at 7.8t (without ballast) and features an 8t rear linkage capacity and a 3t front linkage lift capacity.
This means that if the robot is stopped by an obstacle, the farmer can tell it to proceed. If this isn’t possible, manual intervention would be required.
From a safety aspect, the unit operates within a prescribed geofenced area. It has visual indicator lights, an audible warning alarm and has emergency stop buttons around the machine.
The machines are operated through full GPS control, with this technology sourced from NovAtel. It’s equipped with a module for bidirectional data transfer and RTK GNSS for precise guidance, with positioning as accurate as +/-2.5cm.
Implements
One of the big advantages for AgXeed over other autonomous machines currently in the marketplace is that it can be paired with existing implements already used on the farm.
Coupling to an implement is done manually. The operator reverses the robot into line with the attachment through a remote control. Once the three-point linkage is attached, it’s just a matter of connecting the IsoBus plug, the PTO and the hydraulic hoses, etc.
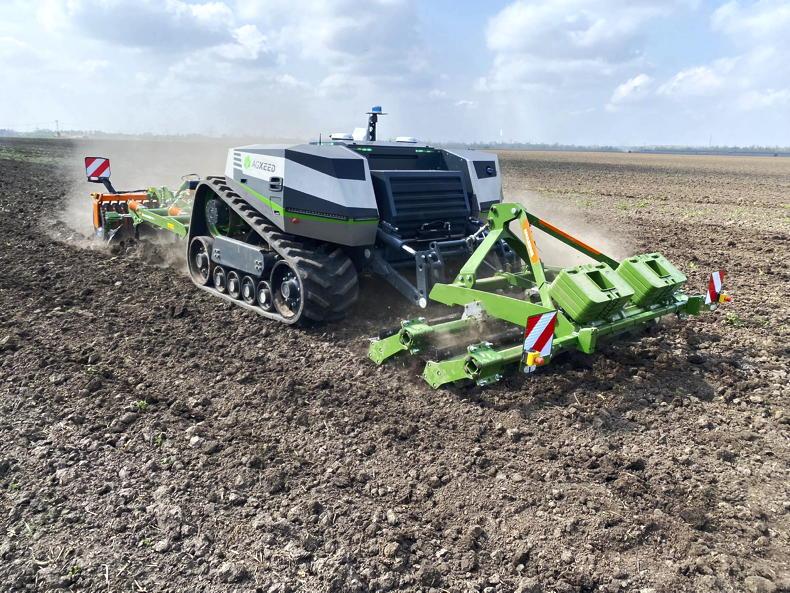
One big advantages for AgXeed over other autonomous machines is that it can be paired with existing implements already used on the farm.
For transport, the machine can be put on a low loader or it can be towed. The robot features two central tubes in the chassis where the farmer connects a drawbar and transport wheels to allow the unit to be towed. On arrival, the drawbar and wheels are folded out of the way.
Setting the AgBot up in the field
If you were to buy a machine, the first thing you would have to do is map all fields and log all implements on to the cloud system.
To create a job for the robot, the operator then needs to select the field on the online portal. This can be done via a computer or through an app.
From here, you must choose the intended AgBot-implement combinations and then define your desired process parameters, which include the working speed, the working depth or hydraulic control valve settings.
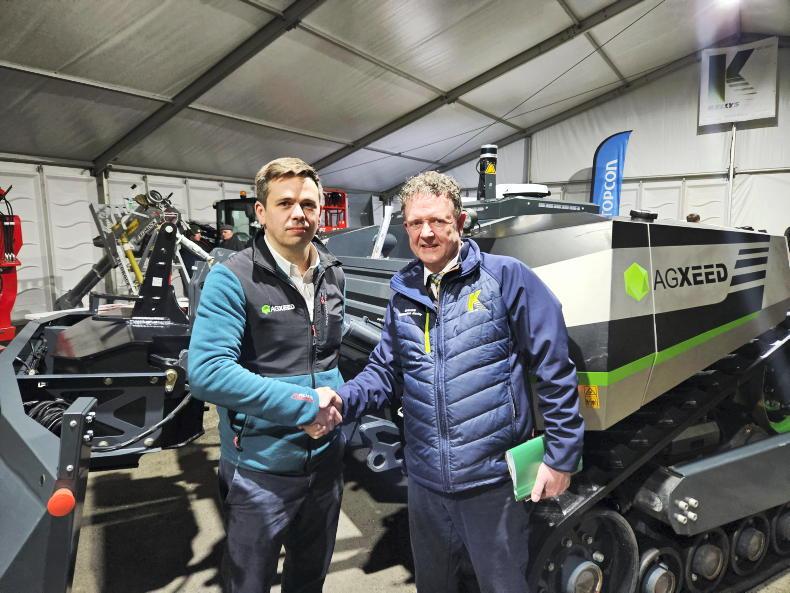
Kelly’s of Borris has been appointed as the sole Irish importer and distributor of the Dutch-built robots.
After this, you choose your desired reference A-B line and then the portal takes over and automatically creates the whole routing and task. The owner has full visibility to monitor the running process from his/her phone/computer.
Who are AgXeed?
AgXeed is a young Dutch company, which is carrying a wealth of knowledge. The start-up only came into existence in 2018, but its four co-founders are steeped in engineering.
Its founders are all ex-Fendt employees, who were based at the Rogator sprayer factory in Holland. When Fendt made the decision to move the Rogator sprayer production to its Katana self-propelled forager factory in Germany, not all staff were willing to up-ship and move.
Over a beer at a barbecue, the four co-workers decided they would try to design and build their own project. The project started in the summer of 2018 in an old chicken house on a nearby farm.
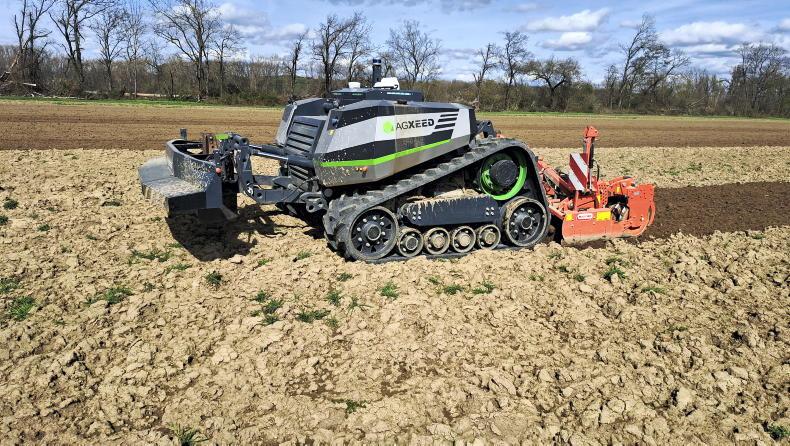
Five track belt widths are available, from 300mm to 910mm, and it also features an adjustable track width.
In December 2019 - 20 months later - the team rolled out its first fully functional prototype. This was followed by two years of testing, before the project was commercially ready for sale in 2022.
The company has grown rapidly and now has 50 staff. To meet production demands, AgXeed last month moved into the old Fendt Rogator sprayer factory, which I’m sure holds much sentimental value for its four co-founders.
Over the last number of years, Claas and Amazone have both heavily invested into the business, but it remains majority owned by the co-founders.
How many machines are in the fields?
The company has built and delivered a total of 80 machines so far, with an additional 115 machines currently on its order book.
The Netherlands and Germany both account for 20 units each, with 15 in France and units in Canada, Switzerland, Australia, New Zealand and others.
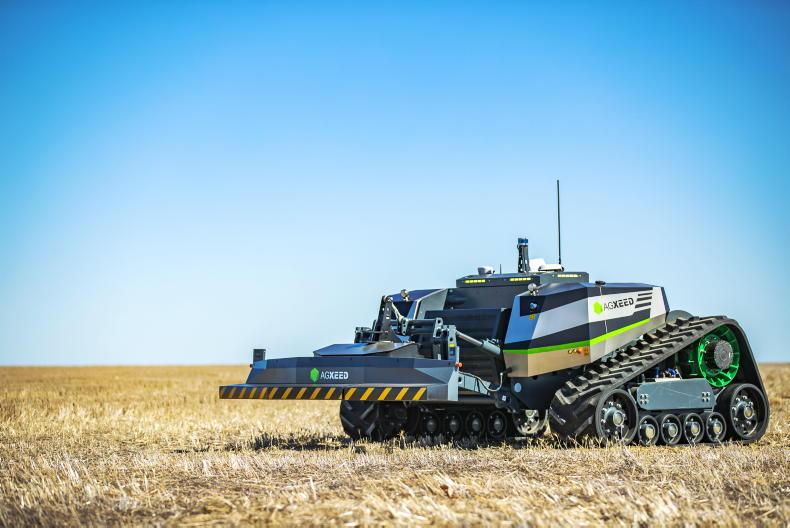
The company has built and delivered a total of 80 machines so far, with an additional 115 machines currently on its order book.
A total of four machines were sold into England last year. AgXeed have three customers running two machines each, with all having a third machine on order.
These machines are being used for a whole range of tasks including ploughing, cultivating, power harrowing, sowing, mowing and mulching.
Have they a role to play in Irish agriculture?
From an Irish context, the big question everyone will ask is whether there is a place for these machines in our market, where we have such an unstable weather climate, small fields and hugely varying soil types?
“We have four demos lined up in Ireland and we expect two sales this year for the larger tracked machine. These will typically be on 800-plus acres farms, growing specialist fruit and vegetables. While machines are able to run to 13km/h, it is where slow applications are needed that the return on investment comes," said Peter.
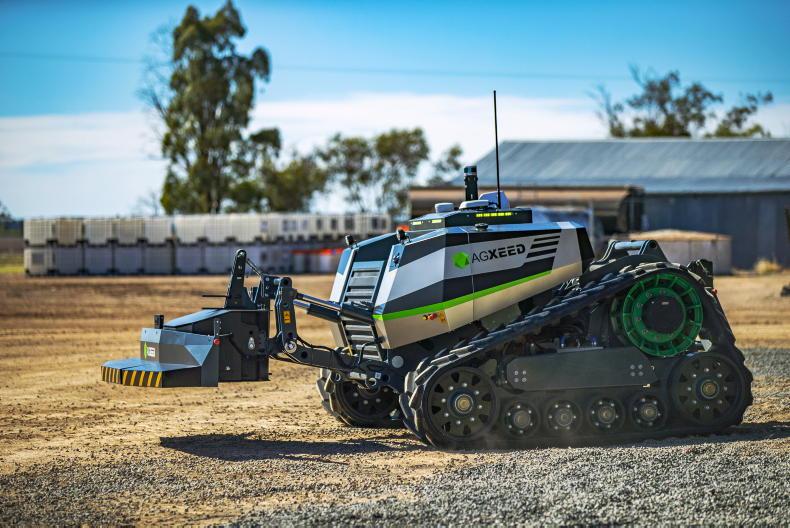
The electric drive train has a speed range from 0-13.5km/h.
"Upcoming years I would expect sales of the tracked machine to be around five units per year, but it is the 75hp wheeled version which will be better suited for the Irish market.
"The price is far more attractive for handling 3m implements and we have a successor due next year which will offer more power,” explained Peter.
50% grant aid available in England
A new and recently announced grant titled ‘Improving Farm Productivity’ is open to farmers in England. This grant provides up to 50% of the cost of farm robotic and automated equipment investments, including this autonomous tractor.
Interestingly, the minimum grant available is £25,000 and the maximum grant available is £500,000.
“There is a pot of £45m available under the new grant. AgXeed are expecting 60 grant applications to be submitted very shortly.
"The machines are priced at £300,000 plus VAT, which works out at around £2,000/hp, which is double the price of a conventional tractor,” explained Peter.
Model: AgXeed AgBot 5.115T2.Engine: 156hp Deutz 4.1-litre, four-cylinder diesel. Electric PTO: 136hp electric driveline. Electric forward speed: 0.1 to 13.5 km/h.Hydraulics: 85l/min. Linkage capacity: 8t rear, 3t front. Width of tracks: five options (300mm to 910mm). Track width: Variable 1.8m to 3.2m. Crop clearance: 42cm.Weight: 7.8t. Sensors: Lidar, ultrasound. Price: €320,000 plus VAT.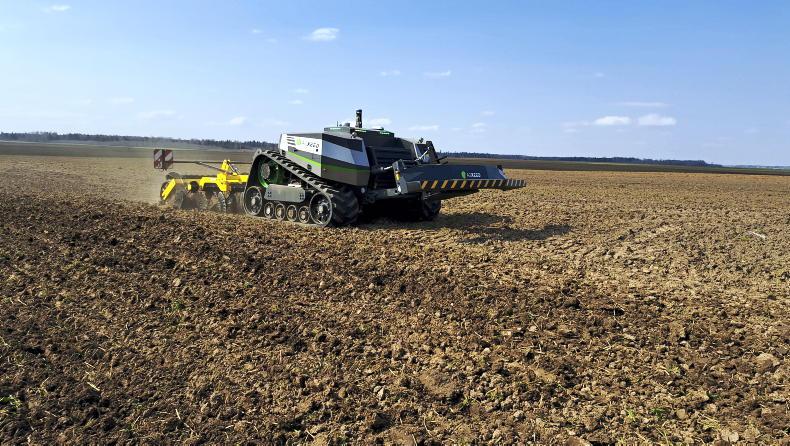
The machines are priced at €320,000 plus VAT.
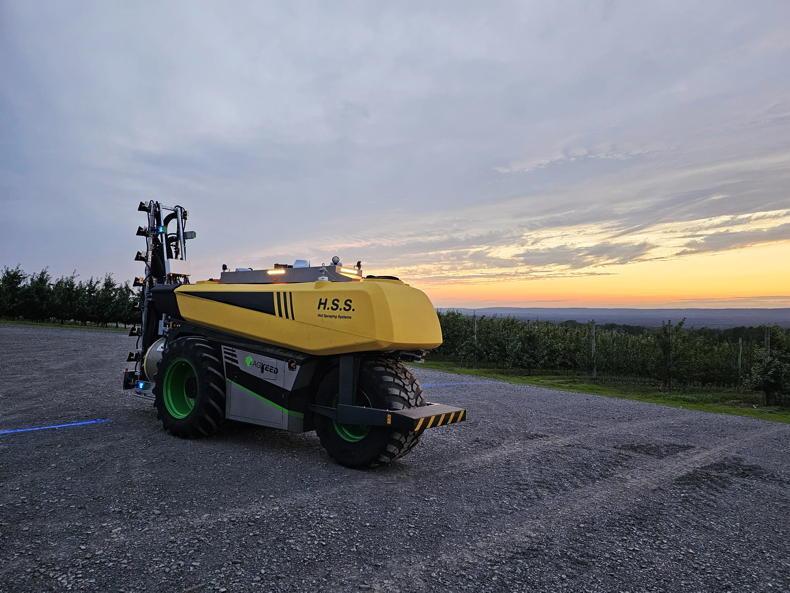
With three models in the range, these come with diesel-electric drive and come on wheels or on tracks.
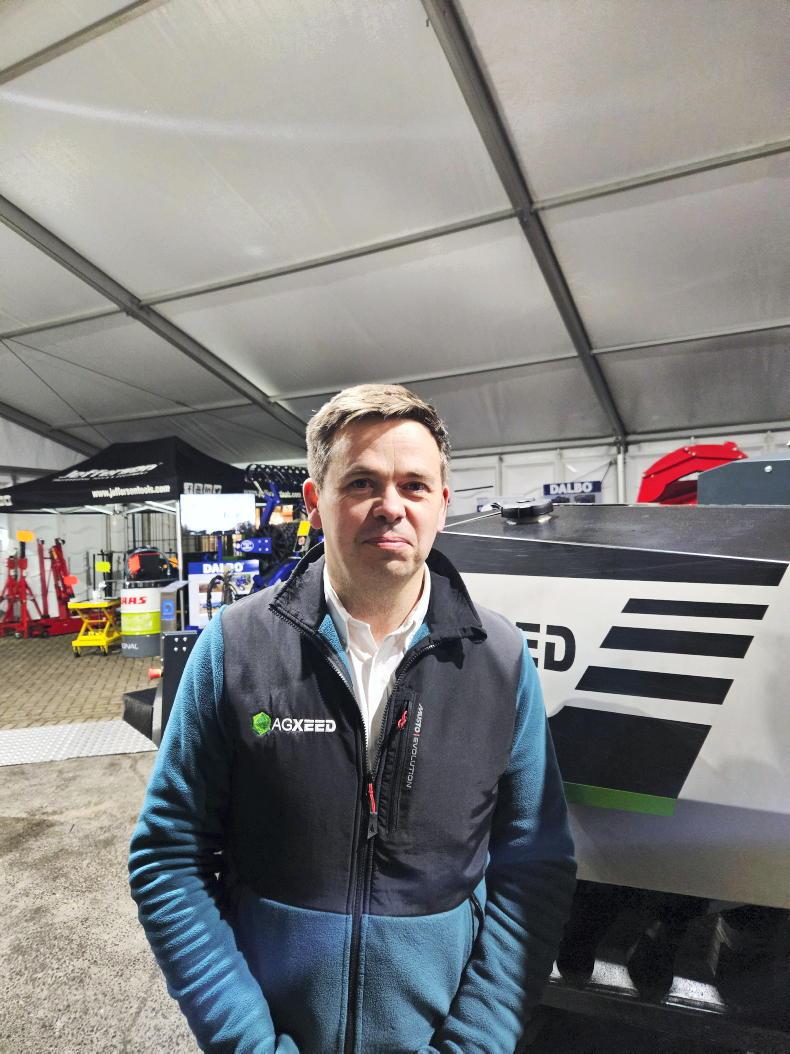
Peter Robinson.
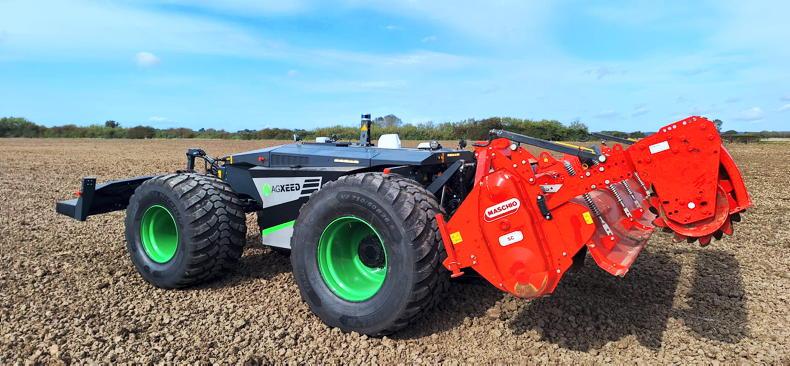
The hydraulic system is supplied by Bosch, and offers a flow rate of 85l/min at 210bar.
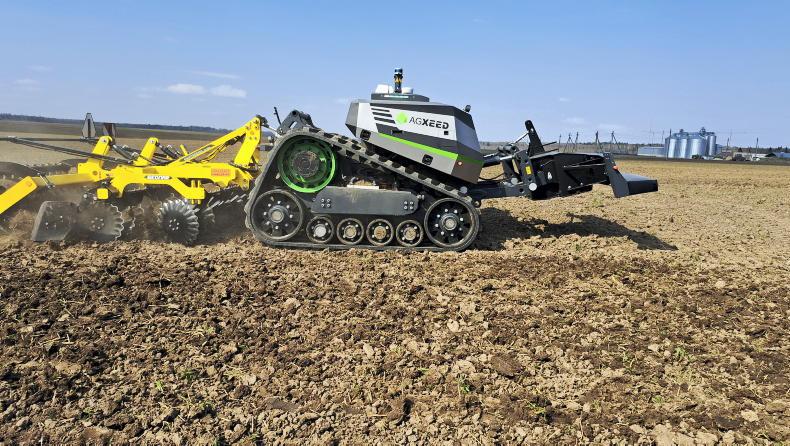
Power is transmitted from the engine to a generator and from there to electric drive motors.
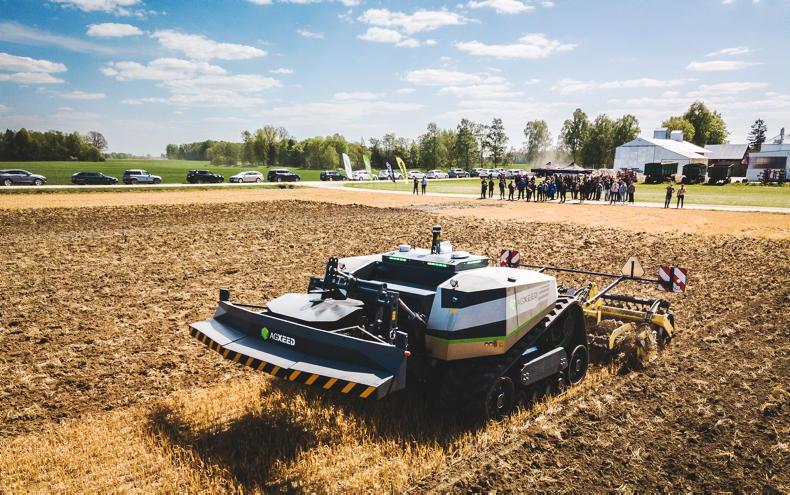
With a 350l diesel tank and a 30l AdBlue tank, the manufacturer claims that the robot will typically run for 20 hours at 75% load on one tank of fuel.
The first AgXeed autonomous agricultural tractor has arrived on Irish soil.
The first unit was on display at the Kelly’s of Borris open days in Carlow last week.
This appearance officially marked the appointment of the well-known Claas dealership as the sole Irish importer and distributor of these Dutch built robots.
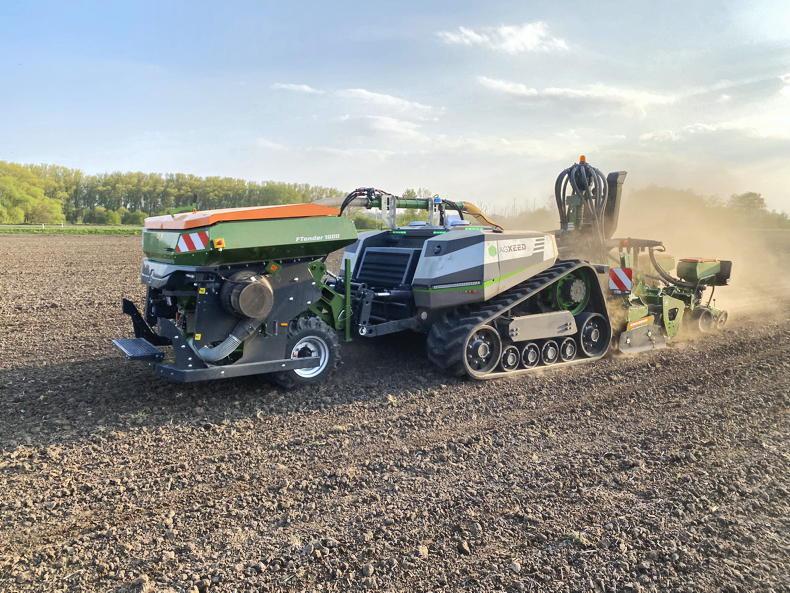
For obstacle detection, it uses lidar, ultrasonic, radar and contact sensors.
The robot
AgXeed has designed three models of autonomous field robots. With three models in the range, these come with diesel-electric drive and come on wheels or on tracks.
The machine on display was an AgBot 5.115T2. This is the flagship model, which is also the only tracked version.
It’s powered by a 4.1l four-cylinder 156hp Deutz engine, with a maximum torque of 610Nm. Power is transmitted from the engine to a generator and from there to electric drive motors. The electric drive train has a speed range from 0km/h to 13.5km/h.
With a 350l diesel tank and a 30l AdBlue tank, the manufacturer claims that the robot will typically run for 20 hours at 75% load on one tank of fuel. It claims efficiency is largely down to the electric drivetrain.
The hydraulic system is supplied by Bosch and offers a flow rate of 85l/min at 210bar. Meanwhile, up to four double-acting proportional spool valves and load-sensing hydraulics are available.
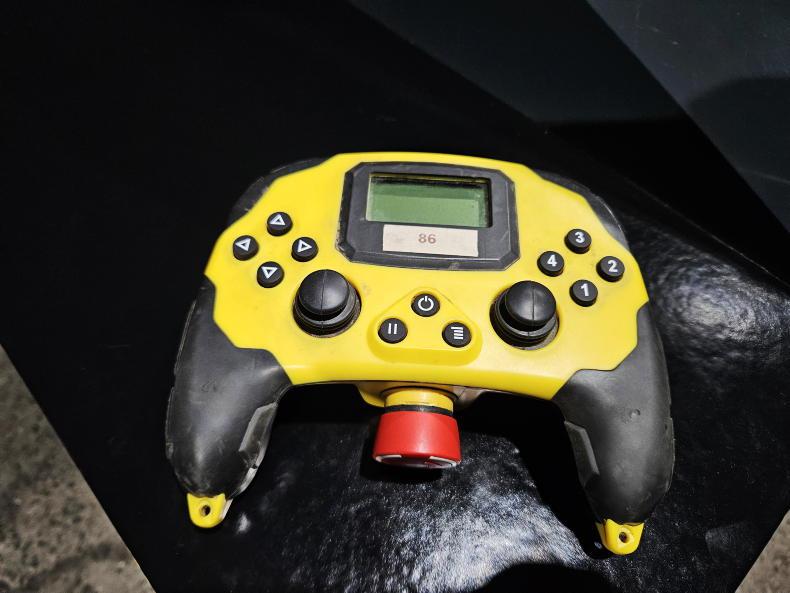
The operator can manually operate the robot through a remote control.
The unit weighs in at 7.8t (without ballast) and features an 8t rear linkage capacity, which is paired up with a 3t front linkage lift capacity.
Five different track belt widths are available, from 300mm to 910mm, while it also features an adjustable track width. The track width can be manually adjusted from its narrowest 1.8m out to 3.2m.
It offers a crop clearance of 42cm. An electric PTO, independent of the engine speed, and external high-voltage connections are available.
The 156hp tracked version was presented in 2020, followed by the 75hp three-wheeled AgBot 2.055W3 for orchards and vineyards in 2021, which was most recently joined by the four-wheeled 75hp AgBot 2.055W4.
The autonomy element
“To meet the regulations for unsupervised autonomy, the machines have to have four levels of sensors," explained AgXeed head of sales Peter Robinson.
"These include Lidar scanners on the top of the machine, radar sensors which are integrated into the safety bumper, ultrasonic sensors which are also integrated into the safety bumper and contact sensitive bumper which is also integrated into the safety bumper.
"This technology is used to detect obstacles and allow the tractor to carry out autonomous work without supervision. For successful autonomy, it requires three of the four to be working at any one time.
"Sometimes, direct harsh sunlight can affect the lidar, while heavy dust can kill the ultrasound.
"When the machine is operational, the safety bumper runs 15cm above the ground. If anything comes into contact with this, it will stop the machine dead and kill the power to the implement at the rear. The machines are strictly prohibited to be autonomously operated on roads. The units are fully insurable and meet all regulations,” he explained.
If the sensors detect an obstacle, the owner is sent a message on their phone. Cameras installed around the tractor allow the owner to see the entire surroundings of the tractor.
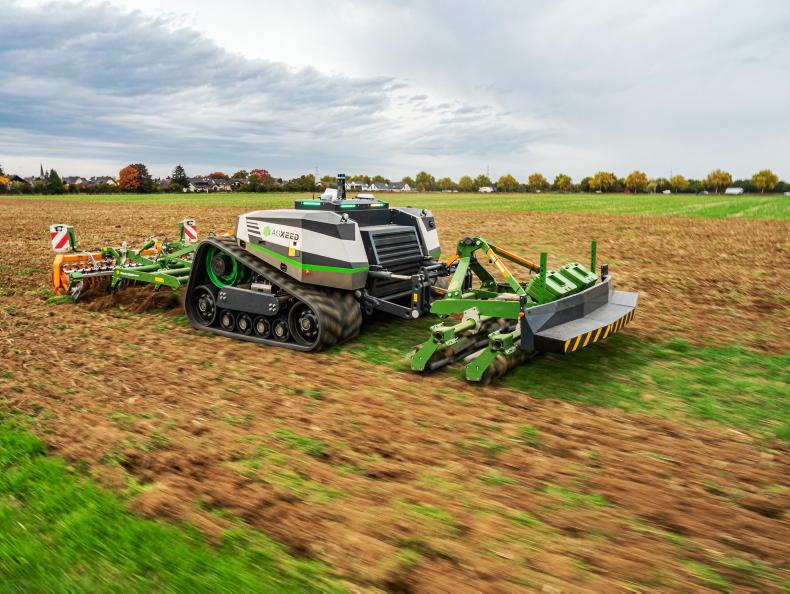
It in at 7.8t (without ballast) and features an 8t rear linkage capacity and a 3t front linkage lift capacity.
This means that if the robot is stopped by an obstacle, the farmer can tell it to proceed. If this isn’t possible, manual intervention would be required.
From a safety aspect, the unit operates within a prescribed geofenced area. It has visual indicator lights, an audible warning alarm and has emergency stop buttons around the machine.
The machines are operated through full GPS control, with this technology sourced from NovAtel. It’s equipped with a module for bidirectional data transfer and RTK GNSS for precise guidance, with positioning as accurate as +/-2.5cm.
Implements
One of the big advantages for AgXeed over other autonomous machines currently in the marketplace is that it can be paired with existing implements already used on the farm.
Coupling to an implement is done manually. The operator reverses the robot into line with the attachment through a remote control. Once the three-point linkage is attached, it’s just a matter of connecting the IsoBus plug, the PTO and the hydraulic hoses, etc.
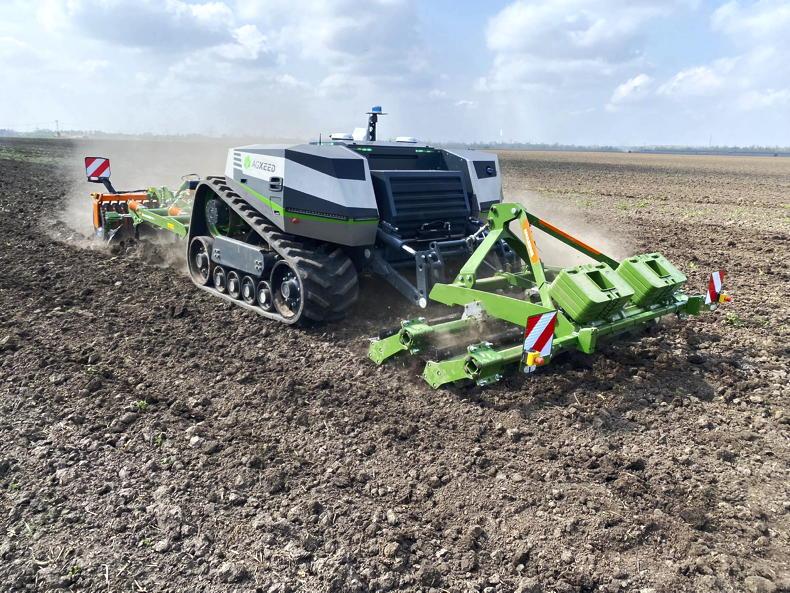
One big advantages for AgXeed over other autonomous machines is that it can be paired with existing implements already used on the farm.
For transport, the machine can be put on a low loader or it can be towed. The robot features two central tubes in the chassis where the farmer connects a drawbar and transport wheels to allow the unit to be towed. On arrival, the drawbar and wheels are folded out of the way.
Setting the AgBot up in the field
If you were to buy a machine, the first thing you would have to do is map all fields and log all implements on to the cloud system.
To create a job for the robot, the operator then needs to select the field on the online portal. This can be done via a computer or through an app.
From here, you must choose the intended AgBot-implement combinations and then define your desired process parameters, which include the working speed, the working depth or hydraulic control valve settings.
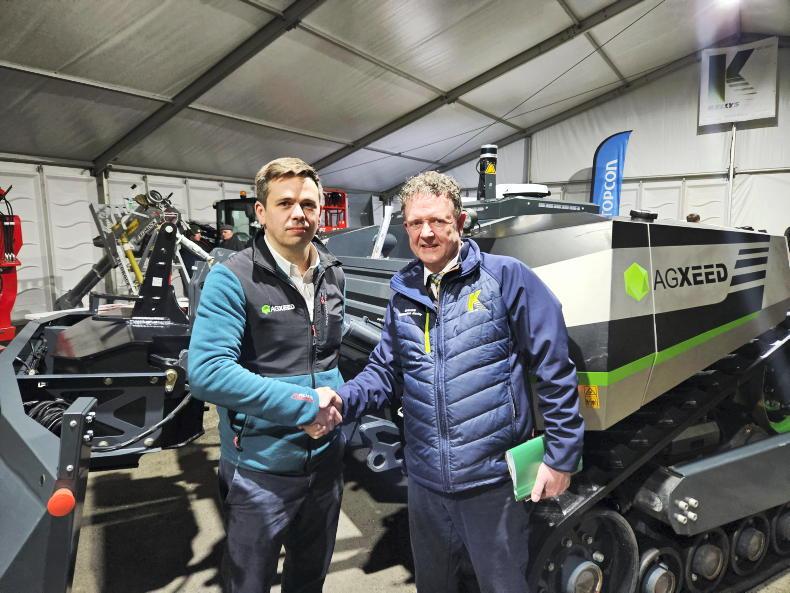
Kelly’s of Borris has been appointed as the sole Irish importer and distributor of the Dutch-built robots.
After this, you choose your desired reference A-B line and then the portal takes over and automatically creates the whole routing and task. The owner has full visibility to monitor the running process from his/her phone/computer.
Who are AgXeed?
AgXeed is a young Dutch company, which is carrying a wealth of knowledge. The start-up only came into existence in 2018, but its four co-founders are steeped in engineering.
Its founders are all ex-Fendt employees, who were based at the Rogator sprayer factory in Holland. When Fendt made the decision to move the Rogator sprayer production to its Katana self-propelled forager factory in Germany, not all staff were willing to up-ship and move.
Over a beer at a barbecue, the four co-workers decided they would try to design and build their own project. The project started in the summer of 2018 in an old chicken house on a nearby farm.
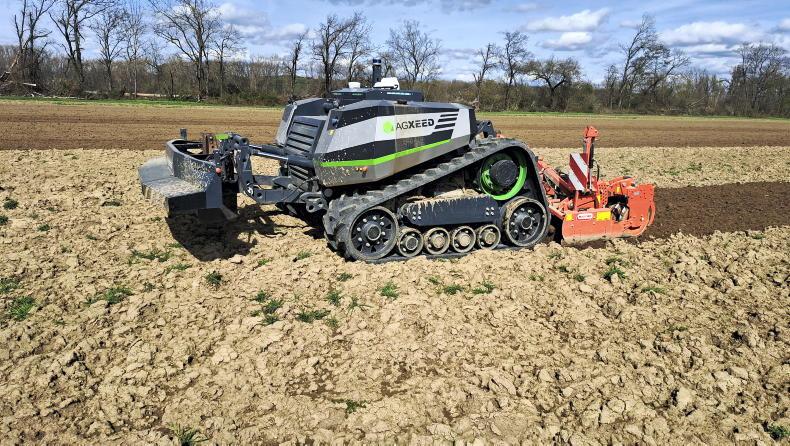
Five track belt widths are available, from 300mm to 910mm, and it also features an adjustable track width.
In December 2019 - 20 months later - the team rolled out its first fully functional prototype. This was followed by two years of testing, before the project was commercially ready for sale in 2022.
The company has grown rapidly and now has 50 staff. To meet production demands, AgXeed last month moved into the old Fendt Rogator sprayer factory, which I’m sure holds much sentimental value for its four co-founders.
Over the last number of years, Claas and Amazone have both heavily invested into the business, but it remains majority owned by the co-founders.
How many machines are in the fields?
The company has built and delivered a total of 80 machines so far, with an additional 115 machines currently on its order book.
The Netherlands and Germany both account for 20 units each, with 15 in France and units in Canada, Switzerland, Australia, New Zealand and others.
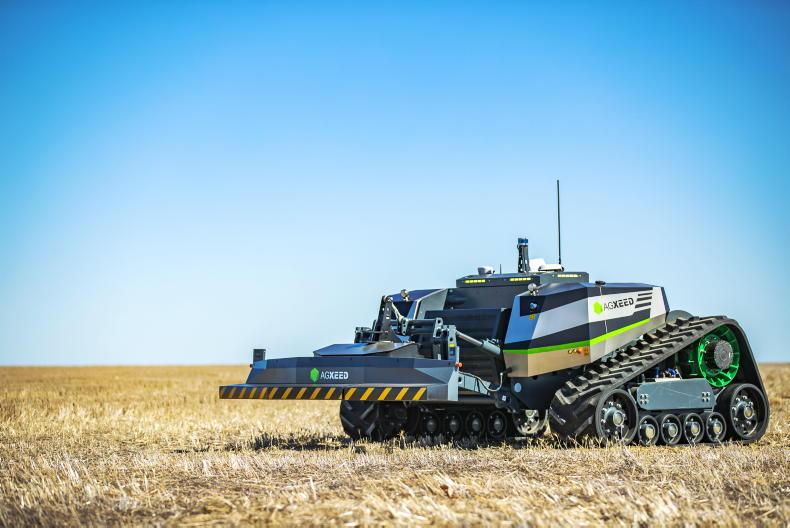
The company has built and delivered a total of 80 machines so far, with an additional 115 machines currently on its order book.
A total of four machines were sold into England last year. AgXeed have three customers running two machines each, with all having a third machine on order.
These machines are being used for a whole range of tasks including ploughing, cultivating, power harrowing, sowing, mowing and mulching.
Have they a role to play in Irish agriculture?
From an Irish context, the big question everyone will ask is whether there is a place for these machines in our market, where we have such an unstable weather climate, small fields and hugely varying soil types?
“We have four demos lined up in Ireland and we expect two sales this year for the larger tracked machine. These will typically be on 800-plus acres farms, growing specialist fruit and vegetables. While machines are able to run to 13km/h, it is where slow applications are needed that the return on investment comes," said Peter.
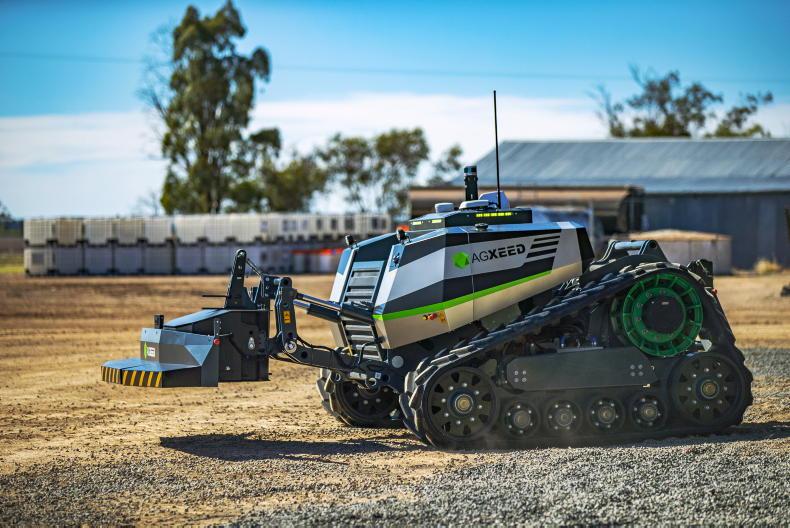
The electric drive train has a speed range from 0-13.5km/h.
"Upcoming years I would expect sales of the tracked machine to be around five units per year, but it is the 75hp wheeled version which will be better suited for the Irish market.
"The price is far more attractive for handling 3m implements and we have a successor due next year which will offer more power,” explained Peter.
50% grant aid available in England
A new and recently announced grant titled ‘Improving Farm Productivity’ is open to farmers in England. This grant provides up to 50% of the cost of farm robotic and automated equipment investments, including this autonomous tractor.
Interestingly, the minimum grant available is £25,000 and the maximum grant available is £500,000.
“There is a pot of £45m available under the new grant. AgXeed are expecting 60 grant applications to be submitted very shortly.
"The machines are priced at £300,000 plus VAT, which works out at around £2,000/hp, which is double the price of a conventional tractor,” explained Peter.
Model: AgXeed AgBot 5.115T2.Engine: 156hp Deutz 4.1-litre, four-cylinder diesel. Electric PTO: 136hp electric driveline. Electric forward speed: 0.1 to 13.5 km/h.Hydraulics: 85l/min. Linkage capacity: 8t rear, 3t front. Width of tracks: five options (300mm to 910mm). Track width: Variable 1.8m to 3.2m. Crop clearance: 42cm.Weight: 7.8t. Sensors: Lidar, ultrasound. Price: €320,000 plus VAT.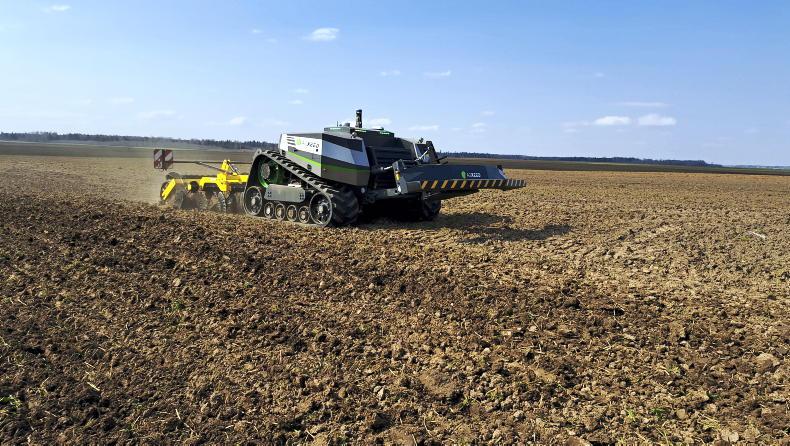
The machines are priced at €320,000 plus VAT.
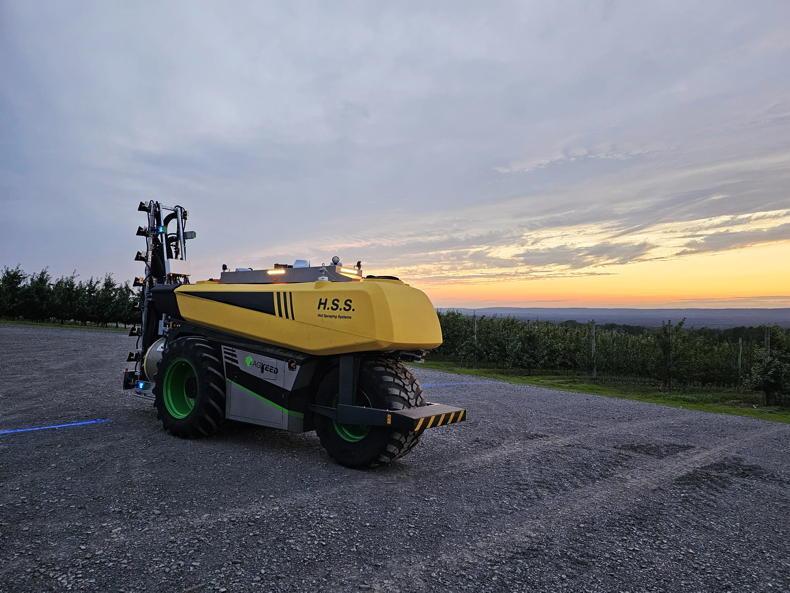
With three models in the range, these come with diesel-electric drive and come on wheels or on tracks.
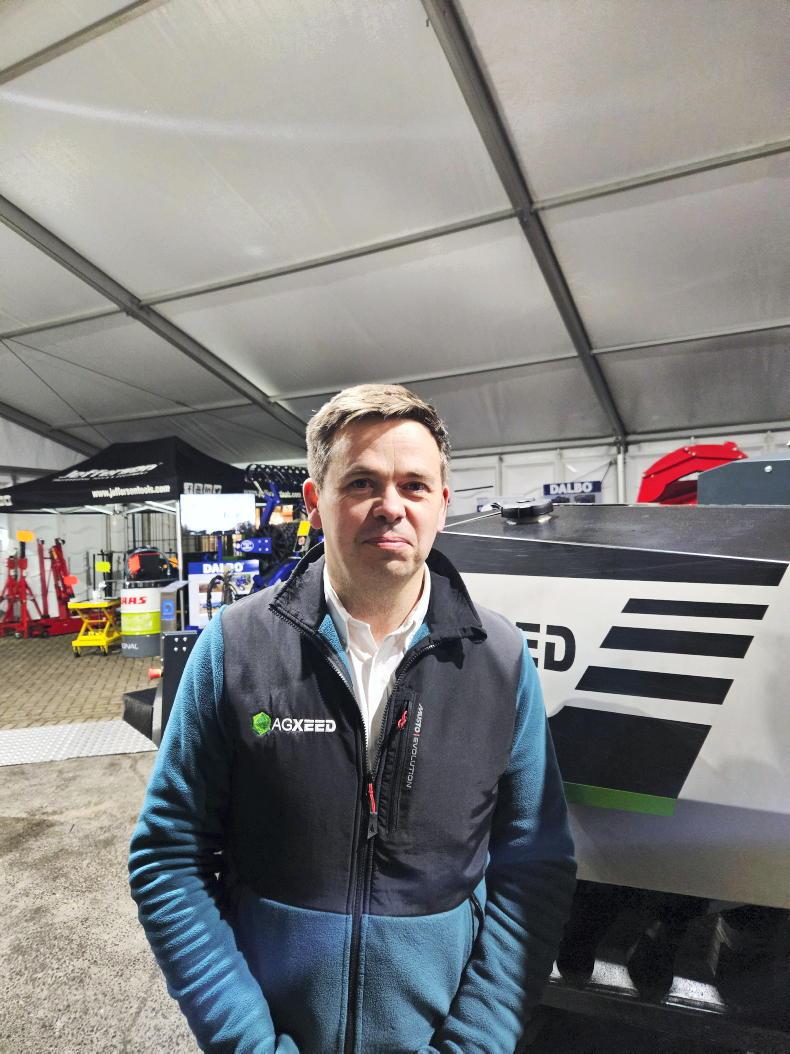
Peter Robinson.
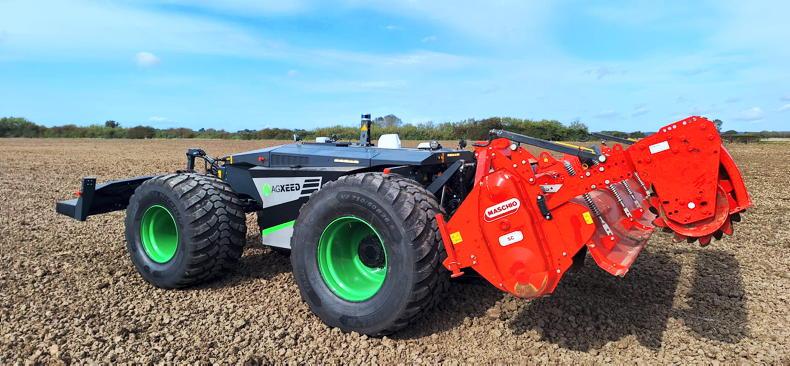
The hydraulic system is supplied by Bosch, and offers a flow rate of 85l/min at 210bar.
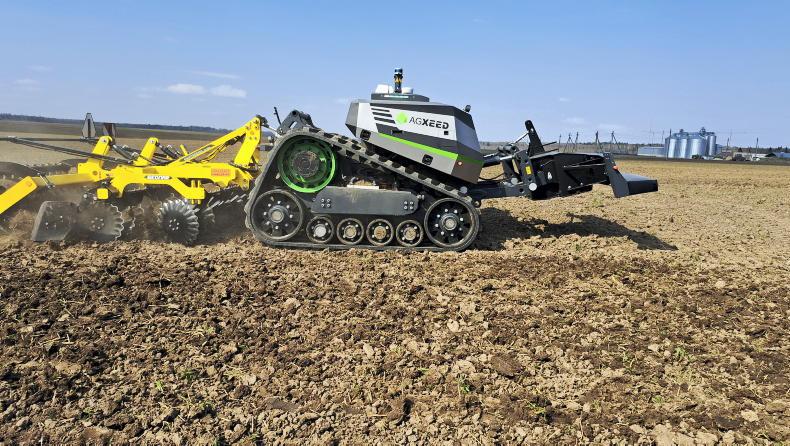
Power is transmitted from the engine to a generator and from there to electric drive motors.
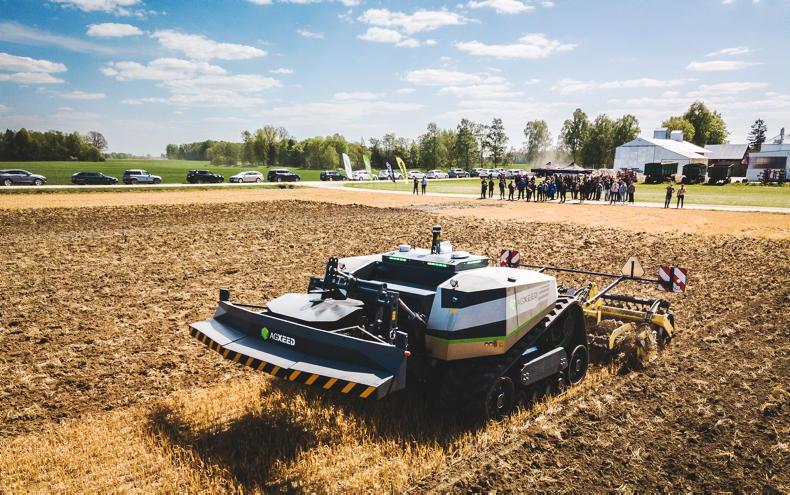
With a 350l diesel tank and a 30l AdBlue tank, the manufacturer claims that the robot will typically run for 20 hours at 75% load on one tank of fuel.
SHARING OPTIONS: