Farming more than 2,750 acres in Navan, Co Meath, the Smith family was one of two Irish potato growers to buy one of the new trailed two-row Dewulf planters ahead of the 2019 season. One year on and Andrew explained that they have been very impressed with the Dutch-built machine.
Why Dewulf?
Previously running a two-row Miedema mounted planter, the Smiths liked the reliability of the machine. Although they bought a new Dewulf planter, some of our readers will be aware that in November 2014, the Belgian company Dewulf and the Dutch company Miedema signed an acquisition agreement.
The family looked elsewhere in the market, but felt that the Dewulf planter was the best all-round and most competitively priced machine for their business. A big factor was the quality of bed it produced.
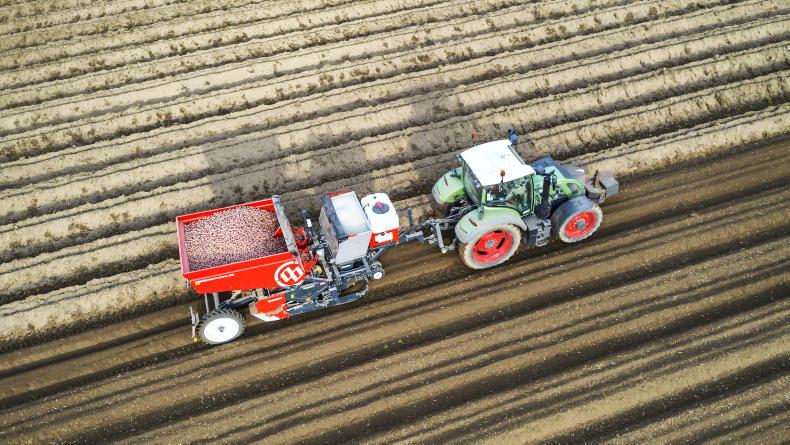
A huge plus for Andrew was the fact the sprayer and fertiliser dispensing rates are infinitely adjustable and will automatically reset to the desired rate based on the tractor's forward speed.
Picture: Adrian Leech Photography
Andrew acknowledged that moving from a 2005 planter to a new machine last year brought about huge technological advances and increases in efficiencies, which will go a long way towards helping pay for the new machine.
Mounted v trailed
Andrew noted that moving from a mounted to a trailed machine hindered manoeuvrability, as it’s much longer. However, once he got used to the trailed machine, this wasn’t an issue. The move to the trailed planter also improved visibility.
The big reason they moved to a trailed machine was to carry more seed potatoes and more fertiliser. Andrew noted that the trailed machine is capable of carrying one tonne of fertiliser and two to three tonnes of seed, a step up from the mounted planter, which only had capacity for 500kg of fertiliser and 1,200kg of seed.

The big reason the Smiths moved to a trailed machine was to carry more seed potatoes and more fertiliser. \Adrian Leech Photography
With an emphasis on efficiency, Andrew tries to operate and load the planter by himself. The fact that he has more than doubled his input-carrying capacity means that he has halved the time the planter is idle, waiting to be loaded.
Depending on the seeding rate, Andrew felt that he can now save at least 10 to 15 minutes every hour. This means he is able to keep up with the two Grimme CS150 de-stoners working ahead of him.
Another advantage to the new machine is the simplicity of detaching it from the tractor in the event of an issue.
“With our older mounted planter, if for some reason we had to change the tractor, it created a lot of hassle. With the trailed machine, everything is much more fluent and easier,” Andrew said.
How it works
The Dewulf MS2000 is a structural belt planter. Its planting system is designed to limit friction between the tubers, preventing damage to the seed potato.
A supply conveyor brings the seed potatoes from the hopper on to the wide belt bed with planting belts and returning belts.
Each row has six planting belts which bring the potatoes to the foam roller. The vibrating chute below the planting belts takes care of the singling and the excess potatoes are taken back to the rear board by the returning belts.
The belt bed is shaped so that each returning belt runs a little faster than the one next to it, which is beneficial in terms of filling of the belt bed.
On the last stretch of the planting belts, the potatoes are slowed down by the slightly slower running foam rubber roller. This speed reduction has a slight damming effect that presses the potatoes tightly against one another.
The position of the foam roller allows the potatoes to fall vertically into the furrow.
The V-shaped furrow opener is equipped with a small chisel that makes a sharp furrow. Dewulf claims that the loose soil created at the bottom prevents the seed potato from rolling. The shape of the furrow opener also crumbles a small amount of loose soil on top, which clamps the tuber in the furrow. The planting depth is set by means of the large depth control wheels mounted on the opener beam, on which the furrow openers are also mounted.
The parallelogram suspension is responsible for the constant planting depth, even across the width of the machine.
Features
One feature that has impressed Andrew is known as hill-master. On his previous planter, Andrew regularly encountered problems with seed flow when working up and down hills.
When planting downhill, the older machine had a tendency to double-plant, allowing extra seed potatoes to be planted due to the flow of gravity. When planting uphill, the opposite would happen. However, automatic hydraulic adjustment on his new machine ensures the belt bed is filled optimally. It helps to take stress off the operator, while saving seed.
Another feature Andrew noted he couldn’t be without is the tipping automat. “The hopper will tilt itself up and down as required to ensure the supply belts are always fed with a sufficient quantity of seed potatoes. This function works automatically and will recognise when coming to a headland, so there’s no waste. On my previous planter, this was manually operated through a spool valve. The automation helps to remove any operator error, also making it easier on the driver,” outlined Andrew.
Andrew was impressed with the MR-control system, which automatically adjusts the machine to help create a uniform ridge. Through this feature, sensors continuously measure the quantity of loose soil in the ridging hood, rather than pressure in the hydraulic cylinders. If needs be, the position of the ridging hood is automatically adjusted.
Technology
A huge plus for Andrew was the fact that the sprayer and fertiliser dispensing rates are infinitely adjustable and will automatically reset to the desired rate based on the tractor’s forward speed.
Another improvement on his previous machine is the way in which the fertiliser is placed between large discs located 5cm (2in) to the right and left of the seed potato.
His previous system wasn’t as accurate and Andrew feels the tubers will now get a better start, contributing to an overall greater yield come harvesting.
Andrew operates the planter on his 2016 Fendt 724. Although he didn’t spec the tractor with auto-steer at the time, he has noted his next tractor will be equipped with full real-time kinematic (RTK). Instead, he uses a T-jet system, the same as what he uses on his Bogballe fertiliser spreader.
The GPS co-ordinates of the field are collected by driving around the headlands. Once the field map is set up, this system controls the machine’s section control, the auto knock-on and -off of the rows. As it’s a two-row planter, it has two sections. Andrew said that he only got the section control up and running properly this year, but has noted significant cost savings.
“Our old machine was ground-drive. With this, we had wastage in two ways. Firstly, when we lifted the planter at the headlands, the wheel would keep turning and seed would continue to come out. Secondly, we would always be inclined to sow a little extra where the headland met the run to ensure enough seed is set. It’s difficult to quantify the exact savings, but at €600/t for certified Rooster seed, I can often see half a tonne being saved in most fields,” explained Andrew.
In the cab, the control layout is quite simple. Andrew has four cameras linked to one screen while all the planting statistics are displayed on the operating terminal.

Andrew has four cameras linked to one screen while all the planting statistics are displayed on the operating terminal.
It’s straightforward to connect a GPS signal from the tractor or standalone system to the planter’s control system.
When we spoke with Andrew, he was almost finished up on his second planting season with the machine.
He noted that the planter is user-friendly – so much so that an inexperienced operator could pilot the machine. He only highlighted two faults.
Firstly, he was disappointed that it didn’t come with a hopper cover.
To overcome this, he retrofitted a cover he designed himself.
Secondly, he felt that the discs where the fertiliser is applied have trouble working in wet conditions.
Technological advances
Although he didn’t go for a wider planting width, he’s been more than impressed with the technological advances and increased efficiencies, which have helped him to increase his output to between 8ha and 10ha per day (20 to 25 acres).
He added that the team at Quaile Machinery have been more than helpful and that he can see himself buying another Dewulf planter down the road.
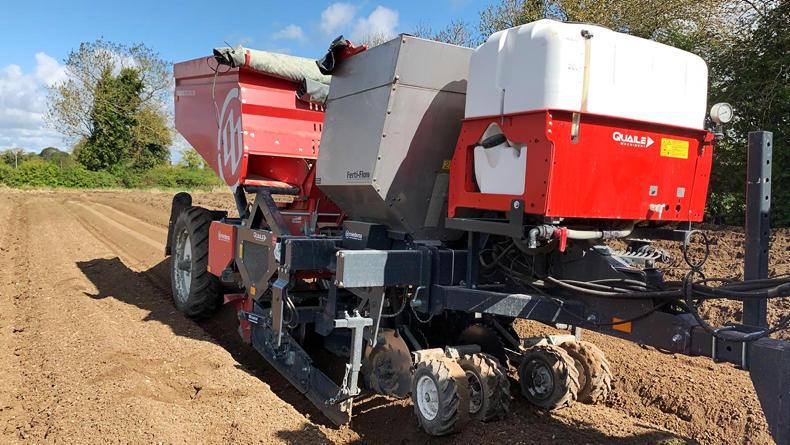
Dewulf potato planter.
Model: MS 2000. Number of rows: two.Weight empty: 2,700kg.Fertiliser capacity: 1,050kg.Hydraulic requirements: minimum of 50l/min.Required tractor: minimum of 70hp.List price: prices starting from €61,150 excluding VAT.
Farming more than 2,750 acres in Navan, Co Meath, the Smith family was one of two Irish potato growers to buy one of the new trailed two-row Dewulf planters ahead of the 2019 season. One year on and Andrew explained that they have been very impressed with the Dutch-built machine.
Why Dewulf?
Previously running a two-row Miedema mounted planter, the Smiths liked the reliability of the machine. Although they bought a new Dewulf planter, some of our readers will be aware that in November 2014, the Belgian company Dewulf and the Dutch company Miedema signed an acquisition agreement.
The family looked elsewhere in the market, but felt that the Dewulf planter was the best all-round and most competitively priced machine for their business. A big factor was the quality of bed it produced.
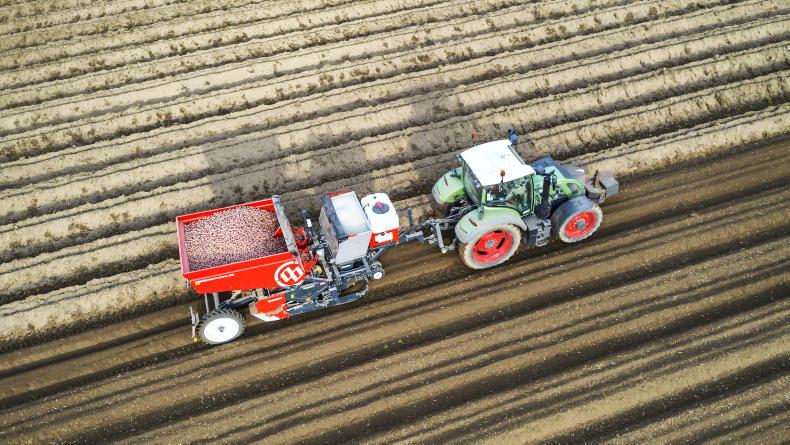
A huge plus for Andrew was the fact the sprayer and fertiliser dispensing rates are infinitely adjustable and will automatically reset to the desired rate based on the tractor's forward speed.
Picture: Adrian Leech Photography
Andrew acknowledged that moving from a 2005 planter to a new machine last year brought about huge technological advances and increases in efficiencies, which will go a long way towards helping pay for the new machine.
Mounted v trailed
Andrew noted that moving from a mounted to a trailed machine hindered manoeuvrability, as it’s much longer. However, once he got used to the trailed machine, this wasn’t an issue. The move to the trailed planter also improved visibility.
The big reason they moved to a trailed machine was to carry more seed potatoes and more fertiliser. Andrew noted that the trailed machine is capable of carrying one tonne of fertiliser and two to three tonnes of seed, a step up from the mounted planter, which only had capacity for 500kg of fertiliser and 1,200kg of seed.

The big reason the Smiths moved to a trailed machine was to carry more seed potatoes and more fertiliser. \Adrian Leech Photography
With an emphasis on efficiency, Andrew tries to operate and load the planter by himself. The fact that he has more than doubled his input-carrying capacity means that he has halved the time the planter is idle, waiting to be loaded.
Depending on the seeding rate, Andrew felt that he can now save at least 10 to 15 minutes every hour. This means he is able to keep up with the two Grimme CS150 de-stoners working ahead of him.
Another advantage to the new machine is the simplicity of detaching it from the tractor in the event of an issue.
“With our older mounted planter, if for some reason we had to change the tractor, it created a lot of hassle. With the trailed machine, everything is much more fluent and easier,” Andrew said.
How it works
The Dewulf MS2000 is a structural belt planter. Its planting system is designed to limit friction between the tubers, preventing damage to the seed potato.
A supply conveyor brings the seed potatoes from the hopper on to the wide belt bed with planting belts and returning belts.
Each row has six planting belts which bring the potatoes to the foam roller. The vibrating chute below the planting belts takes care of the singling and the excess potatoes are taken back to the rear board by the returning belts.
The belt bed is shaped so that each returning belt runs a little faster than the one next to it, which is beneficial in terms of filling of the belt bed.
On the last stretch of the planting belts, the potatoes are slowed down by the slightly slower running foam rubber roller. This speed reduction has a slight damming effect that presses the potatoes tightly against one another.
The position of the foam roller allows the potatoes to fall vertically into the furrow.
The V-shaped furrow opener is equipped with a small chisel that makes a sharp furrow. Dewulf claims that the loose soil created at the bottom prevents the seed potato from rolling. The shape of the furrow opener also crumbles a small amount of loose soil on top, which clamps the tuber in the furrow. The planting depth is set by means of the large depth control wheels mounted on the opener beam, on which the furrow openers are also mounted.
The parallelogram suspension is responsible for the constant planting depth, even across the width of the machine.
Features
One feature that has impressed Andrew is known as hill-master. On his previous planter, Andrew regularly encountered problems with seed flow when working up and down hills.
When planting downhill, the older machine had a tendency to double-plant, allowing extra seed potatoes to be planted due to the flow of gravity. When planting uphill, the opposite would happen. However, automatic hydraulic adjustment on his new machine ensures the belt bed is filled optimally. It helps to take stress off the operator, while saving seed.
Another feature Andrew noted he couldn’t be without is the tipping automat. “The hopper will tilt itself up and down as required to ensure the supply belts are always fed with a sufficient quantity of seed potatoes. This function works automatically and will recognise when coming to a headland, so there’s no waste. On my previous planter, this was manually operated through a spool valve. The automation helps to remove any operator error, also making it easier on the driver,” outlined Andrew.
Andrew was impressed with the MR-control system, which automatically adjusts the machine to help create a uniform ridge. Through this feature, sensors continuously measure the quantity of loose soil in the ridging hood, rather than pressure in the hydraulic cylinders. If needs be, the position of the ridging hood is automatically adjusted.
Technology
A huge plus for Andrew was the fact that the sprayer and fertiliser dispensing rates are infinitely adjustable and will automatically reset to the desired rate based on the tractor’s forward speed.
Another improvement on his previous machine is the way in which the fertiliser is placed between large discs located 5cm (2in) to the right and left of the seed potato.
His previous system wasn’t as accurate and Andrew feels the tubers will now get a better start, contributing to an overall greater yield come harvesting.
Andrew operates the planter on his 2016 Fendt 724. Although he didn’t spec the tractor with auto-steer at the time, he has noted his next tractor will be equipped with full real-time kinematic (RTK). Instead, he uses a T-jet system, the same as what he uses on his Bogballe fertiliser spreader.
The GPS co-ordinates of the field are collected by driving around the headlands. Once the field map is set up, this system controls the machine’s section control, the auto knock-on and -off of the rows. As it’s a two-row planter, it has two sections. Andrew said that he only got the section control up and running properly this year, but has noted significant cost savings.
“Our old machine was ground-drive. With this, we had wastage in two ways. Firstly, when we lifted the planter at the headlands, the wheel would keep turning and seed would continue to come out. Secondly, we would always be inclined to sow a little extra where the headland met the run to ensure enough seed is set. It’s difficult to quantify the exact savings, but at €600/t for certified Rooster seed, I can often see half a tonne being saved in most fields,” explained Andrew.
In the cab, the control layout is quite simple. Andrew has four cameras linked to one screen while all the planting statistics are displayed on the operating terminal.

Andrew has four cameras linked to one screen while all the planting statistics are displayed on the operating terminal.
It’s straightforward to connect a GPS signal from the tractor or standalone system to the planter’s control system.
When we spoke with Andrew, he was almost finished up on his second planting season with the machine.
He noted that the planter is user-friendly – so much so that an inexperienced operator could pilot the machine. He only highlighted two faults.
Firstly, he was disappointed that it didn’t come with a hopper cover.
To overcome this, he retrofitted a cover he designed himself.
Secondly, he felt that the discs where the fertiliser is applied have trouble working in wet conditions.
Technological advances
Although he didn’t go for a wider planting width, he’s been more than impressed with the technological advances and increased efficiencies, which have helped him to increase his output to between 8ha and 10ha per day (20 to 25 acres).
He added that the team at Quaile Machinery have been more than helpful and that he can see himself buying another Dewulf planter down the road.
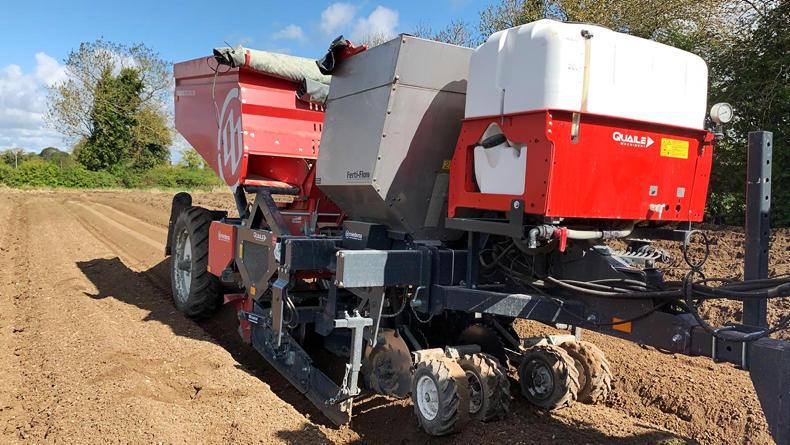
Dewulf potato planter.
Model: MS 2000. Number of rows: two.Weight empty: 2,700kg.Fertiliser capacity: 1,050kg.Hydraulic requirements: minimum of 50l/min.Required tractor: minimum of 70hp.List price: prices starting from €61,150 excluding VAT.
SHARING OPTIONS: