A new dairy cow cubicle shed has been completed on the McCracken family farm in Lissan, Co Tyrone, representing a significant investment in the farm business.
New shed for part-time dairying.
The dairy enterprise is unusual as it is run on a part-time basis. Kevin McCracken works as a full-time architect in nearby Magherafelt.

Kevin McCracken farms at Lissan, Co Tyrone.
He milks before and after work with help from his father, Sean, who also has full-time employment off-farm. Kevin’s grandfather, Patrick, is also at hand to help with farm work and offer advice.
There are 30 mainly Friesian-type cows being milked on the farm at present. The new shed contains 32 cubicles, and the long-term aim is to gradually increase the herd, while continuing to run the farm on a part-time basis.
The new building is a four-bay, apex shed, with a central feed passage and a single row of cubicles on each side.
“We did the project in phases. This let us spread the costs out and gave us time to do as much of the work ourselves as possible. Cows got into the shed for the first time in December,” Kevin said.
Phases
The first tank was started in 2016. It is 70ft by 13ft and when completed, it effectively doubled slurry storage capacity on the farm. A second tank, spanning 70ft by 35ft, went in the following year. In the third year, the new tanks were slatted, and construction of the shed began.
Overall, the project took four years to complete. There was no grant support used for any of the new shed or tanks and it had a total cost of approximately £60,000.
At just under £2,000/cow, Kevin acknowledges that the building is slightly more expensive than is sometimes recommended, but he points out that there is enough slurry storage to last 60 cows for six months. This will mean future expansion will be cheaper and the extra slurry storage is invaluable in an area where winters can be long.
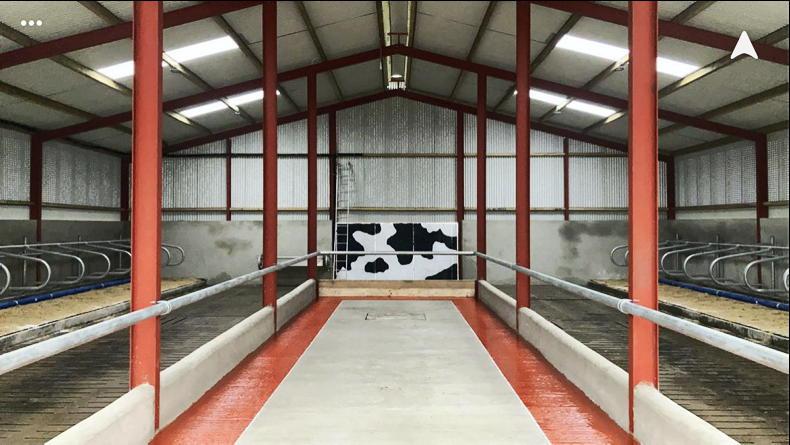
Extra feed space will not be required when Kevin extends the shed and ups cow numbers.
The feed passage is 14ft wide and runs for three of the four 15ft bays, which provides a crossover space at the back so there are no dead ends.
Cows are fed grabs of silage from an existing pit and bales are also fed occasionally. A single pipe neck rail is used as the feed barrier.
Concrete blocks were built for the bottom of the feed barrier along the two sides.
At the end, two wooden planks were used instead, and the neck rail can be screwed off easily with two bolts. This is to allow access to a slurry mixing point inside the shed.
Both slurry tanks in the shed are 8ft deep and there are no supportive piers. Kevin said that having internal shuttered walls instead should make it easier for slurry to circulate in the tanks at mixing.
Structure
The shed is 14ft high at the eaves and it has a 15-degree pitched roof. On the gable wall facing the yard, there are double-sliding doors at the feed passage and two swinging doors give access to the slats and cubicles.
“We are on an exposed site, so we have good air flow anyway. To maximise that, we have perforated sheeting around three sides, and timber cladding space boarding is on the front gable,” Kevin said.
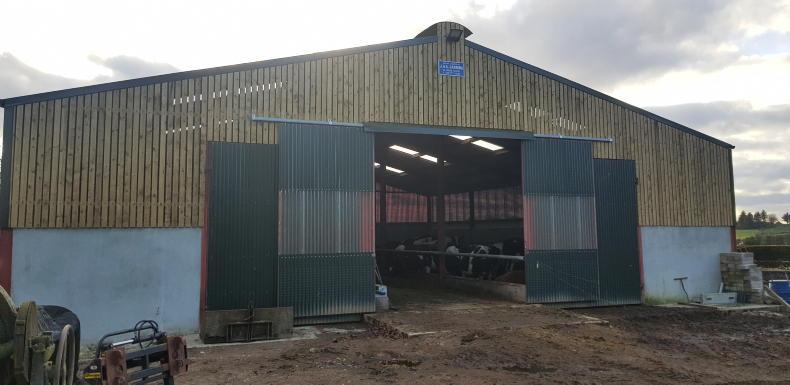
There is timber cladding space boarding on the front gable.
“There is a raised ridge to let air escape from the shed and there is also a space between the top of the wall and tin sheeting to allow air to flow in,” he added.
There is a 12ft 6in slatted area between the feed passage and the cubicles on both sides. One row of cubicles is above a tank and the exterior shed wall in 14in. The other row is on solid ground and this wall is only 12in.
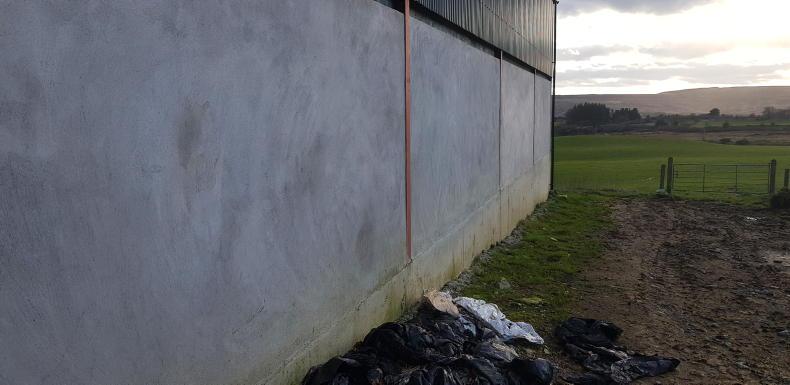
Kevin kept this shed wall thicker so that it would be flush with tank wall at the exterior.
The wider wall stems from the tank wall needing six inches to support the cubicles and eight inches for the shed’s steel work. The shed is built on a slope and the tank wall can therefore be seen from the outside. Kevin kept the shed wall thicker, so that it would be flush with tank wall at the exterior.
Planning for gradual herd expansion
Space was left for a door in the middle of the far gable wall so that the shed could be extended when cow numbers increase in the future.
“The idea is to eventually continue this shed out another two bays and put in four rows of cubicles. That would leave us with another 32 cubicles and there is ample feed space for over 50 cows in the existing shed already. We would be happy running a herd of 50 or 60 cows. It would suit the amount of land we have around the yard and would allow us to keep our off-farm jobs,” Kevin said.
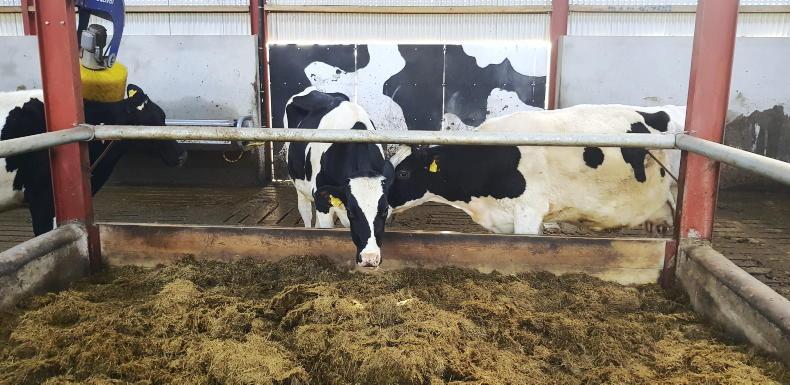
Space was left for a door in the middle of the far gable wall so that the shed could be extended.
In the new four-bay shed, Kevin put in two rows of cubicles instead of three, so that he would not have to build extra feed space in the extension. He also points out that three rows of cubicles would mean the feed barrier would face outside.
“Perimeter feeding was not an option due to the natural fall of the site and the exposed location which brings heavy rain and strong wind. The central feed passage gives more flexibility for batching cows into smaller groups as well,” Kevin said.
Parlour
Before more cubicle housing is built, the next phase of development on the farm surrounds the milking facilities. At present, cows are milked in a byre system with 12 stands and six milking units.
Kevin has already purchased a second-hand parlour. It was originally a seven-a-side double-up, but the plan is to convert it to a 14-a-side swingover.
The new parlour and collecting yard will also be built beside the cubicle shed, where outdoor cattle handling facilities are located at present.
Kevin already has girders in the yard for the new building and hopes to start construction later this year.
Would a robot not suit Kevin’s setup better, given the small herd size and limited labour availability?
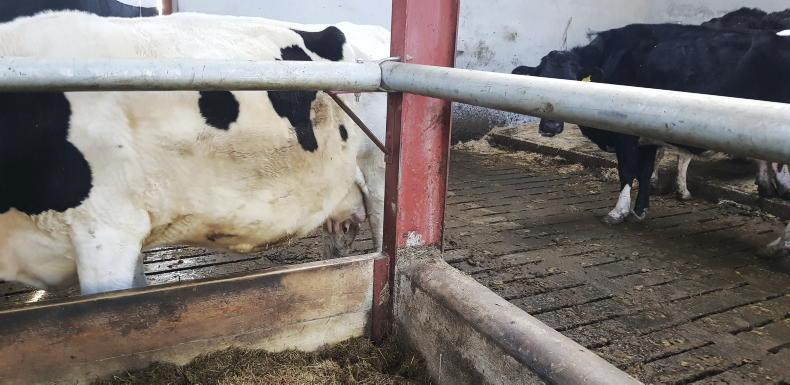
This run of feed barrier can be dismantled easily to give access to a slurry mixing point.
“I put a lot of thought into going down the robotic route. I have a space designated in the future extension that will accommodate a robot, but in the short term I feel that I cannot justify it,” Kevin responds.
Firstly, his low input, British Friesian-type cows would not respond to more frequent milking in the same way that high-yielding, Holstein cows do. He wants to keep cows at grass and is not convinced that robots work effectively in grazing systems. Also, a robot would add significant cost to the buildings work and Kevin feels that this money can be invested in better ways on his farm.
“In the 14-unit parlour, I hope to have 60 cows milked and washed up in an hour so that I can go on to my work knowing that the cows have been taken care of,” he said.
A new dairy cow cubicle shed has been completed on the McCracken family farm in Lissan, Co Tyrone, representing a significant investment in the farm business.
New shed for part-time dairying.
The dairy enterprise is unusual as it is run on a part-time basis. Kevin McCracken works as a full-time architect in nearby Magherafelt.

Kevin McCracken farms at Lissan, Co Tyrone.
He milks before and after work with help from his father, Sean, who also has full-time employment off-farm. Kevin’s grandfather, Patrick, is also at hand to help with farm work and offer advice.
There are 30 mainly Friesian-type cows being milked on the farm at present. The new shed contains 32 cubicles, and the long-term aim is to gradually increase the herd, while continuing to run the farm on a part-time basis.
The new building is a four-bay, apex shed, with a central feed passage and a single row of cubicles on each side.
“We did the project in phases. This let us spread the costs out and gave us time to do as much of the work ourselves as possible. Cows got into the shed for the first time in December,” Kevin said.
Phases
The first tank was started in 2016. It is 70ft by 13ft and when completed, it effectively doubled slurry storage capacity on the farm. A second tank, spanning 70ft by 35ft, went in the following year. In the third year, the new tanks were slatted, and construction of the shed began.
Overall, the project took four years to complete. There was no grant support used for any of the new shed or tanks and it had a total cost of approximately £60,000.
At just under £2,000/cow, Kevin acknowledges that the building is slightly more expensive than is sometimes recommended, but he points out that there is enough slurry storage to last 60 cows for six months. This will mean future expansion will be cheaper and the extra slurry storage is invaluable in an area where winters can be long.
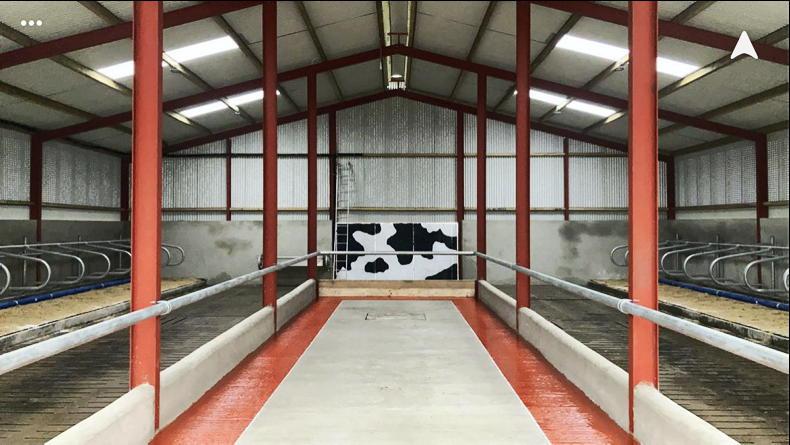
Extra feed space will not be required when Kevin extends the shed and ups cow numbers.
The feed passage is 14ft wide and runs for three of the four 15ft bays, which provides a crossover space at the back so there are no dead ends.
Cows are fed grabs of silage from an existing pit and bales are also fed occasionally. A single pipe neck rail is used as the feed barrier.
Concrete blocks were built for the bottom of the feed barrier along the two sides.
At the end, two wooden planks were used instead, and the neck rail can be screwed off easily with two bolts. This is to allow access to a slurry mixing point inside the shed.
Both slurry tanks in the shed are 8ft deep and there are no supportive piers. Kevin said that having internal shuttered walls instead should make it easier for slurry to circulate in the tanks at mixing.
Structure
The shed is 14ft high at the eaves and it has a 15-degree pitched roof. On the gable wall facing the yard, there are double-sliding doors at the feed passage and two swinging doors give access to the slats and cubicles.
“We are on an exposed site, so we have good air flow anyway. To maximise that, we have perforated sheeting around three sides, and timber cladding space boarding is on the front gable,” Kevin said.
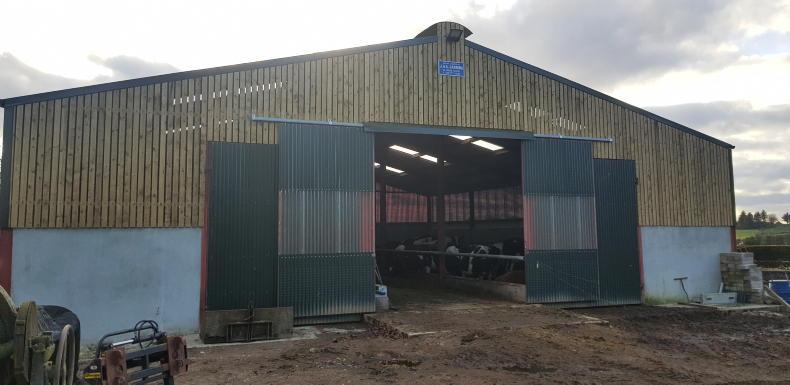
There is timber cladding space boarding on the front gable.
“There is a raised ridge to let air escape from the shed and there is also a space between the top of the wall and tin sheeting to allow air to flow in,” he added.
There is a 12ft 6in slatted area between the feed passage and the cubicles on both sides. One row of cubicles is above a tank and the exterior shed wall in 14in. The other row is on solid ground and this wall is only 12in.
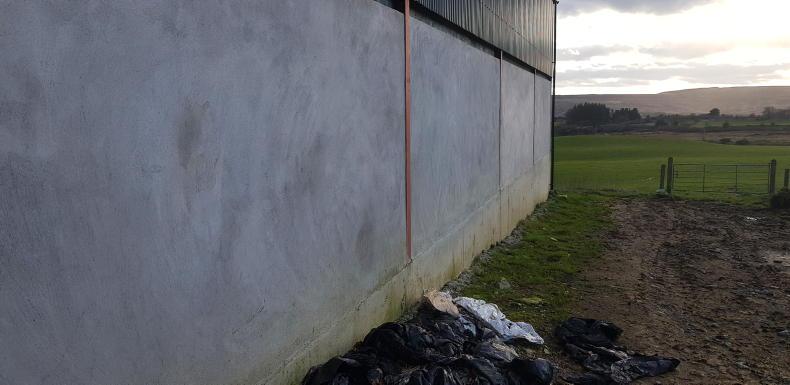
Kevin kept this shed wall thicker so that it would be flush with tank wall at the exterior.
The wider wall stems from the tank wall needing six inches to support the cubicles and eight inches for the shed’s steel work. The shed is built on a slope and the tank wall can therefore be seen from the outside. Kevin kept the shed wall thicker, so that it would be flush with tank wall at the exterior.
Planning for gradual herd expansion
Space was left for a door in the middle of the far gable wall so that the shed could be extended when cow numbers increase in the future.
“The idea is to eventually continue this shed out another two bays and put in four rows of cubicles. That would leave us with another 32 cubicles and there is ample feed space for over 50 cows in the existing shed already. We would be happy running a herd of 50 or 60 cows. It would suit the amount of land we have around the yard and would allow us to keep our off-farm jobs,” Kevin said.
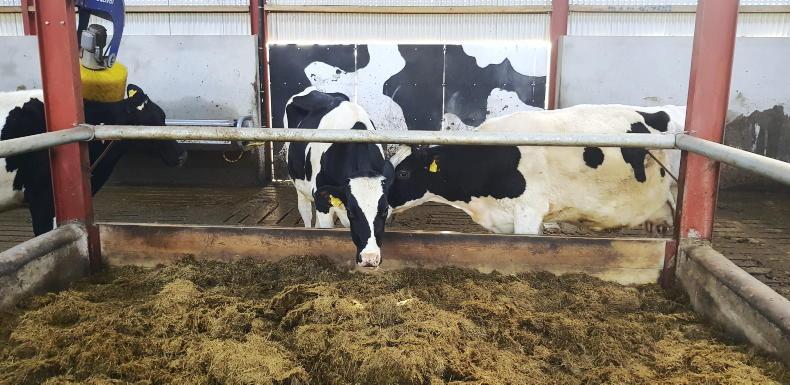
Space was left for a door in the middle of the far gable wall so that the shed could be extended.
In the new four-bay shed, Kevin put in two rows of cubicles instead of three, so that he would not have to build extra feed space in the extension. He also points out that three rows of cubicles would mean the feed barrier would face outside.
“Perimeter feeding was not an option due to the natural fall of the site and the exposed location which brings heavy rain and strong wind. The central feed passage gives more flexibility for batching cows into smaller groups as well,” Kevin said.
Parlour
Before more cubicle housing is built, the next phase of development on the farm surrounds the milking facilities. At present, cows are milked in a byre system with 12 stands and six milking units.
Kevin has already purchased a second-hand parlour. It was originally a seven-a-side double-up, but the plan is to convert it to a 14-a-side swingover.
The new parlour and collecting yard will also be built beside the cubicle shed, where outdoor cattle handling facilities are located at present.
Kevin already has girders in the yard for the new building and hopes to start construction later this year.
Would a robot not suit Kevin’s setup better, given the small herd size and limited labour availability?
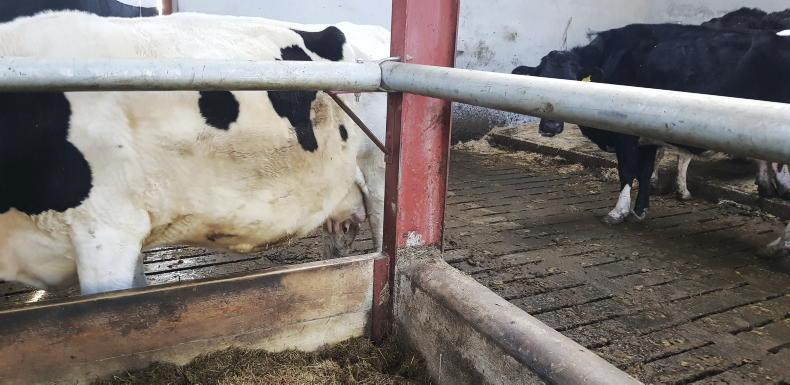
This run of feed barrier can be dismantled easily to give access to a slurry mixing point.
“I put a lot of thought into going down the robotic route. I have a space designated in the future extension that will accommodate a robot, but in the short term I feel that I cannot justify it,” Kevin responds.
Firstly, his low input, British Friesian-type cows would not respond to more frequent milking in the same way that high-yielding, Holstein cows do. He wants to keep cows at grass and is not convinced that robots work effectively in grazing systems. Also, a robot would add significant cost to the buildings work and Kevin feels that this money can be invested in better ways on his farm.
“In the 14-unit parlour, I hope to have 60 cows milked and washed up in an hour so that I can go on to my work knowing that the cows have been taken care of,” he said.
SHARING OPTIONS: